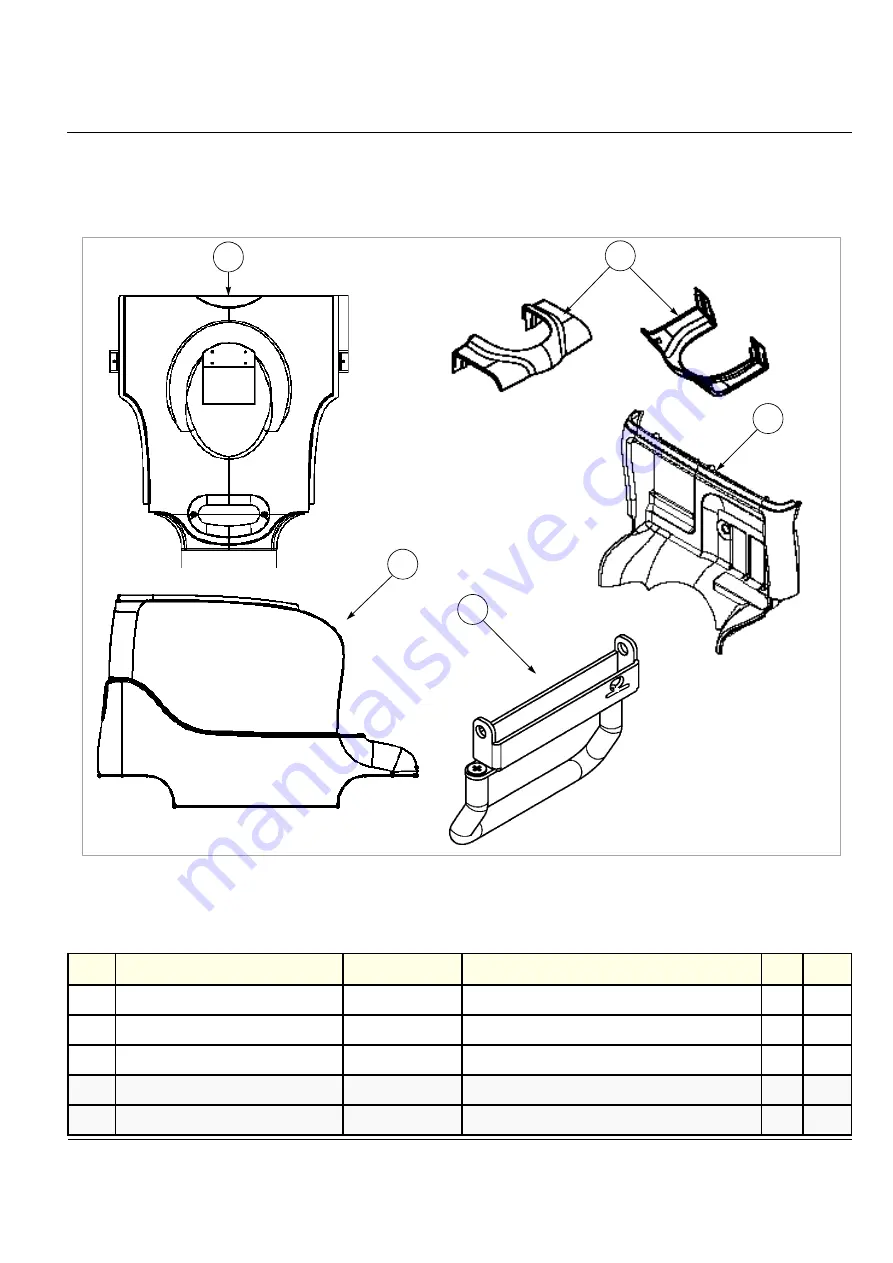
GE M
EDICAL
S
YSTEMS
D
IRECTION
2392751-100, R
EVISION
3
V
IVID
™ 4 S
ERVICE
M
ANUAL
Chapter 9 - Renewal Parts
9-3
Section 9-3
Renewal Parts Lists and Diagrams
9-3-1
Mechanical Hardware Parts
Figure 9-1 Mechanical Hardware Parts - Diagram 1
Table 9-2
Mechanical Hardware Parts - Diagram 1
Item
Part Name
Part Number
Description
Qty
FRU
101
Cover Rear
2258594
1
2
102
Cover Connector Panels
2258596
1
2
103
Cover Front
2258597
1
2
104
Cover Left
2258599
1
1
105
Up/Down/Swivel Handle V4
2370002-2
1
1
101
103
102
105
104