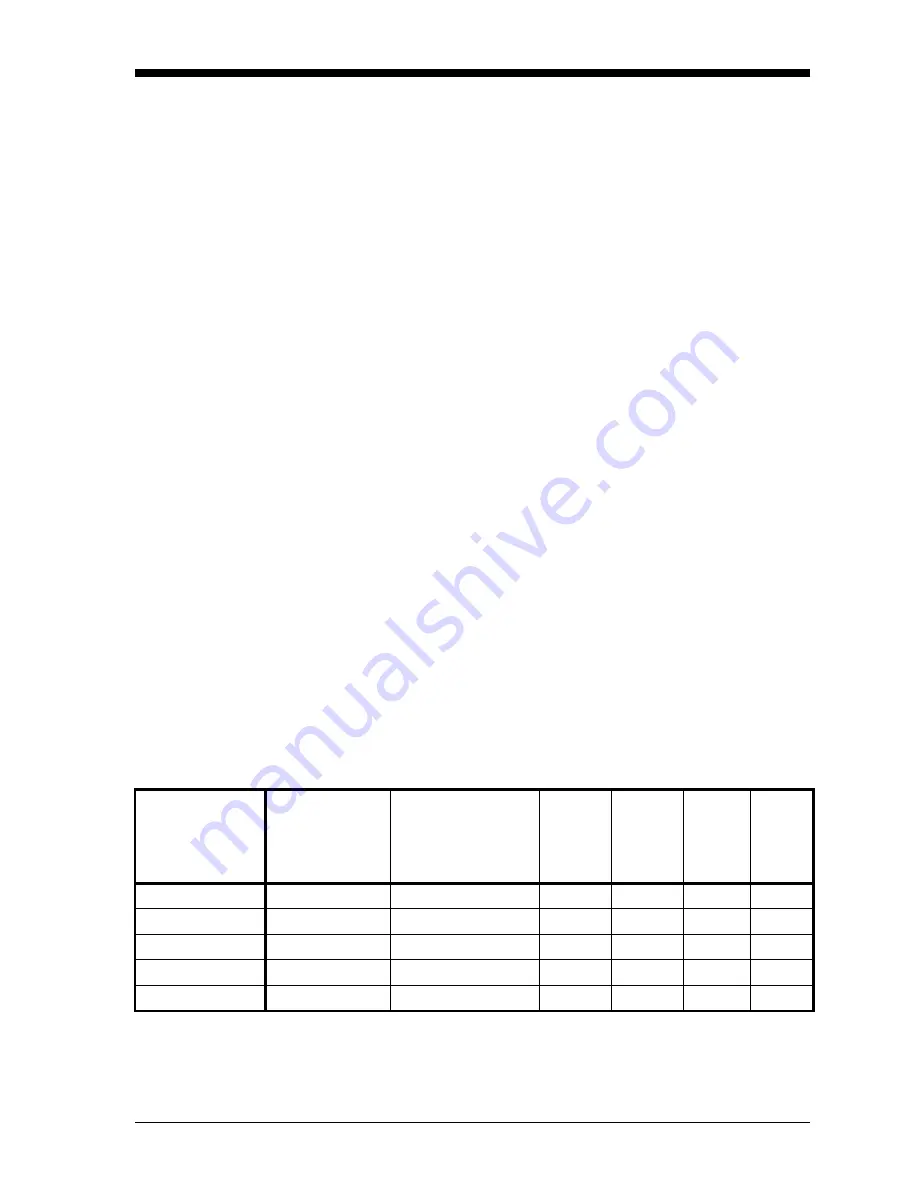
Installation
1-9
March 2004
Wiring the RS232 Serial
Port
The Model UTX878 flow transmitter is equipped with a built-in
RS232 serial communications port. Proceed to the section below for
wiring instructions. For more information on serial communications,
refer to the
EIA-RS Serial Communications
manual (916-054).
Use the serial port to connect the Model UTX878 flow transmitter to
an ANSI terminal or a personal computer. The RS232 interface is
wired as Data Terminal Equipment (DTE), and the signals available
at the COMMUNICATION terminal block are shown in Table 1-1
below.
1.
Follow the instructions on page 1-4 to prepare the unit before you
connect power.
2.
Use the information in Table 1-1 below to construct a suitable
shielded cable for connecting the Model UTX878 to the external
device. If desired, an appropriate cable may be purchased from GE
Panametrics.
Note:
The DTR and RTS signals power the UTX878 communication
circuit and are required for proper operation. Consult the
factory if you have additional questions.
Note:
Signal names that imply direction (e.g., transmit and receive)
are named from the point of view of the DTE device (the GE
Panametrics meter is usually considered the DTE device).
When the RS232 standard is strictly followed, these signals
are labeled with the same name and pin # on the DCE device
side as well. Unfortunately, the convention is not followed
because the DTE and DCE side get confused. Therefore,
connections that imply direction are changed to reflect their
direction on the DCE side.
Table 1-1: RS232 Connection to DCE or DTE Device
Communication
TB4
Colors for GE
Panametrics
Cable (flying
leads)
Signal
Description
DCE
DB25
Pin #
DCE
DB9
Pin #
DTE
DB25
Pin #
DTE
DB9
Pin #
1
Brown
DTR 20
4
20
4
2
White
RTS
4
7
4
7
3
Black
Signal Ground
7
5
7
5
4
Red
UTX878 (Transmit)
2
3
3
2
5
Green
UTX878 (Receive)
3
2
2
3
Summary of Contents for UTX878 Ultrasonic
Page 2: ...iii March 2004 The UTX878 Flow Transmitter and Transducers ...
Page 8: ...Chapter 1 ...
Page 20: ...March 2004 Installation 1 11 Figure 1 5 UTX878 Outline and Installation Dwg 712 1196 rev 2 ...
Page 22: ...March 2004 Installation 1 13 Figure 1 7 UTX878 Wiring Diagram Dwg 702 528 rev 2 ...
Page 23: ...Chapter 2 ...
Page 45: ...Chapter 3 ...
Page 52: ...Chapter 4 ...
Page 60: ...Chapter 5 ...
Page 65: ...Chapter 6 ...
Page 75: ...Chapter 7 ...
Page 80: ...Appendix A ...
Page 85: ...Appendix B ...
Page 86: ...CE Mark Compliance Introduction B 1 EMC Compliance B 1 ...
Page 88: ...Appendix C ...
Page 89: ...Data Records Site Data C 1 ...
Page 93: ...Appendix D ...
Page 94: ...Service Record Introduction D 1 Data Entry D 1 Diagnostic Parameters D 3 ...