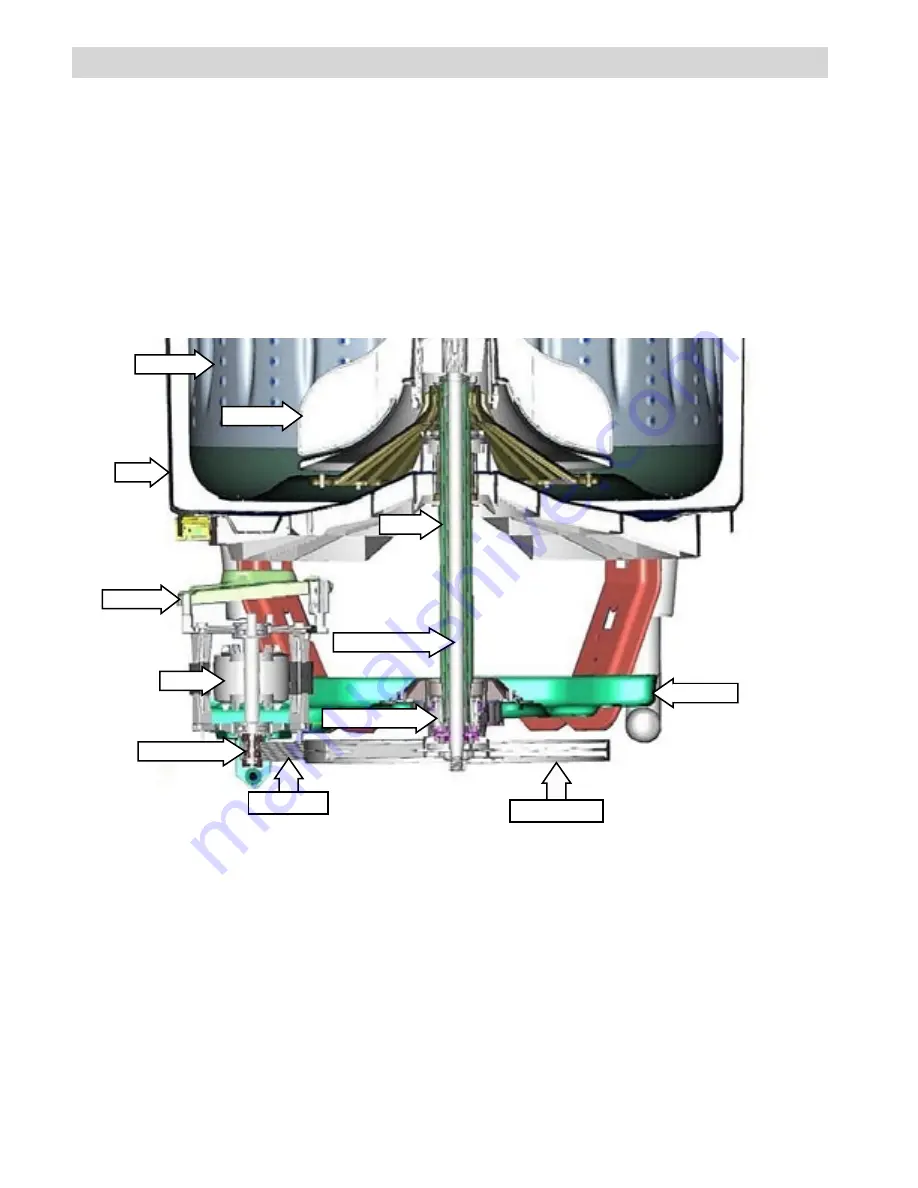
– 16 –
Shaft and Mode Shifter Overview
The shaft and mode shifter assembly consists of the shaft and tube, mode shifter cam, and mode shifter coil.
It operates in 2 distinct modes, spin and agitation.
The shaft and tube transfers power to the wash system. Motor power is transmitted to the shaft and tube
from the drive belt to the drive pulley. The drive pulley is attached to one end of the agitator shaft and the
agitator is attached to the other. The tube is fixed to the washer basket at all times.
The mode shifter changes the shaft and tube from spin to agitation. In agitation mode, the tube is fixed to the
platform and the agitator shaft rotates freely. In spin mode, the agitator shaft is fixed to the tube and both
rotate together.
Basket
Motor
Agitator
Motor Pulley
Mode Shifter
Drive Belt
Drive Pulley
Tub
Platform
Inverter
View from Right Side
Agitator Shaft
(Continued next page
)
Tube