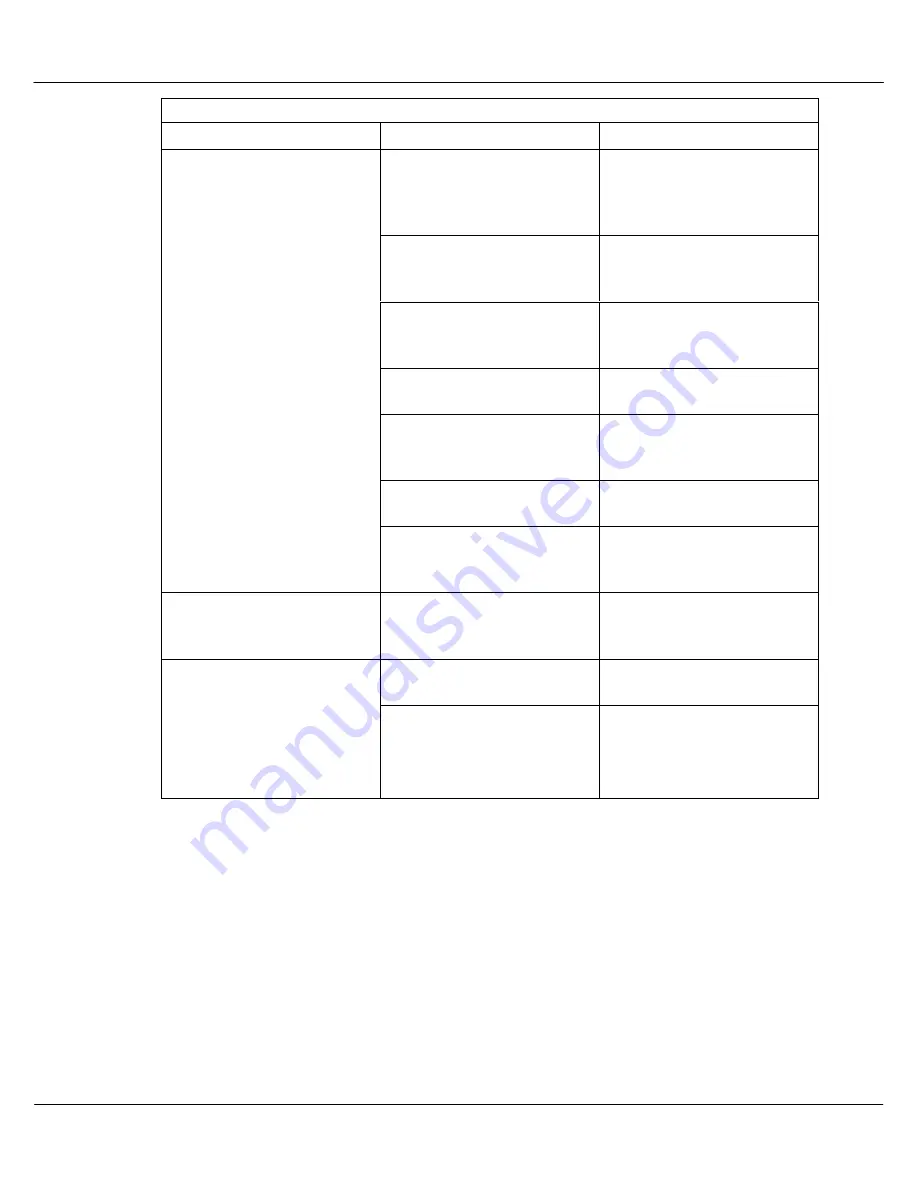
Troubleshooting
Troubleshooting possible faults
2018-9015-003
03-2015
Brakes
Symptom
Possible cause
Solution
The spreader partially
brakes or does not brake at
all.
The air brake hoses (red
and yellow/blue) are not
connected to the tractor
outlet.
Connect hoses.
The air brake hose
(yellow/blue) is not well
connected.
Connect the hose.
No air pressure in the
braking system or the air
pressure is below 4.83 bar.
Find air leaks and repair.
Check hoses, air tank and
hose fittings.
Air leaks from the hoses.
Find damaged, pinched or
defective hoses and repair.
The brake linings are worn
out.
Refer to section Advanced
maintenance - Changing air
brake parts.
A slack adjuster is not
properly adjusted.
Refer to section Advanced
maintenance - Calibration.
Oil and water in the braking
system.
Purge air tank 3-4 seconds
by pulling on the steel wire
located under the spreader.
The spreader brakes do not
release.
The emergency brake (red)
hose is not connected.
Connect the red hose on
the proper outlet of the
tractor.
The spreader does not
brake evenly.
A slack adjuster is not
properly adjusted.
Refer to section Advanced
maintenance - Calibration.
A brake lining is worn out.
Change brake lining.
Refer to section
Maintenance - Air brake -
Changing air brake parts.