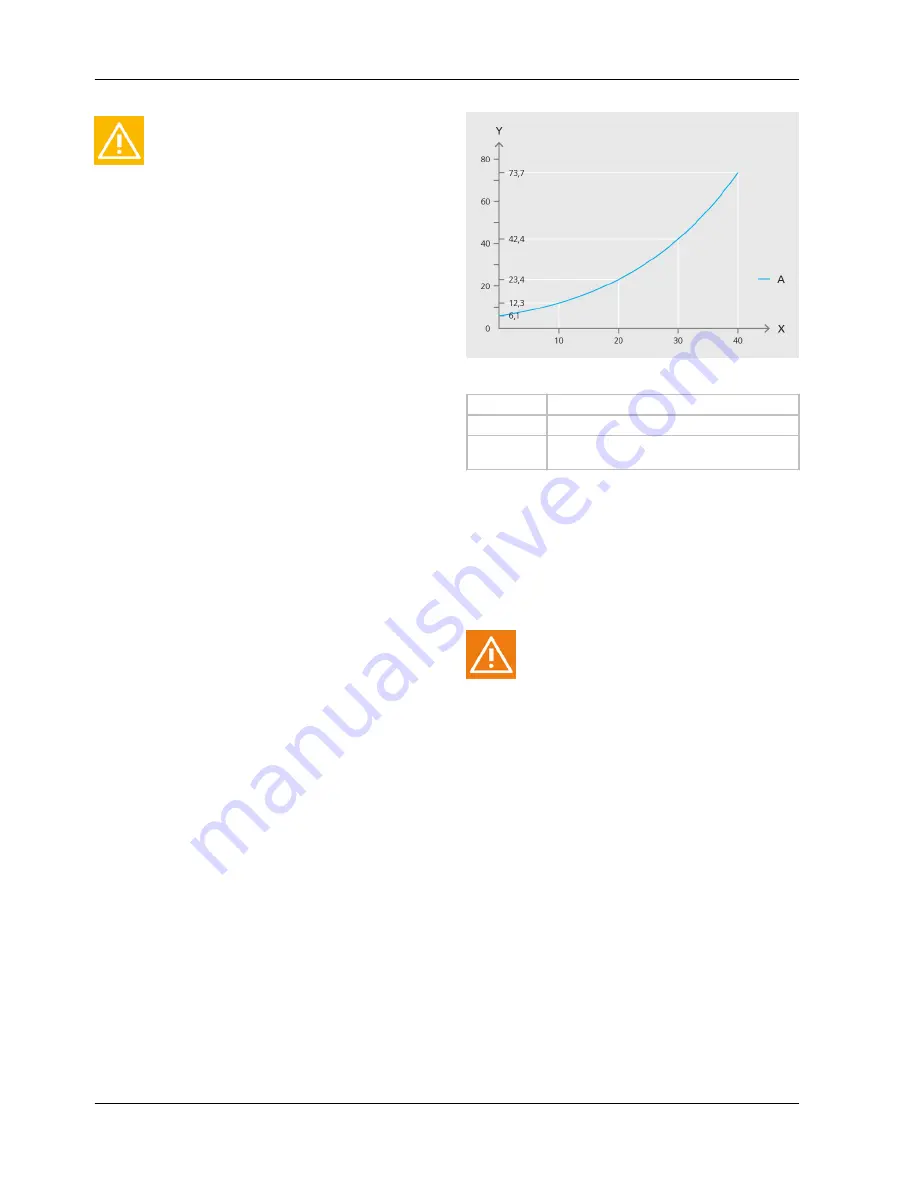
Caution!
Checking devices which could be
damaged by the specified test pres-
sure must be removed or blocked
before the leak test is performed.
A record should be kept of the pressure test, noting
the pressure in the pipes tested, the ambient temper-
ature and the outside temperature in the shade at
hourly intervals.
The removed measuring and control instruments
should be reinstalled after completion of the leak test
and if there are no leaks in the package/chiller.
Test strategy
Dry nitrogen is used as the test medium. After reach-
ing the test pressure, the pressure drop is measured
via the differential pressure measurement. This may
only change by 0.02 bar within an hour. If the display
device does not indicate a leakage through foam for-
mation, the system is sealed.
Testing devices
A pressure gauge with an accuracy of 0.5% over the
entire measuring range, with a digital resolution of
0.01 bar must be used for the measurement.
The testing described here is based on pressure
gauges with pressure gauge and LEAK mode from
Keller.
Display devices
A foaming agent must be used as the means to indi-
cate leakages. A solution of 50 parts water and 1
part detergent can be used as the foaming agent.
Leaks are detected through formation of foam. A
leak detection spray can be used in problem areas.
Carrying out the test
1. Wet all connecting joints (welded seams, flange
connections, screw fastenings, etc.) with foaming
agent. Remedy any leaks detectable from the
noticeable formation of foam.
8.5.3
Drying, vacuum
After the leak tightness test has been completed, the
plant must be evacuated and undergo a vacuum test
for 3 hours. Evacuation is used to remove air and
moisture from the plant.
A vacuum pump must be used for evacuation.
The permissible increase in vacuum is maximum
6.66 mbar over a period of 3 hours.
fig.29:
Vacuum required to remove moisture from refrigerating
plants
X
Room or Wall temperature in °C
Y
Vacuum in mbar
A
Vacuum required to remove moisture from
refrigerating plants
Measured values have to be checked and recorded
hourly after reaching the required vacuum. After the
vacuum pressure, the temperatures in the machine
house and the outdoor temperature in shade must
be entered in the log. After the vacuum test, the
pressure compensation must be carried out with
NH
3
.
Warning!
Shut the oil pump during evacuation!
See also "Evacuation on refrigerant side" in the
chapter "Maintenance work".
Start-up
Operating Manual | GEA Grasso M-Series
Screw Compressor Packages
56
GEA Refrigeration Germany GmbH | P_261511_1 | Generated 01.04.2015
Summary of Contents for Grasso M-Series
Page 88: ......