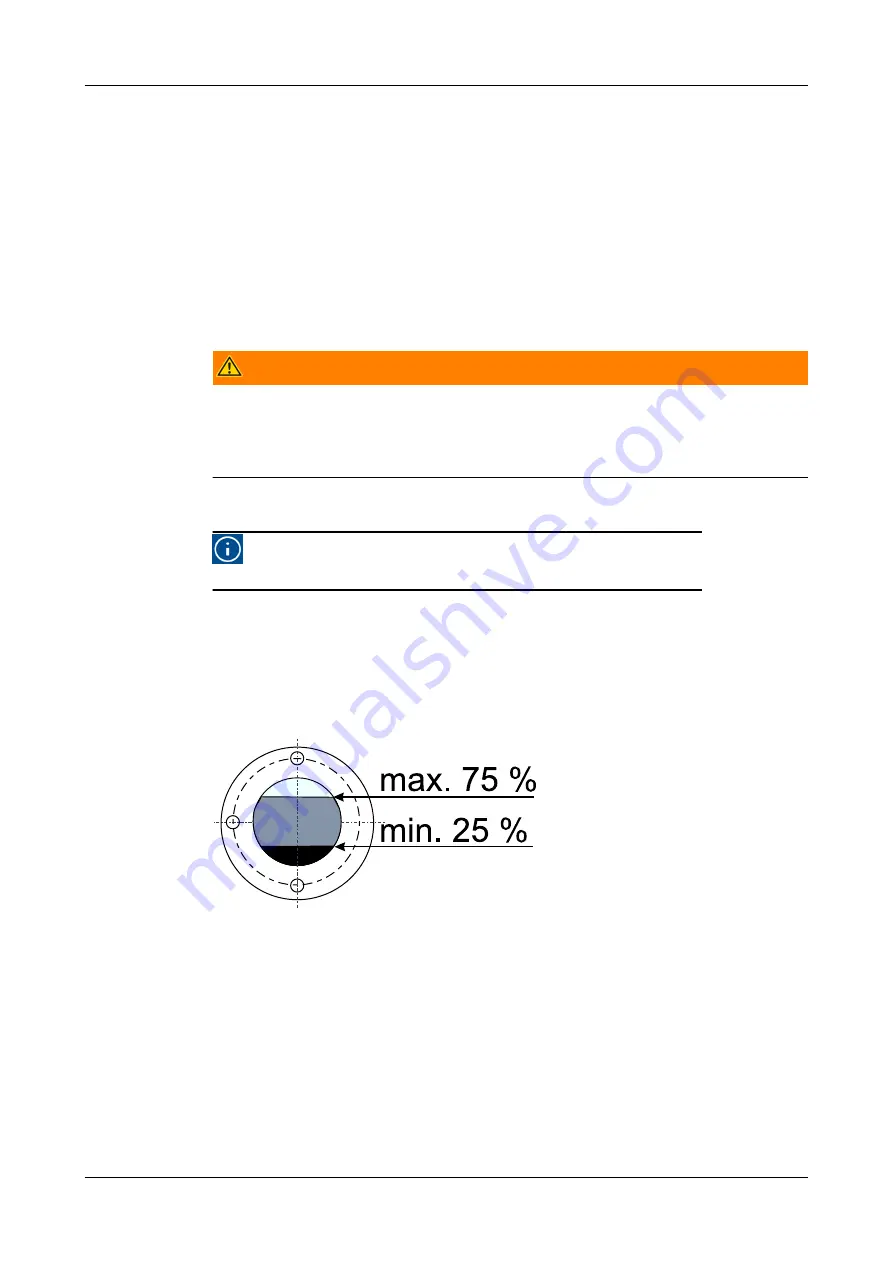
iii.
Place a moisture absorbing compound (eg a dessicant such as silica gel)
inside the control cabinet.
iv.
Place warning tags on the electric system and all closed stop valves.
Prior to starting up after a shut down, change the oil and exchange the oil filters.
Determine the starting and stopping procedure from prior to start the compressor.
2.4
LUBRICATION DATA
Determine max Toil and set this value in the safety device.
Change the oil as soon as an oil analysis indicates contaminated oil.
Warning!
It is expressly pointed out that it is not permitted to mix different types
of oil. If another type of oil is used, first remove all the stale oil in the
filters, oil pump, crankcase, shaft seal, oil separator and oil drains of
the installation.
2.4.1
Topping up oil with compressor operating
Hint!
Use Grasso’s hand-operated oil pump, part. no. 18.13.121
Topping up oil is permitted during compressor operation.
Be sure that this oil is the same as in the plant (refer to Section 2.4, Page 34).
Without affecting the operation of the compressor, the oil may be topped up by
means of a separate oil pump. This pump enables the oil to be forced into the
crankcase via the oil charging valve, against suction pressure.
Fig.14:
Oil level in compressor sight glass
2.5
EVACUATION, LEAK TESTING AND START-UP OF THE COMPRESSOR/PACKAGE
To evacuate the refrigeration system refer to Section 1.4.2, Page 24,
Always use a vacuum pump or pump-down unit to evacuate the refrigerant from
the compressor.
2.5.1
EVACUATION OF REFRIGERANT BEFORE SERVICING
Procedure to evacuate the compressor:
INSPECTION AND TROUBLE SHOOTING
LUBRICATION DATA
P-NL-094_imm_VHS_English_13
34
26.07.2021