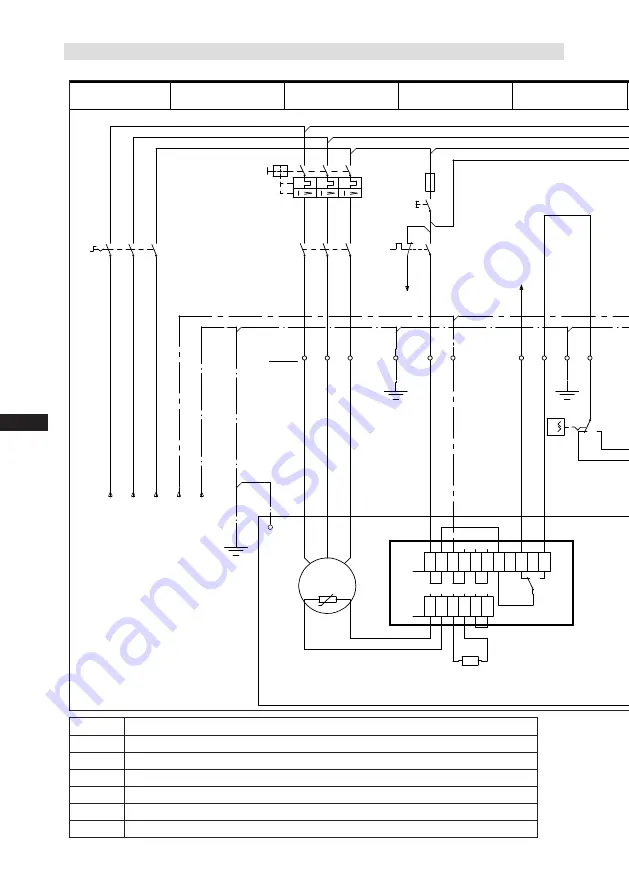
14
D
GB
F
E
96166-05.2012-DGbFEI
5.3 Circuit diagram direct start 230 V
∆
/ 400 V Y
Fig. 15
R1
Cold conductor (PTC sensor) motor winding
R2
Thermal protection thermostat (PTC sensor)
F1
Motor safety switches
F2
Control power circuit fuse
F3
Safety chain (high/low pressure monitoring)
B1
Release switch (thermostat/pressostat)
Q1
Main switch
Terminal box compressor