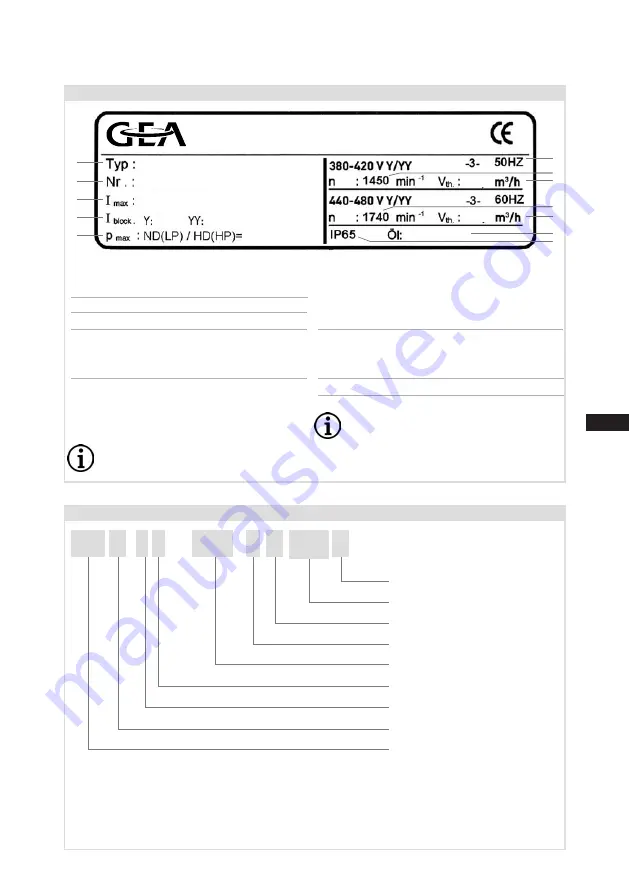
D
GB
F
E
7
96156-03.2016-DGb
1
2
3
4
5
6
7
8
9
10
11
12
13
1
Type designation
2
Machine number
3
maximum operating current
4
Starting current (rotor blocked)
Y: Part winding 1
YY: Part winding 1 and 2
5
ND (LP): max. permissible operating
pressure
(g)
Low pressure side
HD (HP): max. permissible operating
pressure
(g)
High pressure side
Observe the limits of
application diagrams!
50 Hz
60 Hz
6
Voltage, circuit, frequency
7
Nominal rotation speed
8 Displacement
9
Voltage, circuit, frequency
10 Nominal rotation speed
11 Displacement
12 Oil type filled at the factory
13 Terminal box protection type
Electrical accessories can change
the IP protection class!
}
}
Fig. 3
/
HG
3 4
290- 4
CO
2
X
2.3 Type key
(example)
¹
)
HG - Hermetic Gas-Cooled (suction gas-cooled)
²
)
X - Ester oil charge
³
)
ML - Normal cooling and deep freezing at low and medium evaporation temperatures
S - For frequency regulation and extended limits of application
SH - For high evaporating temperatures eg. heat pumps, different oil charge
Transcritical
CO
2
version
Compressor version ³
)
Number of poles
Swept volume
Numbers of cylinders
Size
Oil charge ²
)
Series ¹
)
T
S
1
2
3
4
5
6
7
8
9
10
11
12
13
AS12345-001
59,8 A
231 A
283 A
20,1
24,1
CO2,C 85 E
HGX34/230-4 S CO
2
T
100/150 bar
GEA Bock GmbH
72636 Frickenhausen, Germany
2
|
Product description
2.2 Name plate
(example)