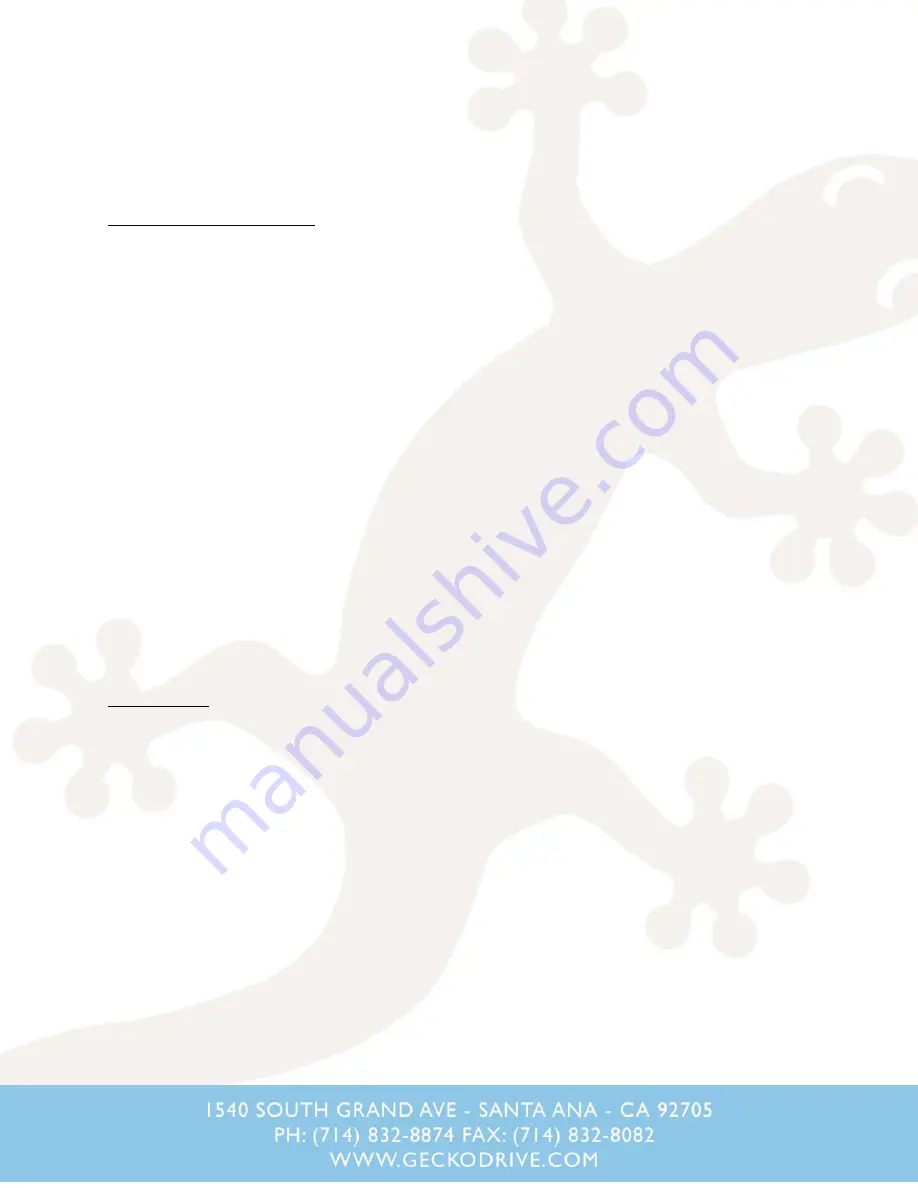
2
The G216 is a 7A, 80VDC step motor drive with an integrated voltage-controlled oscillator (VCO). It can be used as a step and
direction input motor drive or as a dual input speed controller, with user adjustable CW and CCW speeds and acceleration
profile. The operating mode and mode related functions are set via the 10-position slide switch on side of the drive. The G216
has 2 opto-isolated inputs for use in VCO mode or Step and Direction mode. The function of the input/outputs is also
determined by the selected operating mode. The features of these operating modes are described below.
STEP MOTOR DRIVE FEATURES
The G216 can operate as a conventional STEP and DIRECTION input step motor drive.
MICROSTEPPING:
The G216 has a 10 microstep native resolution; each full step angle of the motor is divided into 10 equally
spaced microsteps so a 200 step per revolution motor has 2000 stopping locations per revolution.
STEP PULSE MULTIPLIER:
The G216 synthesizes 10 microstep pulses for every full-step pulse and 5 microstep pulses for half-step
pulse. The G216 acts like a full or half-step drive but motor has the smoothness of a 10-microstep drive.
SUB-MICROSTEPPING:
For the 10 microstep resolution, each input step pulse is divided into 32 sub-microsteps resulting in a
motor smoothness equal to a 320 microstep drive.
MORPHING:
The G216 morphs from sine-cosine motor currents at low speeds to square-wave currents at high speeds. This
technique extracts the maximum possible power from the motor at higher speeds. Morphing begins at 240RPM and ends at
360RPM.
MID-BAND RESONANCE COMPENSATION:
The G216 uses active second-order damping to completely suppress a step motor’s
tendency to resonate and stall at medium speeds (300RPM – 900RPM). This results in stable motor operation in this region.
LOW SPEED RESONANCE COMPENSATION:
Low speed resonances are motor vibrations at speeds below 120 RPM caused by
motor non-linearity. The PROFILE and ADJUST trimpots settings nulls these vibrations.
PROTECTION:
The G216 is protected against motor to ground and motor to motor output short-circuits. It is also protected
against reversed power supply polarity and power supply over-voltage. The internal fuse blows on polarity reversal and over-
voltage.
AUTOMATIC STANDBY CURRENT:
If enabled, the motor phase current is reduced to 70% of the set value and the G216 motor
switching topology is changed to a low heating recirculating mode. This happens 1 second after the last step pulse is received.
VCO FEATURES
'ON THE FLY' MOTION CONTROL:
Acceleration, velocity and destination can be changed even while the motor is in motion. The
new values apply immediately.
CW and CCW LIMIT INPUTS:
The G216 has an input for a limit switch on each end of travel. Once this switch is triggered the
motor will decelerate to a stop and accelerate up to the opposite direction’s set speed.