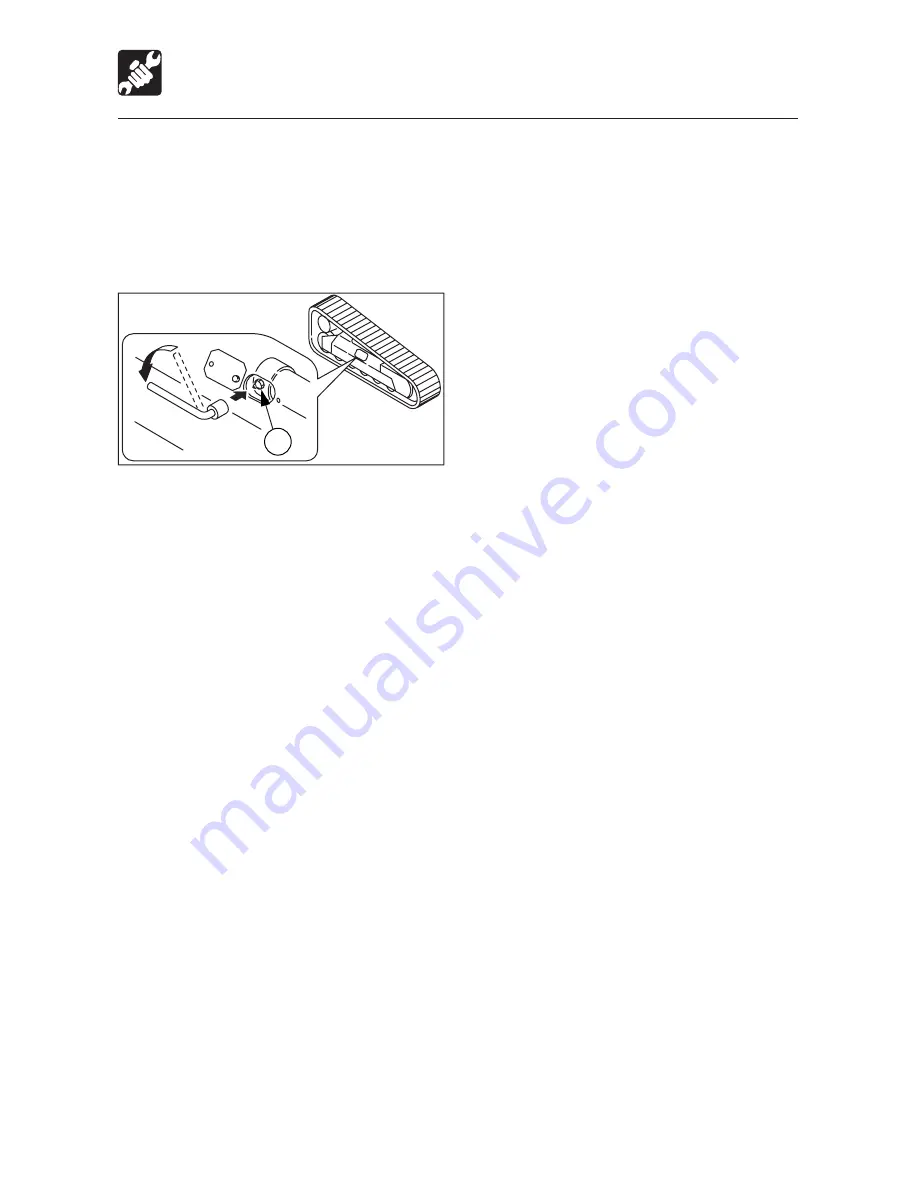
129
MAINTENANCE
Every 50 Hours
2. Use the grease gun to insert grease
through the grease nipple in the grease
discharge valve (1).
3. Check the track tension.
Decreasing the tension
1. Remove the cover.
2. Use the wrench to slowly loosen the
grease discharge valve (1) and drain the
grease.
If the grease does not drain easily, move
the machine forward or rearward.
3. Tighten the grease discharge valve (1).
• Tightening torque: 59 N·m (43.4 ft-lb.)
1
T7G016
Summary of Contents for CTL55
Page 1: ...CTL55 CTL65 CTL75 CTL85 Compact Track Loader OPERATOR S MANUAL Revision E 09 10...
Page 6: ...4...
Page 8: ...6...
Page 38: ...SAFETY 36 Safety Signs Decals...
Page 39: ...37 SAFETY Safety Signs Decals...
Page 40: ...SAFETY 38 Safety Signs Decals...
Page 66: ...64 MEMO...
Page 67: ...65 MEMO...
Page 68: ...66 MEMO...
Page 69: ...67 MEMO...
Page 70: ...68...
Page 114: ...MAINTENANCE 112 Maintenance Log Date Hours Service Procedure...
Page 115: ...113 MAINTENANCE Maintenance Log Date Hours Service Procedure...
Page 123: ...121 MEMO...
Page 129: ...127 MEMO...
Page 156: ...154...
Page 170: ...168...
Page 171: ...169 Main Speci cations 170 Machine Dimensions 174 Operating Range 176 SPECIFICATIONS...
Page 176: ...SPECIFICATIONS 174 Machine Dimensions...
Page 178: ...SPECIFICATIONS 176 Operating Range T7K0021 F H C A D B G E...
Page 180: ...178...
Page 181: ...179 General Precautions 180 Air Conditioner CTL55 182 OPTIONS...
Page 193: ...191 MEMO...
Page 194: ...192...
Page 195: ...193 INDEX...