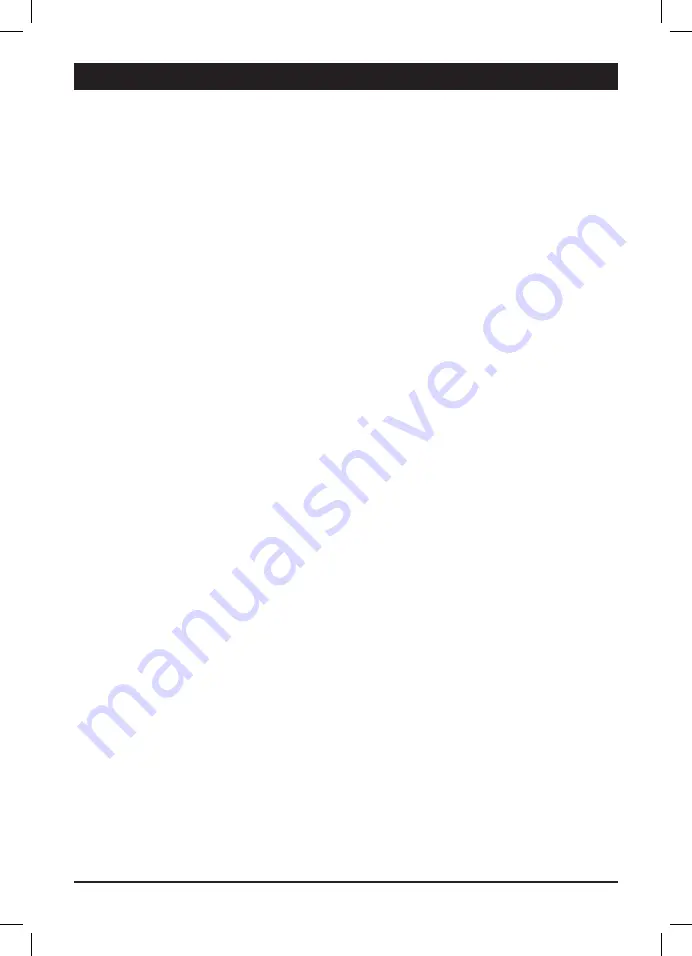
MS3002 Manual v.200909
Page 19
GLOSSARY OF TERMS
AMPERAGE (AMPS) –
A measure of
the flow of electric current. Higher ratings
generally means the tool is suited for
heavier use.
ARBOR LOCK –
Allows the user
to keep the blade from rotating while
tightening or loosening the arbor bolt
during blade replacement or removal.
BASE –
Supports the table, holds
accessories and allows for workbench or
leg set mounting.
BEVEL LOCK HANDLE –
Locks the
miter saw at a desired bevel angle.
BEVEL SCALE –
To measure the bevel
angle of the saw blade 0° to 47° left.
CARBIDE TIPPED –
Extremely hard
steel pieces with sharp cutting edges
fastened to cutting tools such as saw
blades.
COVER PLATE SCREW –
Loosen this
screw and rotate the plate for access to
the blade arbor bolt.
EXTENSION CORD –
An electric cord
used between power tools and outlets to
extend the range of the tools. The more
amperage your tool uses, the longer the
distance, the larger the size of the wire
needed in your extension cord.
EYE PROTECTION –
Goggles or
spectacles intended to protect your
eyes. Eye protection should meet the
requirements of ANSI Z.87.1 (USA) or
CSA Z94.3-M88 (Canada).
FACE SHIELD –
An impact resistant
shield that helps to protect your face from
chips, sparks, small debris. Should only
be used in conjunction with additional eye
protection.
FENCE –
Helps to keep the workpiece
from moving when sawing. Scaled to
assist with accurate cutting.
GUARD –
Protective devise that forms
a barrier between a hazardous object
such as a blade, wheel or cutter and the
operator.
HOLD-DOWN LATCH –
Locks the
miter saw in the lowered position for
compact storage and transportation.
INSTRUCTION OR OPERATOR’S
MANUAL –
Booklet accompanying
your power tool that describes the
hazards and safe operation procedures,
outlines basic tool operation, care and
maintenance.
MITER HANDLE –
Used to rotate the
table, and to rotate the saw to a right or
left cutting position.
MITER SCALE –
Measures the miter
angle of the saw blade. Positive stop
index points have been provided at 0°,
15°, 22.5°, 31.6° and 45° right and left.
MOUNTING HOLES –
To mount the
miter saw to a stable surface.
ON/OFF TRIGGER SWITCH –
To
start the tool, squeeze the trigger.
Release the trigger to turn off the miter saw.
POSITIVE STOP LOCKING LEVER
–
Locks the miter saw at a preset positive
stop for the desired miter angle.
SWITCH HANDLE –
The switch handle
contains the trigger switch and the laser
on/off switch. The blade is lowered into
the workpiece by pushing down on the
handle. The saw will return to its upright
position when the handle is released.