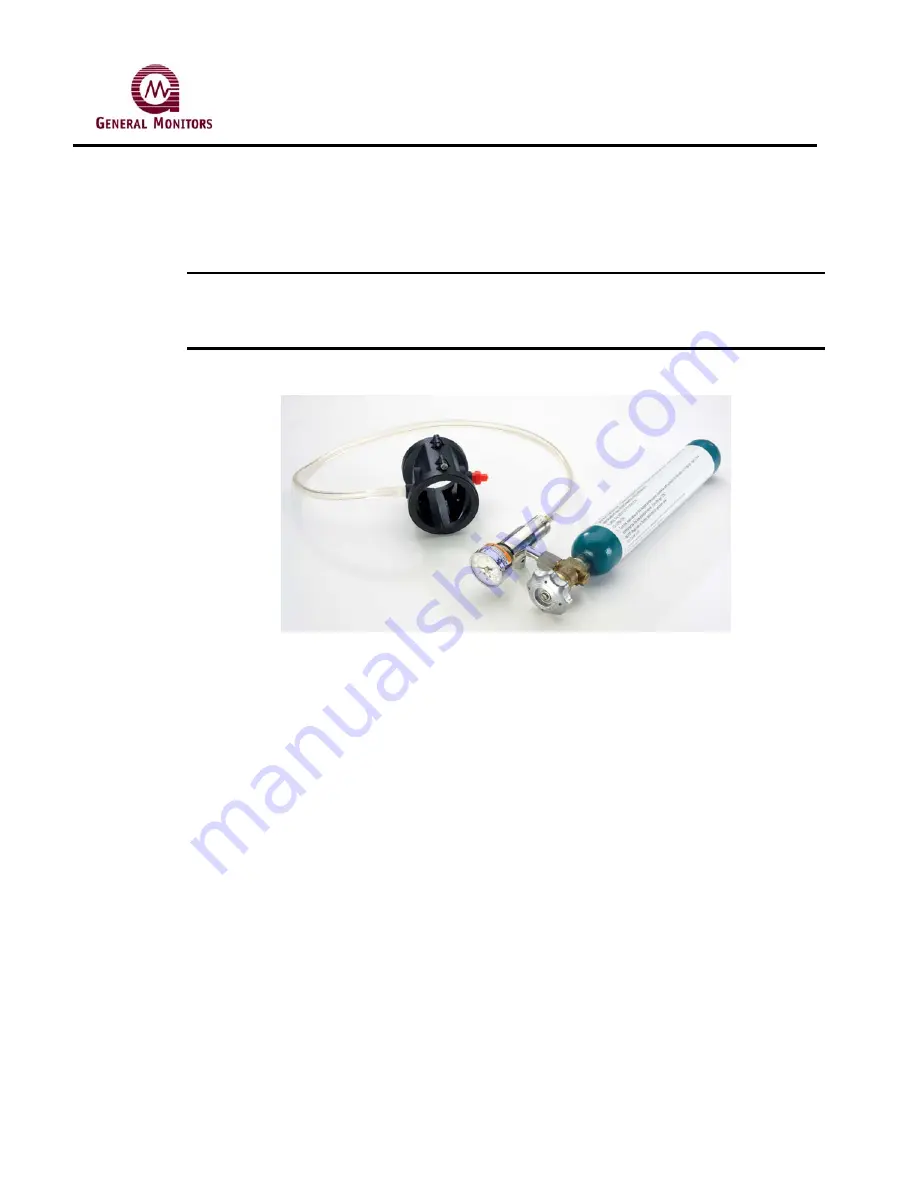
Model IR400
18
4.1.3 Gas Check Test Guidelines
Running a gas check test enables you to verify whether the detector is functioning correctly, by
applying a known gas concentration and monitoring the % LEL reading while keeping the alarm
and warning relays disabled. To apply gas or a gas simulation during the test, you can use the
General Monitors gas check kit with portable purge calibrator equipment.
•
NOTE:
You cannot run a gas check test from an FMD or IR4000S
attached to an
IR400. The FMD and IR4000S have a relay inhibit mode that will turn off the Warn
and Alarm relay but the current loop will still transmit the gas concentration level. This
could cause alarms on control room equipment.
4.1.3.1 Portable Purge Calibrator Equipment
The portable purge calibrator is a compact, accurate and safe system containing a non-
explosive gas concentration. The lecture bottle is filled with a standard 50% LEL mixture of
gas/air. Using a known gas/air mixture reduces the likelihood of error in field calibration.
The hose and cup adapter that are included allow for quick calibrations and gas checks.
Pre-mixed calibration gases at approximately 50% LEL are available in lecture bottles.
•
Butane
C4H10
•
Ethane
C2H6
•
Ethylene
C2H4
•
Methane
CH4
•
Hexane
C6H14
•
Pentane
C5H12
•
Propane
C3H8
Spare bottles containing these gases may be ordered. Methane lecture bottles may be returned
to General Monitors for refilling with the standard 2.5% by volume methane (50% LEL per ISO
10156 and NFPA 325).
4.1.4 Calibration Guidelines
Calibrating the detector corrects any errors that may be affecting the % LEL measurement that
is taking place. You should use the General Monitors gas check kit for calibration. Section
4.1.3.1 describes the gas check kit equipment in more detail. You may need to calibrate the
IR400 detector under several circumstances.
•
If the gas check test indicates that the detector needs adjustment.
•
If you are reconfiguring the IR400 to detect a different type of gas.
•
If you are moving the detector to a higher altitude location (every 1000 feet difference in
altitude requires recalibration).
Summary of Contents for IR400
Page 2: ......
Page 15: ...Model IR400 11 Figure 5b IR400 Mounting Dimensions with a European Box ...
Page 20: ...Model IR400 16 Figure 7 Wiring Diagram from IR400 to Control Equipment ...
Page 41: ...Model IR400 37 9 6 Engineering Documentation ...
Page 45: ...Model IR400 HART Field Device Specification for Point IR Gas Detector ...
Page 78: ...Model IR400 Infrared Point Detector for Hydrocarbon Gas Applications Modbus programming guide ...