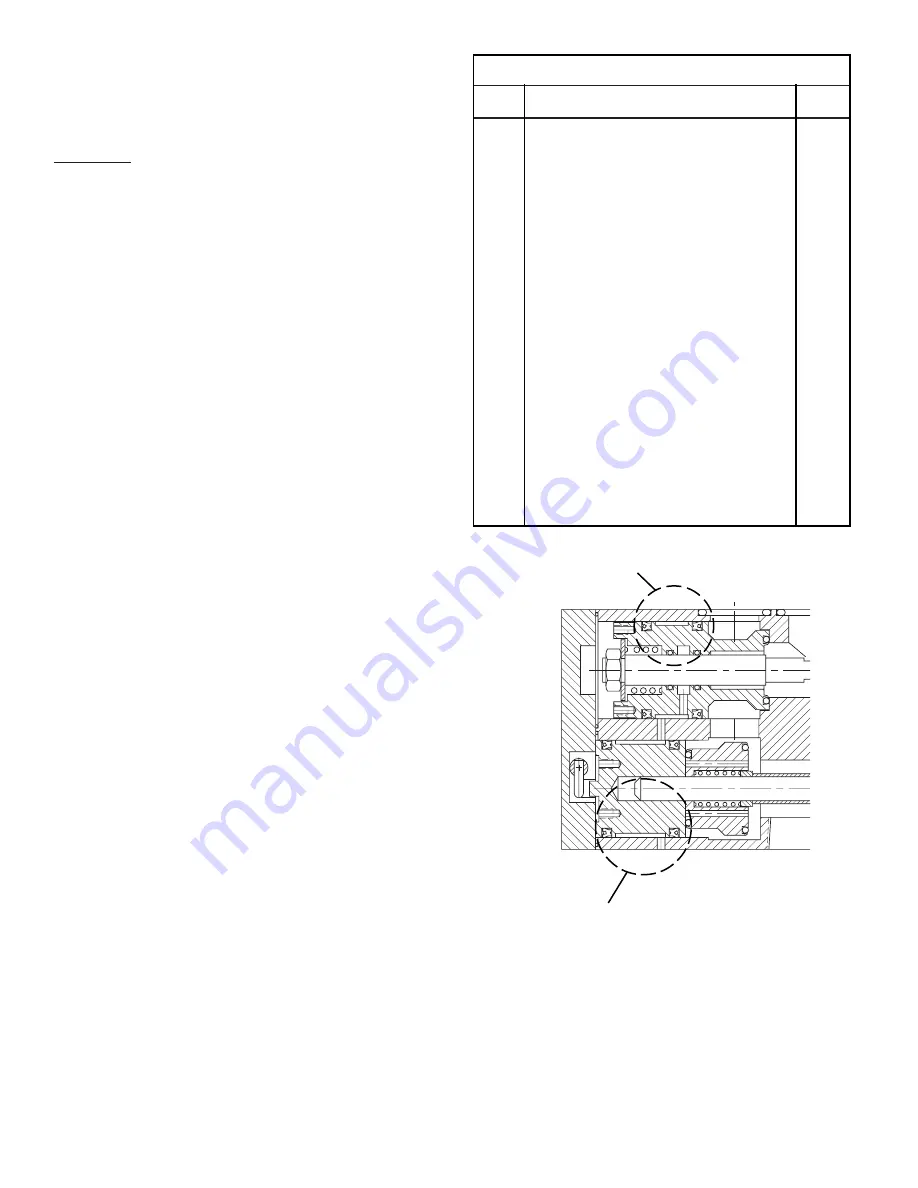
4 - 8
Maintenance and Repair
4.7
Inlet and Purge Exhaust
Switching Valve Maintenance
(Models OP15 through OP200)
WARNING!
Ensure that the Dryer is de-energized, valve isolated,
and fully depressurized before attempting to remove
or disassemble any Dryer component or subassembly.
Failure to do so may result in serious personal injury
and/or equipment damage.
1.
Clean and inspect all valve hardware upon disassem-
bly. Replace all software and any hardware which ap-
pears damaged or abnormally worn.
2.
Clean and inspect valve seat located inside the valve
body [1].
3.
Apply an ultra-thin film of O-ring lubricant to items [14],
[16], [17], and [21] before reassembly.
4.
The U-cup piston seal [16] has been fitted with a cut
O-ring. Ensure that the U-cup piston seal is installed
on the valve pistons [4] and [5] as shown in Figure 4.3.
5.
Apply a light coat of lubricant to the sockethead cap
screws, items (1) and (18). Hand tighten screws until
snug. Torque as follows:
Torque 1/4 - 20 screws to 40 in-lbs.
Torque 5/16 - 18 screws to 135 in-lbs.
Switching Valve Components
Item
Description
Total
1
Valve Body
1
2
Valve Cover (Left Side)
1
3
Valve Cover (Right Side)
1
4
Valve Piston (Inlet)
2
5
Valve Piston (Purge Exhaust)
2
6
Valve Poppet (Purge Exhaust)
2
7
Connect Rod
1
8
Centering Rod
1
9
Spacer
1
10
Backup Ring
2
11
Compression Spring (Inlet)
2
12
Compression Spring (Purge Exhaust)
2
13
Washer
2
14
O-Ring (Valve Cover)
4
15
Tetraseal
3
16
Piston Seal
8
17
O-Ring (Inlet)
4
18
Sockethead Cap Screw
12
19
Locknut
2
20
Shaft
2
21
O-Ring (Shaft)
2
22
Pin
2
Piston seal [16] orientation
on inlet valve piston [4].
Typical both sides.
Piston seal [16] orientation on
purge exhaust valve piston [5].
Typical both sides.
Figure 4.3