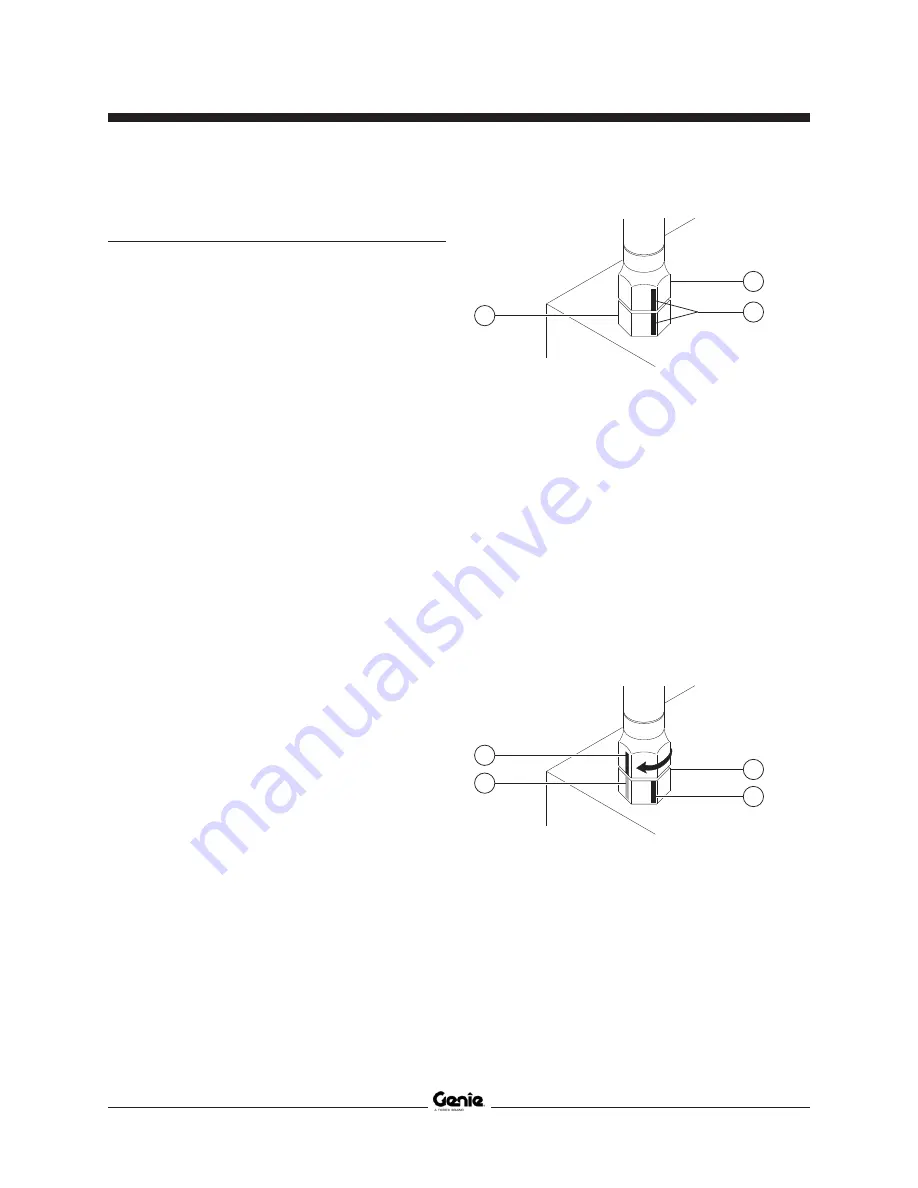
Section 2 • Specifications
November 2014
Part No. 229753
GS-2669 RT • GS-3369 RT • GS-4069 RT
2 - 11
SPECIFICATIONS
Torque Procedure
Seal-Lok™ fittings
1 Replace the O-ring. The O-ring must be replaced
anytime the seal has been broken. The O-ring
cannot be re-used if the fitting or hose end has
been tightened beyond finger tight.
Note: The O-rings used in the Parker Seal Lok™
fittings and hose ends are custom-size O-rings.
They are not standard SAE size O-rings. They are
available in the O-ring field service kit (Genie part
number 49612).
2 Lubricate the O-ring before installation.
3 Be sure that the face seal O-ring is seated and
retained properly.
4 Position the tube and nut squarely on the face
seal end of the fitting and tighten the nut finger
tight.
5 Tighten the nut or fitting to the appropriate
torque per given size as shown in the table.
6 Operate all machine functions and inspect the
hoses and fittings and related components to
confirm that there are no leaks.
JIC 37° fittings
1 Align the tube flare (hex nut) against the nose of
the fitting body (body hex fitting) and tighten the
hex nut to the body hex fitting to hand-tight,
approximately 30 in-lbs / 3.4 Nm.
2 Make a reference mark on one of the flats of the
hex nut, and continue it on to the body hex
fitting with a permanent ink marker. Refer to
Figure 1.
Figure 1
a
hex nut
b
reference mark
c
body hex fitting
3 Working clockwise on the body hex fitting, make
a second mark with a permanent ink marker to
indicate the proper tightening position. Refer to
Figure 2.
Note: Use the
JIC 37° Fittings
table on the previous
page to determine the correct number of flats for
the proper tightening position.
Note: The marks indicate that the correct tightening
positions have been determined. Use the second
mark on the body hex fitting to properly tighten the
joint after it has been loosened.
Figure 2
a
body hex fitting
b
reference mark
c
second mark
4 Tighten the hex nut until the mark on the hex nut
is aligned with the second mark on the body hex
fitting.
5 Operate all machine functions and inspect the
hoses and fittings and related components to
confirm that there are no leaks.
a
b
c
a
b
c
b
Summary of Contents for GS-2669 RT
Page 169: ...Section 6 Schematics November2014 6 9 Control Panel Circuit Diagram 6 10 ...
Page 235: ...Section 6 Schematics November2014 6 75 6 76 Electrical Schematic GS 4069 RT Gas LPG Models AS ...
Page 238: ...November2014 Section 6 Schematics 6 78 Electrical Schematic GS 4069 RT Gas LPG Models AS 6 77 ...
Page 243: ...Section 6 Schematics November2014 6 83 Electrical Schematic GS 4069 RT Diesel Models AS 6 82 ...
Page 246: ...November2014 Section 6 Schematics 6 86 Electrical Schematic GS 4069 RT Diesel Models AS 6 85 ...
Page 251: ...Section 6 Schematics November2014 6 91 Electrical Schematic GS 4069 RT Gas LPG Models CE 6 92 ...
Page 254: ...November2014 Section 6 Schematics 6 94 Electrical Schematic GS 4069 RT Gas LPG Models CE 6 93 ...
Page 259: ...Section 6 Schematics November2014 6 99 6 100 Electrical Schematic GS 4069 RT Diesel Models CE ...
Page 267: ...Section 6 Schematics November2014 6 107 Hydraulic Schematic GS 2669 RT and GS 3369 RT 6 108 ...
Page 270: ...November2014 Section 6 Schematics 6 110 Hydraulic Schematic GS 4069 RT 6 109 ...