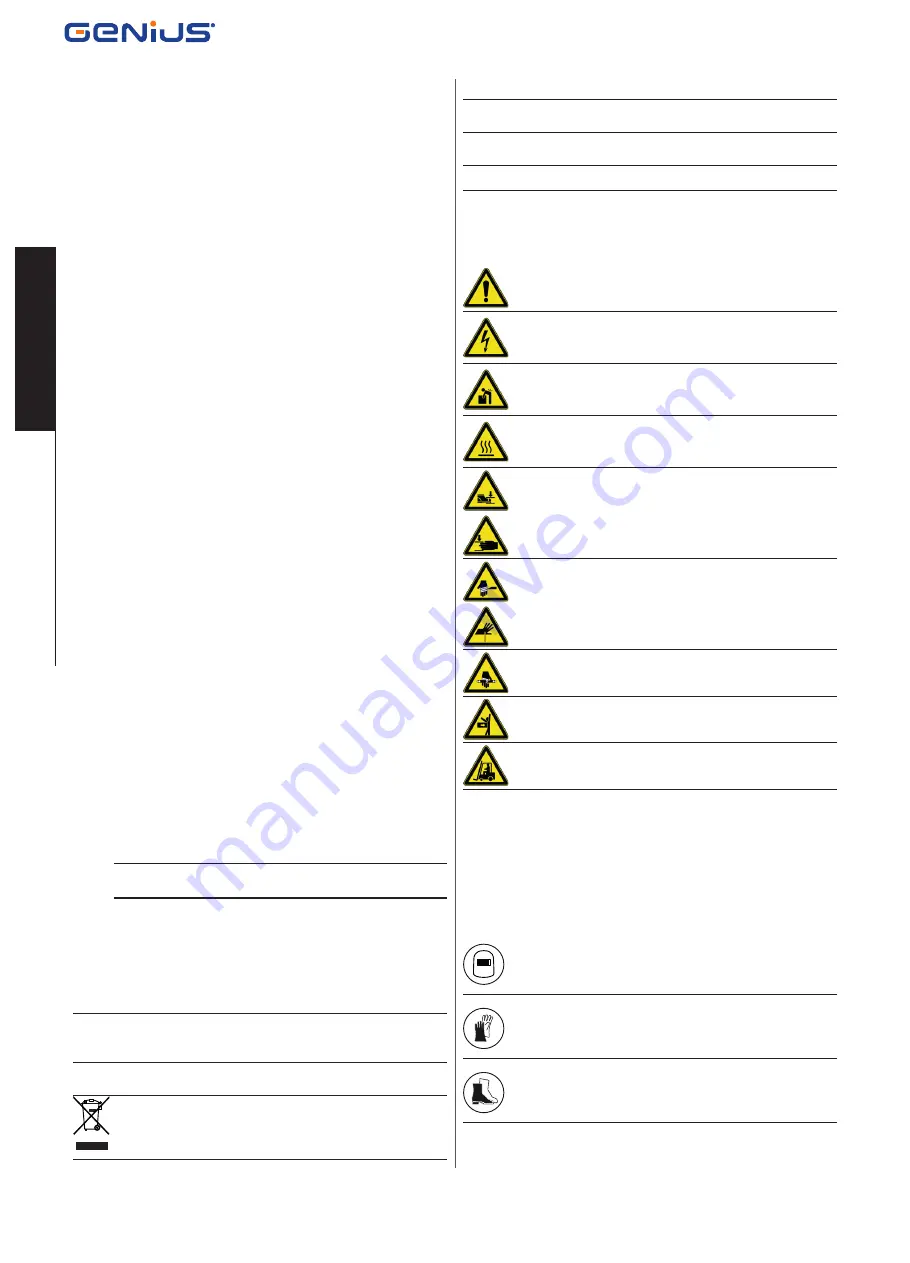
BLIZZARD 500-900
4
532102 - Rev.B
Tr
ansla
tion of the original instruc
tions
ENGLISH
1. INTRODUCTION TO THIS INSTRUCTION MANUAL
FIGURE E.g.:
1
-3 see Figure 1 - detail 3.
TABLE E.g.:
1
see Table 1.
§
CHAPTER/SECTION E.g.: §1.1 see section 1.1.
1.1 MEANING OF SYMBOLS USED
1
Symbols: notes and warnings on the instructions
F
WARNING ELECTRIC SHOCK HAZARD - The operation or stage described
must be performed following the supplied instructions and applicable safety
regulations.
!
WARNING, PERSONAL INJURY HAZARD OR RISK OF DAMAGE TO COMPO-
NENTS - The operation or stage described must be performed following the
supplied instructions and applicable safety regulations.
WARNING - Details and specifications which must be respected in order to
ensure that the system operates correctly.
RECYCLING AND DISPOSAL - The materials used in manufacturing, the batteries
and any electronic components must not be sent to landfill. They must be taken
to authorised recycling and disposal centres.
3
Symbols: personal protective equipment
Personal protective equipment must be worn to protect against hazards (e.g. crushing,
cutting, shearing etc.):
Obligatory use of mask/goggles to protect the eyes from the risk of shards
produced when using drills or welding equipment.
Obligatory use of work gloves.
Obligatory use of safety footwear.
This manual provides the correct procedures and requirements for
installing BLIZZARD 500-900 and maintaining it in a safe condition.
When drafting the manual, the results of the risk assessment con-
ducted by FAAC S.p.A. on the entire product life cycle have been taken
into account in order to implement effective risk reduction measures.
The following stages of the life cycle of the product have been con-
sidered:
-
Delivery/handling
-
Assembly and installation
-
Set-up and commissioning
-
Operation
-
Maintenance/troubleshooting
-
Disposal at the end of the product’s life cycle
Risks arising from installation and using the product have been taken
into consideration; these include:
-
Risks for the installation/maintenance technician (technical
personnel)
-
Risks for the user of the automation system
-
Risks to product integrity (damage)
In Europe, the automation of a gate falls under the Machinery Directive
2006/42/EC and the corresponding harmonised standards. Anyone
automating a gate (new or existing) is classified as the Manufacturer
of the Machine. They are therefore required by law, among other
things, to carry out a risk analysis of the machine (automatic gate in
its entirety) and take protective measures to fulfil the essential safety
requirements specified in Annex I of the Machinery Directive.
FAAC S.p.A. recommends that you always comply with the EN 12453
standard and in particular that you adopt the safety criteria and de-
vices indicated, without exception, including the dead-man function.
This manual also contains general information and guidelines, which
are purely illustrative and not exhaustive, in order to facilitate the ac-
tivities carried out by the Manufacturer of the Machine in all respects
with regard to carrying out the risk analysis and drafting the instruc-
tions for use and maintenance of the machine. It should be clearly
understood that FAAC S.p.A. accepts no liability for the reliability and/
or completeness of the above instructions. As such, the manufacturer
of the machine must carry out all the activities required by the Machi-
nery Directive and the corresponding harmonised standards on the
basis of the actual condition of the locations and structures where
the product BLIZZARD 500-900 will be installed, prior to commissio-
ning the machine. These activities include the analysis of all the risks
associated with the machine and subsequent implementation of all
safety measures intended to fulfil the essential safety requirements.
This manual contains references to European standards. The au-
tomation of a gate must fully comply with any laws, standards and
regulations applicable in the country where installation will take place.
Unless otherwise specified, the measurements provided in the instruc-
tions are in mm.
2
Symbols: safety indications (ISO 7010)
GENERAL HAZARD
Personal injury hazard or risk of damage to components.
ELECTRIC SHOCK HAZARD
Risk of electric shock from live parts.
CRUSHING HAZARD, DANGER TO THE MUSCULOSKELETAL SYSTEM
Risk of musculoskeletal crushing - Personal injury hazard when manually
lifting heavy loads.
BURN HAZARD
Risk of burns due to the presence of high-temperature parts.
CRUSHING HAZARD
Risk of crushing to the hands/feet due to the presence of heavy parts.
CUTTING/AMPUTATION/PUNCTURE HAZARD
Cutting hazard due to the presence of sharp components or the use of
pointed/sharp tools (drill).
SHEARING HAZARD
Risk of shearing from moving parts.
IMPACT/CRUSHING HAZARD
Risk of impact or crushing due to moving parts.
FORKLIFT TRUCK IMPACT HAZARD
Risk of collision/impact with forklift trucks.