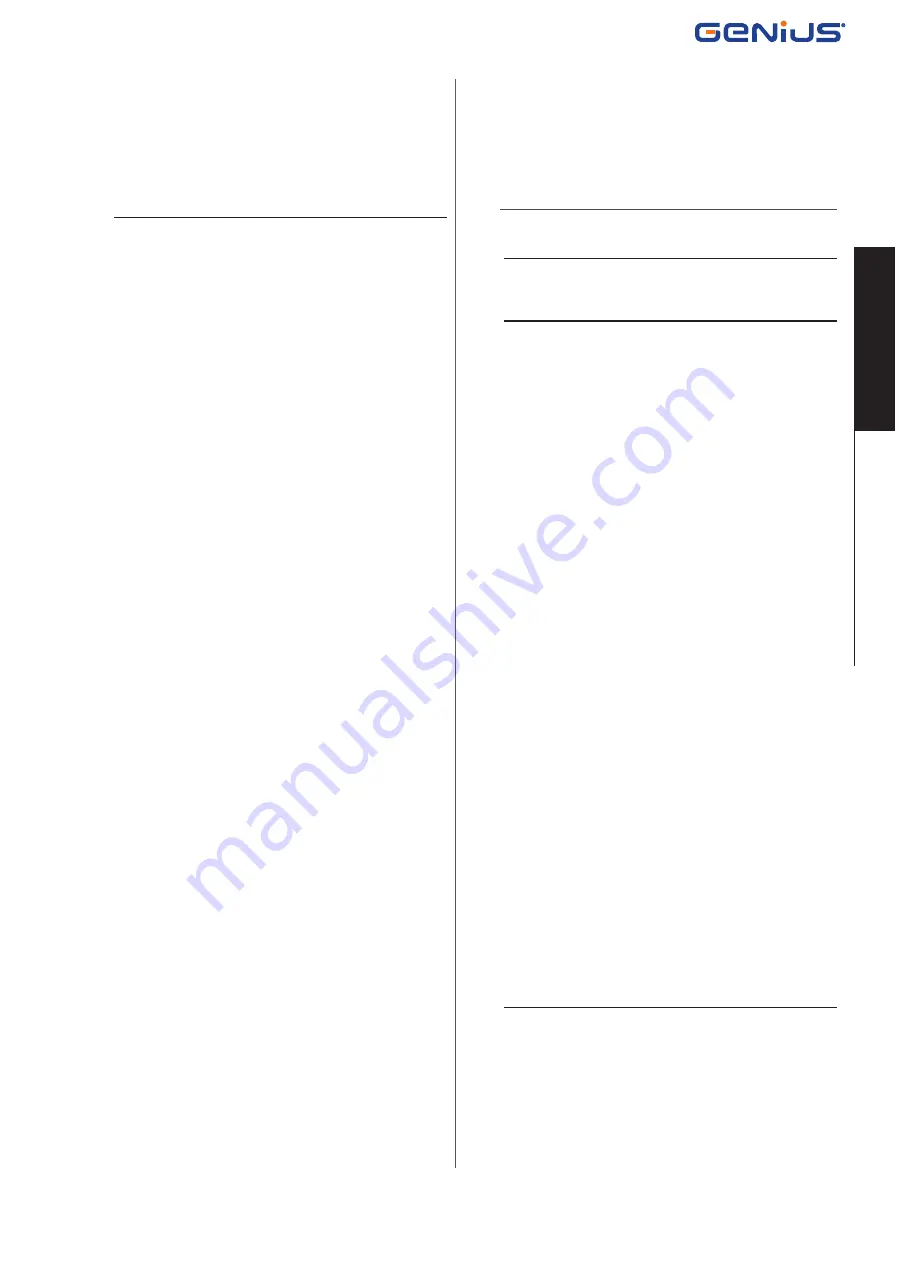
BLIZZARD 500-900
9
532102 - Rev.B
Tr
ansla
tion of the original instruc
tions
ENGLISH
4. INSTALLATION REQUIREMENTS
4.2 ELECTRICAL SYSTEM
4.1 MECHANICAL REQUIREMENTS
The mechanical structural components must comply with the require-
ments of EN 12604. Before installing the automation, the suitability
of the mechanical requirements must be established and any work
that is necessary in order to meet them carried out.
The essential mechanical requirements are as follows:
!
Solid ground to support the weight of the gate, the structures present
and the gearmotor.
Flat, horizontal paving in the area of movement
of the leaf. There must be no chance of water accumulating in the
installation area.
The structure (columns, guides, mechanical stops, leaf and
counterweights) must be solid and there must be no risk of detachment
or collapse (considering the weight of the leaf and the forces applied
by the gearmotor and wind action). Perform structural calculations
where necessary.
The structure must show no signs of corrosion or cracking.
The leaf must remain vertical throughout the entire length of travel,
with a regular, smooth and uniform movement. The path along which
the leaf slides must be perfectly horizontal (the leaf must not have a
tendency to open or close spontaneously when it is released).
Appropriate devices must be installed to prevent the leaf from falling.
There should be a solid surface on the leaf sufficiently large to attach
the rack to.
The sliding guides must be in good condition; they must be straight
and not deformed, they must be fastened securely and there must be
no obstacles along their entire length. The diameter of the guide
wheels must be appropriate for the weight and length of the leaf and
their profile section must coincide with that of the sliding guide. The
number and position of the wheels must ensure an adequate and
constant distribution of the weight.
A solid guide system for the suspended leaf in the case of a cantilever
gate.
Presence of upper containing guide to prevent vertical oscillation of
the leaf. The leaf must not under any circumstances come out from
its guides and fall. Wheels, rollers and bearings in good condition,
lubricated and free from play or friction.
Presence of external mechanical limit stops to limit the travel of the
leaf when opening and closing. The stops must be suitably sized and
solidly fastened so that they resist any impact of the leaf in the event of
improper use (leaf pushed and left to slide freely). The mechanical
limit stops must be positioned at 50 mm beyond the stop position of
the leaf, and must ensure that the leaf remains inside its sliding guides.
The thresholds and protrusions of the paving must be appropriately
shaped in order to prevent the risk of sliding or slipping.
For the creation of detection loops, refer to the specific instructions.
Presence of a safety area between the wall (or other fixed element)
and the furthest protruding part of the open leaf, to protect against
the risk of persons becoming trapped/crushed. Alternatively, check
that the opening force required falls within the maximum permissible
limits according to applicable standards and legislation.
Presence of safety areas between the fixed and moving parts, to protect
against the risk of hands being trapped.
Alternatively, apply protec-
tive elements that prevent fingers from being introduced.
Presence of a safety area between the paving and lower edge of the
leaf, along its entire path, providing protection from the risk of feet
becoming caught in and crushed beneath the wheels.
Alternatively,
apply protective elements preventing the introduction of feet.
No sharp edges or protruding parts should be present to ensure there are
no cutting, hooking or perforation hazards.
Alternatively, eliminate
or protect any sharp edges and protruding parts.
No slots or openings should be present on the sliding leaf or the fencing
to prevent the creation of a shearing hazard. Alternatively, apply
protective mesh to any such openings. The mesh should be sufficien-
tly fine to prevent introduction of body parts requiring protection, in
relation to the distance between the fixed and moving parts.
For the minimum dimensions to prevent crushing/shearing of body
parts, refer to EN 349. For the safety distances required to prevent
danger zones being reached, refer to ISO 13857.
If the area of installation gives rise to the risk of impact by vehicles,
provide an appropriate protective structure to protect the gearmotor.
F
Always shut off the power supply before performing any work. If
the disconnect switch is not in view, apply a warning sign stating
“WARNING - Maintenance in Progress”.
!
The electrical system must comply with applicable legislation in the
country of installation.
Use components and materials with CE marking which are compliant
with the Low Voltage Directive 2014/35/EU and EMC Directive
2014/30/EU.
The power supply line for the automation must be fitted with a multi-
pole circuit breaker, with a suitable tripping threshold, a contact ope-
ning distance of at least 3 mm and a breaking capacity that complies
with current regulations.
The power supply for the automation must be fitted with a 30 mA
differential switch.
The metal parts of the structure must be earthed.
Check that the protective earthing system complies with applicable
regulations in the country of installation.
The electrical cables of the automation system must be of a size and
insulation class that is compliant with current legislation and laid in
appropriate rigid or flexible conduits, either above or below ground.
Use separate conduits for the power supply and the 12-24 V control
devices / accessories cables.
Check buried cable plans to ensure that there are no other electrical
cables in proximity to the planned digging/drilling locations to prevent
the risk of electrocution.
Check that there are no pipes in the vicinity as well.
The conduit fittings and the cable glands must prevent the entry of
moisture, insects and small animals.
Protect extension connections using junction boxes with an IP 67
protection rating or higher.
It is recommended to install a flashing light in a visible position to
indicate when it is moving.
The control accessories must be positioned in areas that are always ac-
cessible and not dangerous for the user. It is recommended to position
the control accessories within the field of view of the automation. This
is mandatory in the case of hold-to-run controls.
If an emergency stop button has been installed, it must be EN13850
compliant.
Comply with the following heights from the ground:
- control accessories = minimum 150 cm
- emergency buttons = maximum 120 cm
If the manual controls are intended to be used by disabled or infirm
persons, highlight them with suitable pictograms and make sure that
these users are able to access them.