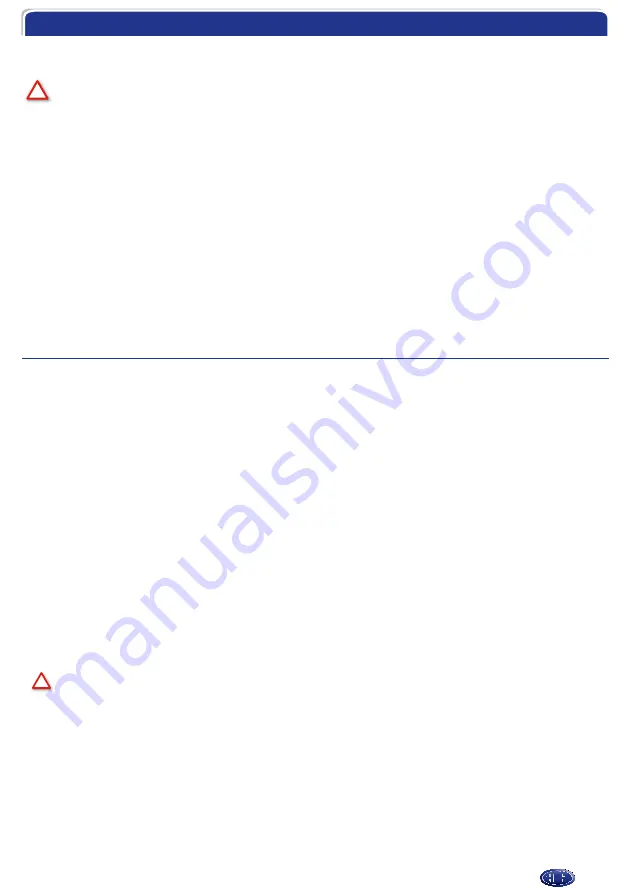
User Manual - P series
5
www.georgin.com
!
For temperature switches, the minimum dead bands given in our manuals are recorded under ideal
test conditions. The sensing element experiences the temperature variations of the installation without
delay and in its bulk. In operation, these dead bands can be different in view of the exchange conditions:
rate of temperature change, specific heat, radiation, inertia of the measuring instrument compared to
inertia of temperature switch, presence of a sleeve or immersion sleeve, etc.
5.2. Pneumatic functions
The instruments can be equipped with a Normally Open (NO) or Normally Closed (NC) pneumatic function using a
poppet or spool valve.
The supply fittings are M5, 1/4, or 1/8 gas threaded according to the type of function or the model.
According to the type of cell, the control pressure will be:
-
As standard: 1.5 to 8 bar (poppet design <> with a residual leak).
-
On request: 0 to 10 bar (spool design <> without leak).
The control fluid must be compatible with the ISO-VG 10 standard (air, nitrogen, etc.).
Maximum allowable filtration 5 µm.
The standard materials for the cell body are polyamide, brass, and/or aluminium. The seals are made of NBR
(other types on request).
II.
Before installation
1.
Storage
The pressure switch or temperature switch must be stored in a sheltered location, in its original packaging.
The storage temperature must be between:
-40 and +70°C for bellows instruments
-20 and +70°C for diaphragm pressure switches
-40 and +55°C for temperature switches from the C, G and M ranges
They must not be stacked to reach a load greater than 10 kg.
2.
Before installation
Allow the instrument to return to ambient operating temperature before installing it.
Whilst removing the packaging, check the equipment and all accessories.
The housing must be examined to check the following points:
Check that the paint has not been damaged.
Check that there are no signs of deformation or impact on the housing.
For instruments equipped with an immobilising bolt for transport (located in the instrument's process fitting),
remove this item.
!
For ML/DML instruments:
1. Loosen the locknut and the immobilizing bolt inserted in the fitting.
2. Connect the instrument to a pressure bench on the HP side, and apply a pressure of 150 mbar. Return to
atmospheric pressure, and disconnect the instrument from the bench.
3. Rest the instrument for 24 hours before calibrating.
Before installation check again that the materials in contact are compatible with the process to be monitored.
If necessary, protect the instrument with a safety device that is appropriate to the application (pressure limiter,
shock absorber, thermowell).