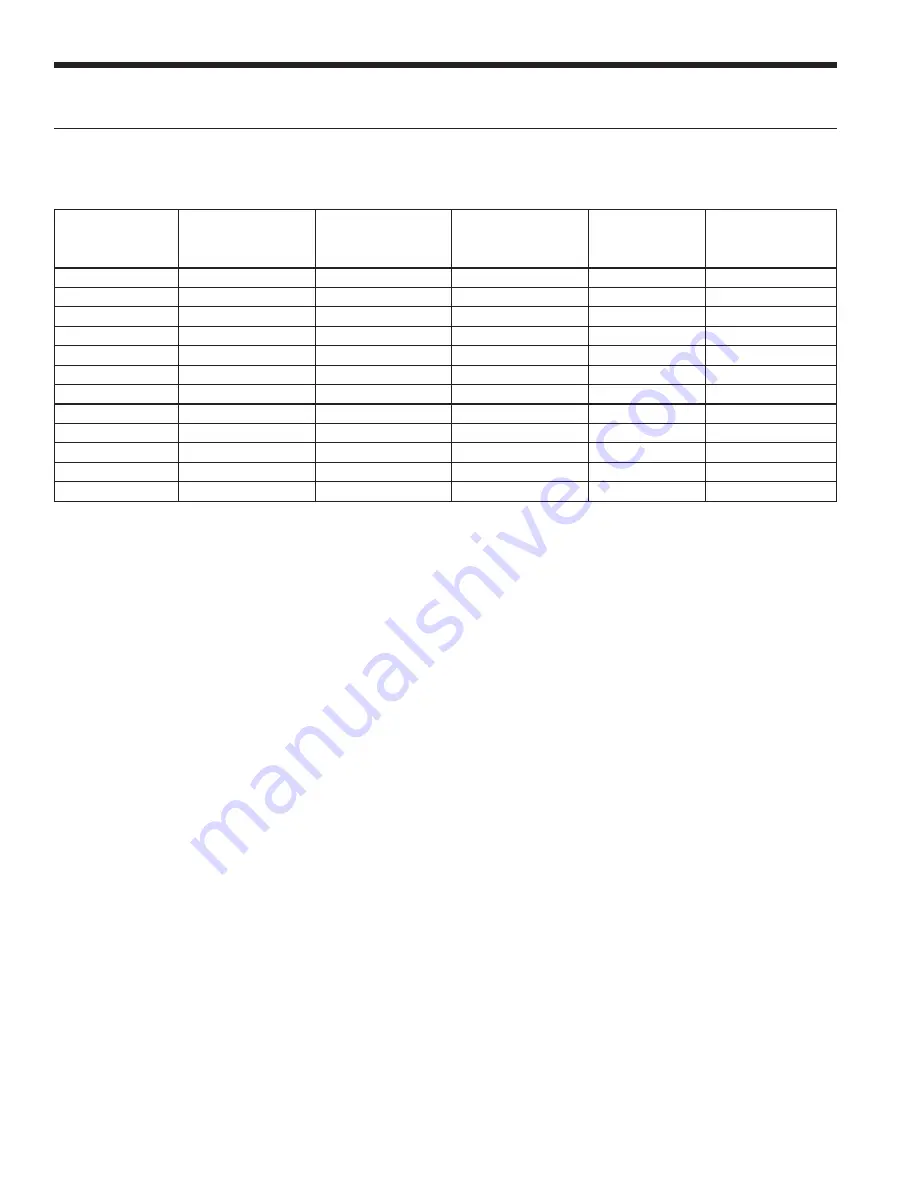
6
General Installation Information cont.
Moving and Storage
If the equipment is not needed for immediate installation it should
be left in its shipping carton and stored in a clean, dry area. Units
must only be stored or moved in the normal “up” orientation.
Unit Location
Locate the unit in an indoor area that allows for easy removal of
the filter and access panels (the air handler units are not approved
for outdoor installation). Location should have enough space
for service personnel to perform maintenance or repair. Provide
sufficient room to make refrigerant, electrical and duct connections.
If the unit is located in a confined space, such as a closet,
provisions must be made for return air to freely enter the space
by means of a louvered door, etc. The air handler section may be
installed on any level surface strong enough to support its weight.
When installed in a closet or on a stand, it should be mounted
on vibration absorbing material slightly larger than the base to
minimize vibration transmission to the building structure.
When installed in an attic or above a drop ceiling, the installation
must conform to all local codes. If the unit is suspended and
installed in the horizontal position, the entire length of the unit
should be supported. If the application requires the air handler to
be installed on the attic floor then the unit should be set in a full
size secondary drain pan. In this case the secondary drain pan
should be set on top of a vibration absorbing mesh. The secondary
drain pan is usually placed on a plywood base. A secondary drain
pan should be used when equipment is installed over a finished
living area to provide protection from water damage in case of
plugging of the air handler primary drain line. The secondary drain
line should terminate somewhere that is easily visible by the
homeowner. Be certain to show the homeowner the termination
location of the secondary drain line and to explain its purpose.
Duct System
The duct system should be sized to handle the design airflow
quietly and efficiently. To maximize sound attenuation of the unit
blower, the supply and return plenums should include an internal
duct liner of fiberglass or constructed of ductboard for the first
few feet. On systems employing a metal duct system, canvas
connectors should be used between the unit and the ductwork. If
air noise or excessive airflow is a problem, the blower speed can
be changed. Application of the unit to un-insulated metal ductwork
in an unconditioned space will cause poor unit performance and
allow condensation to form on the duct and possibly cause damage
to the structure.
If the unit is connected to existing ductwork, check the duct
system to ensure that it has the capacity to accommodate the air
required for the unit application. If the duct is too small, as in the
replacement of heating only systems, larger ductwork should be
installed. All existing ductwork should be checked for leaks and
repaired as necessary.
Condensate Drain
To facilitate condensate removal, the air handler should be pitched
1/4” towards the drain in both directions. The drain line contains
cold water and should be insulated in unconditioned spaces to
avoid drain line condensation from dripping on ceiling, etc. The
drain pan has a primary and auxiliary drain connection. The
21S521A03 condensate hose assembly kit is provided to connect
the drain pan's primary stainless steel tube to the PVC coupling
The air handler drain connections must be connected to a drain line
and pitched away from the unit a minimum of 1/8” per foot to allow
the condensate to flow away from the air handler.
A trap must be
installed in the drain line
below the bottom of the drain pan to
ensure free condensate flow (units are not internally trapped).
ASTON SERIES AIR HANDLER INSTALLATION MANUAL
Air Handler Sizing Selection
The Aston Series Air Handlers are designed for R410a refrigerant and should be matched with Aston indoor and outdoor series
compressor section according to the table below.
Air Handler
Indoor Split Model
(Single)
Indoor Split Model
(Dual Capacity)
Outdoor Split Model
(Dual Capacity)
Airfl ow(CFM)
Electric Heat (kW)
GAH022B***1R
103*022
-
800
5
GAH026B***1R
-
103*026
104*026
925
5
GAH030B***1R
103*030
-
-
980
5, 10
GAH036B***1R
103*036
-
-
1225
5, 10
GAH036B***1R
-
103*038
104*038
1225
5, 10
GAH042B***1R
103*042
-
-
1425
10, 15
GAH048B***1R
103*048
-
-
1625
10, 15
GAH048B***1R
-
103*049
104*049
1625
10, 15
GAH060B***1R
103*060
-
-
1760
10, 15, 20
GAH060B***1R
-
103*064
104*064
1760
10, 15, 20
GAH060B***1R
103*070
-
-
1760
10, 15, 20
GAH060B***1R
-
103*072
104*072
1760
10, 15, 20
6/9/08