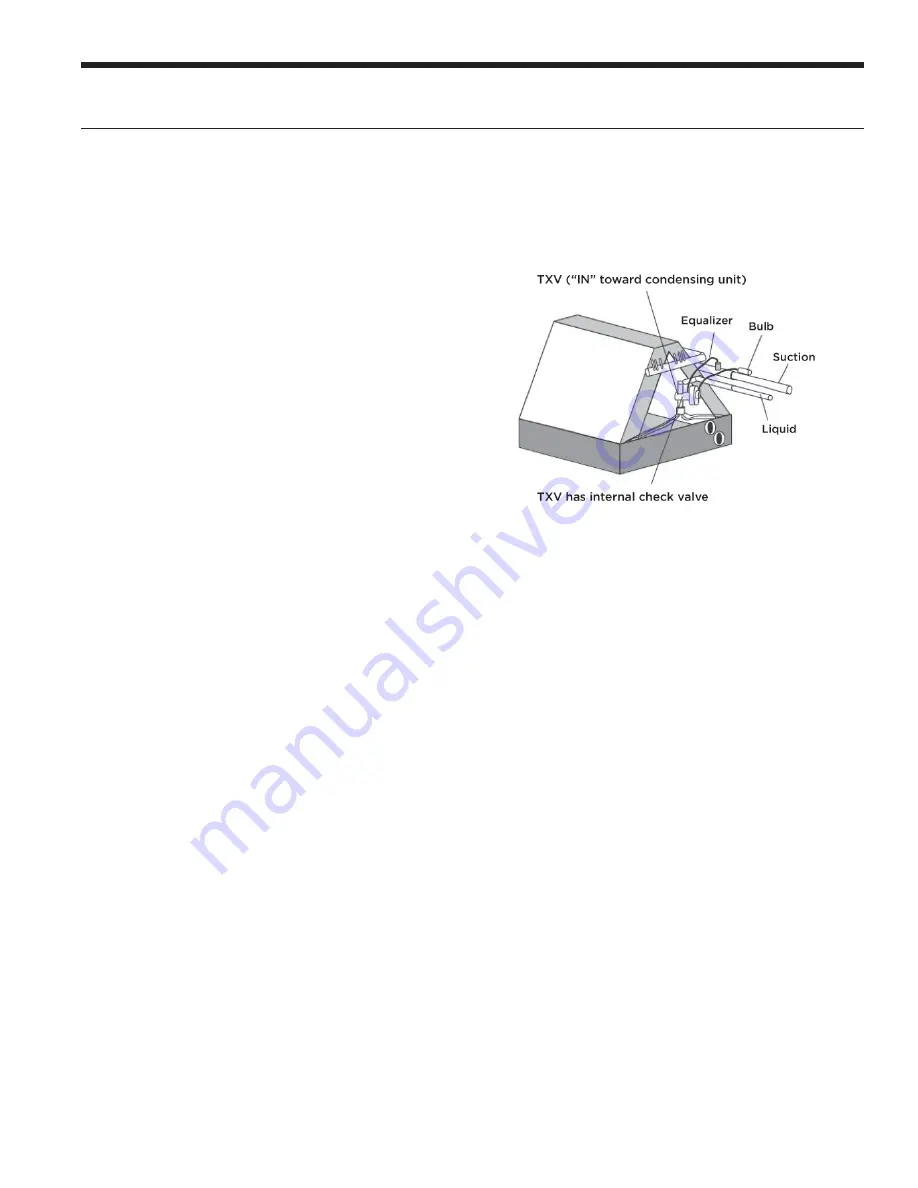
9
General Installation Information cont.
Air Handler Installation
The air handler is attached to the shipping pallet with screws. Prior
to setting the unit in place remove the shipping screws located in
the front base right behind the air filter access panel. Also remove
the external shipping brackets at the rear of the cabinet.
An air filter must always be installed upstream of the air coil on the
return air side of the air handler. An air filter is provided with the
air handler. If there is limited access to the filter rack for normal
maintenance, it is suggested that a return air filter grille be installed.
In this instance the filter supplied with the air handler should be
removed. Be sure that the return duct is properly installed and free
of leaks to prevent dirt and debris from bypassing the filter and
plugging the air coil.
The cabinet should be sealed so that unconditioned warm air can
not enter the cabinet. Warm air will introduce moisture into the
cabinet which could result in water blow-off problems, especially
when installed in an unconditioned space. Make sure that the
liquid line, suction line and drain line entry points into the cabinet
are well sealed. Use the butyl tape supplied with the air handler to
seal around the copper lines entering the cabinet.
All wall penetrations should be sealed properly. The line set should
not come into direct contact with water pipes, floor joists, wall
studs, duct work, floors, walls and brick. The line set should not
be suspended from joists or studs with a rigid wire or strap which
comes into direct contact with the tubing. Wide hanger straps which
conform to the shape of the tubing are recommended. All line sets
should be insulated with a minimum of 3/8” closed cell insulation.
The line set insulation should be pliable, and should completely
surround the refrigerant line. As in all R-410a equipment, a
reversible liquid line filter drier is required to insure all moisture
is removed from the system. This drier is factory installed in the
series compressor section. This drier should be replaced whenever
“breaking into” the system for service. All exterior insulation should
be painted with UV resistant paint or covering to insure long
insulation life.
Connection to the Coil
Connect the refrigerant line set to the ‘A’ coil tubes. Nitrogen
should be bled through the system at 2 to 3 PSI to prevent
oxidation inside the refrigerant tubing. Use a low silver phos-
copper braze alloy on all brazed connections. The air handler
TXV bulb is secured to the ‘A’ coil for shipping. The indoor and
outdoor compressor section is shipped with a factory charge and
the service valves are not to be opened until the line set and air
handler have been leak tested, purged and evacuated. A damp
towel or heat sink should be used on the service valves to prevent
damage caused by excessive heat.
Refer to the Refrigerant Line Sizing table to determine the proper
line set configuration for the system being installed. Line sets over
60 feet in length are not recommended. If the line set is kinked or
deformed and cannot be reformed, the bad section of pipe should
be replaced. A restricted line set will affect unit performance.
Line sets should be routed as directly as possible, avoiding any
unnecessary bends and turns.
Important Note:
The bulb will need to be attached to the suction line on the outside of
the cabinet once the refrigerant line connections have been made.
Leak Testing
The refrigeration line set must be pressurized and checked for
leaks before purging and charging the unit. To pressurize the line
set, attach refrigerant gauges to the service ports and add an inert
gas (nitrogen or dry carbon dioxide) until pressure reaches 60 to 90
PSIG. Never use oxygen or acetylene to pressure test the system.
Use an electronic leak detector or a good quality bubble solution to
detect leaks on all connections made in the field. Be sure to check
the service valve ports and stems for leaks. If a leak is found,
repair it and repeat the above steps. For safety reasons do not
pressurize the system above 150 PSIG. Purge pressure from the
line set slowly when the pressure test is complete. The system is
now ready for evacuation.
System Evacuation
Ensure that the line set and air coil are evacuated before opening
service valves. The line set and air coil must be evacuated to
250 microns with a good quality vacuum pump and use a vacuum
gauge to ensure that air and moisture are removed. With the
system shut off from the vacuum pump a sufficient system vacuum
is achieved when a 500 micron vacuum can be held for 30 minutes.
A fast rise to atmospheric pressure indicates a leak, while a slower
rise to around 1500 microns indicates moisture is still present in the
system and further evacuation is required.
Refrigeration
The GAH series air handlers are supplied with an expansion
device. Once the line set has been brazed into the air handler
the txv bulb must be attached to the suction line outside of the
cabinet and insulated with foam tape. Be careful not to crush the
txv bulb by over-tightening the clamp. The txv supplied has an
internal check valve so no external check valve is necessary. The
ASTON SERIES AIR HANDLER INSTALLATION MANUAL