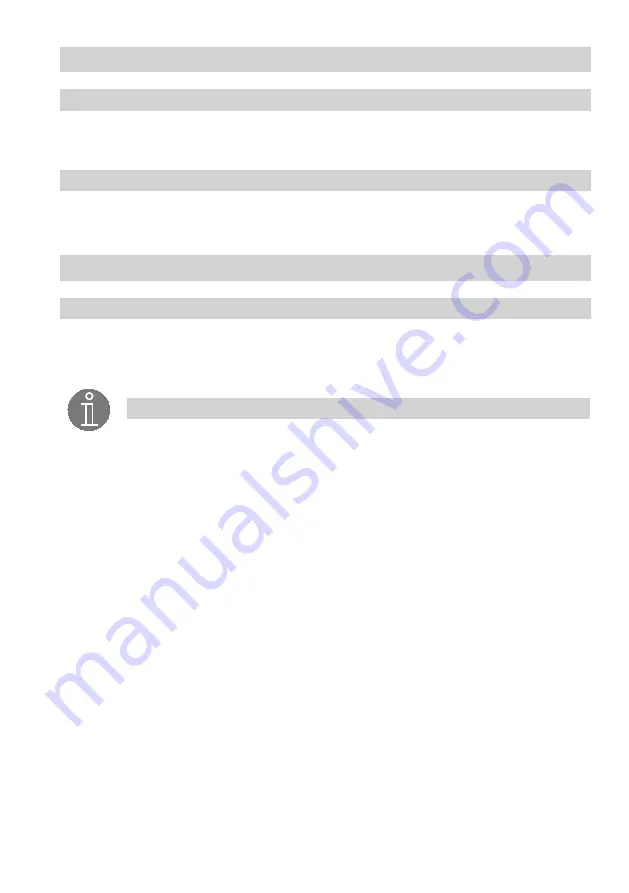
25
Apply power to switching controller NRS 1-41, NRS 1-40.1, NRS 1-40.2.
Commissioning Procedure
Make sure that the level electrode NRG 1...-41, NRG 1...-41.1 is properly connected to the switching
controller NRS 1-41, NRS 1-40.1, NRS 1-40.2 according to the wiring diagram.
Fig. 13, 14
Check wiring
Apply mains voltage
Operation
Used in combination with switching controller NRS 1-41, NRS 1-40.1, NRS 1-40.2 in (pressurized)
hot-water plants and steam boilers working in accordance with TRD 401, TRD 602, TRD 604 or other
national regulations.
High-water level limiter (Max alarm)
Note
n
Should malfunctions occur during the commissioning procedure refer to section
“Troubleshooting” on page 26 in order to find, analyse and eliminate the fault.
Summary of Contents for NRG 16-41
Page 27: ...27 For your Notes ...