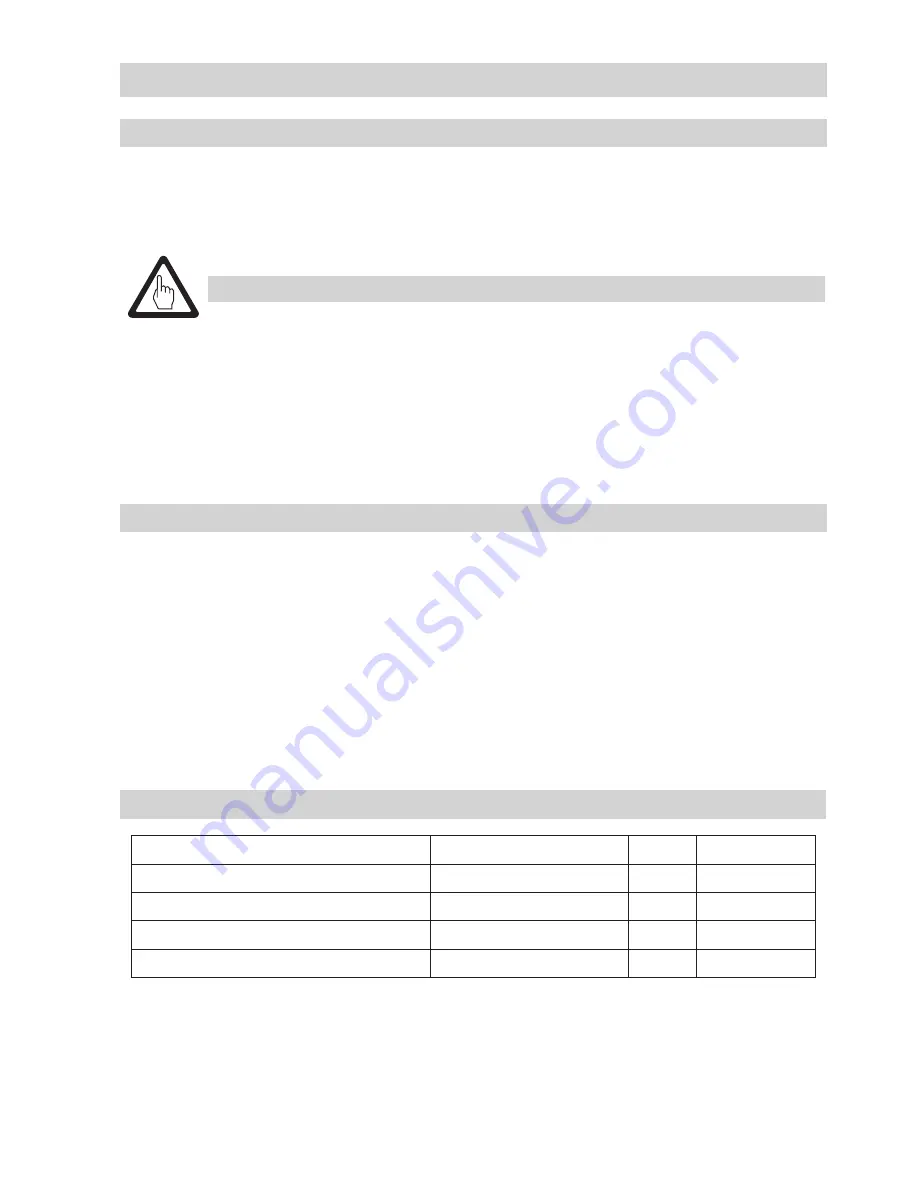
17
Troubleshooting
- continued -
Attention
n
Refer to the installation and operating manuals of the temperature transmitter
TRV 5-40 and the temperature switches TRS 5-50 and TRS 5-52 for commissioning,
for more information on indicated fault code E.xxx and for further diagnosis and
troubleshooting.
n
Please replace the measuring element if the temperature measured by the
temperature sensor deviates from the plant temperature.
n
The measuring element must also be replaced by a new one if a malfunction occurred
and the rated service pressure and temperature limits were exceeded.
Replacing the temperature measuring element
The temperature measuring element
e
can be replaced during operation if necessary.
1. Disconnect supply voltage (TRV 5-40, TRS 5-50, TRS 5-52).
2. Take cover
d
off the terminal box .
3. Disconnect the measuring element
e
.
4. Slacken fixing screws for measuring element. Pull out measuring element.
5. Insert new measuring element and fasten fixing screws.
6. Re-attach the measuring element
e
.
7. Replace cover
d
and tighten screw securely.
8. Apply supply voltage.
Safety note
Safety temperature limiters/monitors are items of equipment with safety function (PED) and must only be
installed, wired and commissioned by qualified and competent staff.
Retrofitting and maintenance work must only be performed by qualified staff who - through adequate
training - have achieved a recognised level of competence.
Temperature sensor type
Designation
Item
Stock code #
TRG 5-65: Nominal length
5
= 115 mm,
Fig. 4
Measuring element
, 1x Pt 100
e
392962
TRG 5-66: Nominal length
5
= 140 mm,
Fig. 4
Measuring element
, 1x Pt 100
e
392963
TRG 5-67: Nominal length
5
= 200 mm,
Fig. 4
Measuring element
, 1x Pt 100
e
392946
TRG 5-68: Nominal length
5
= 200 mm,
Fig. 4
Measuring element
, 2x Pt 100
e
392948
Spare Parts