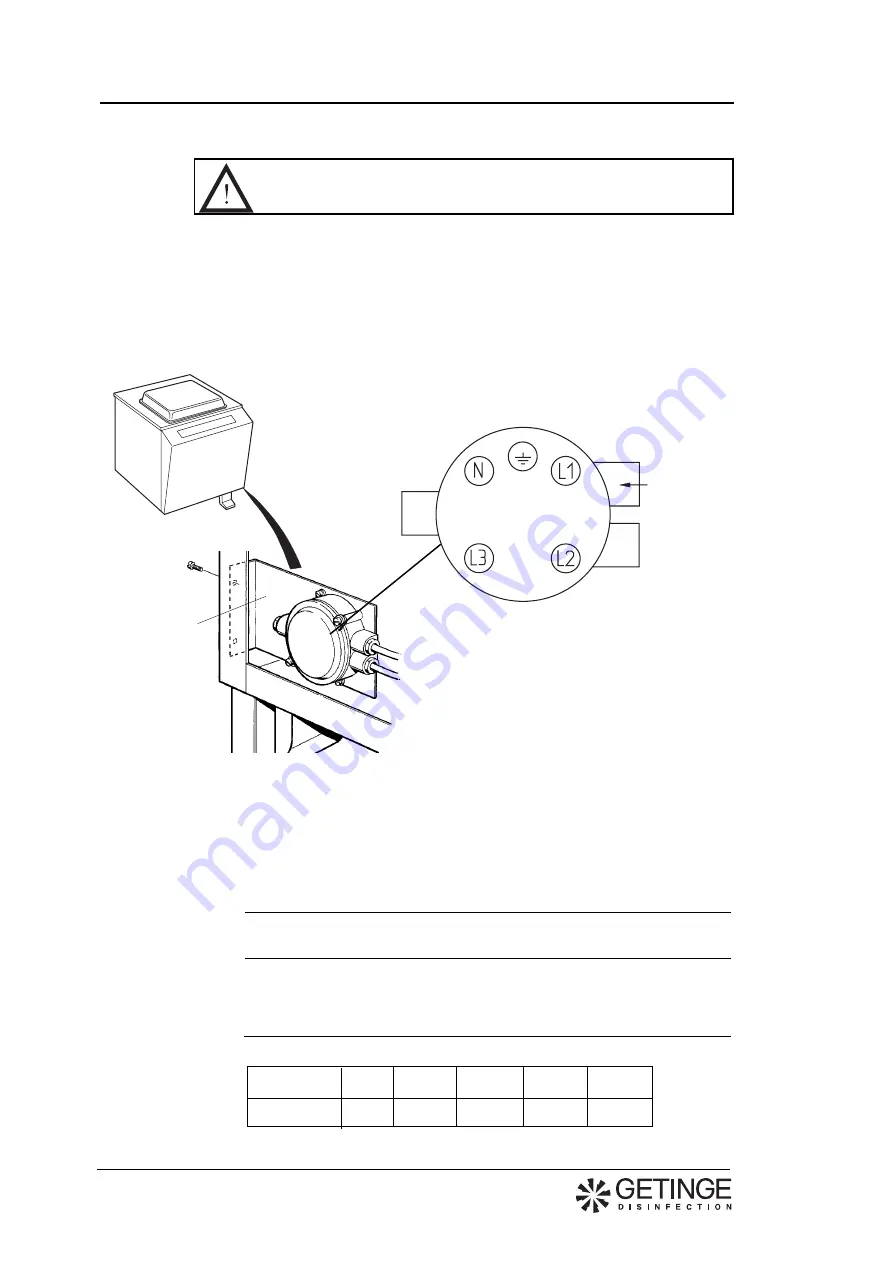
6
Flusher disinfector S-406
Installation
9904
Connection of electricity, water, drain, and possibly steam
May only be performed by authorized personnel.
• The electrical installation must include a cut-off device in the power supply
line to the machine to facilitate maintenance and servicing. The device shall
be located within easy reach on the wall.
• The terminals for electric installation are located under the cover of the
terminal block.
• Connect the disinfector to protective earth and to the voltage supply stated on
the type data plate. Check that the correct fuse is fitted. The recommended
fuse value is stated on the type plate.
• The mounting bracket for the terminal box can be unscrewed and pulled
forward to facilitate installation.
Fig. 4. Electrical connection (see electric circuit diagram in Service
instructions).
• To prevent clogging of filters and valves, flush the water pipes clean, and any
steam pipes too, that are to be connected to the machine.
• Connect the disinfector to the cold and hot water supply, and to steam supply
if used. The water and steam connections must conform to the following
requirements:
Connection (mm)
Pressure (kPa)
Flow (l/s)
Consumption (l/process)
Normal
Glassware
Cold water
15
50-500
0,2
15
8
Hot water
15
50-500
0,2
18
16
Steam
15
60-300
0,5 kg/process
• Drill out the steam jets if necesssary as per the table below:
Electrical
connection
Mounting
bracket
V296
V116
• Teflon tape is recommended for sealing the connections.
Steam pressure
kPa
60-80
80-125
125-200
200-250
250-300
5
4
3.5
3
2,5
Hole diameters
mm