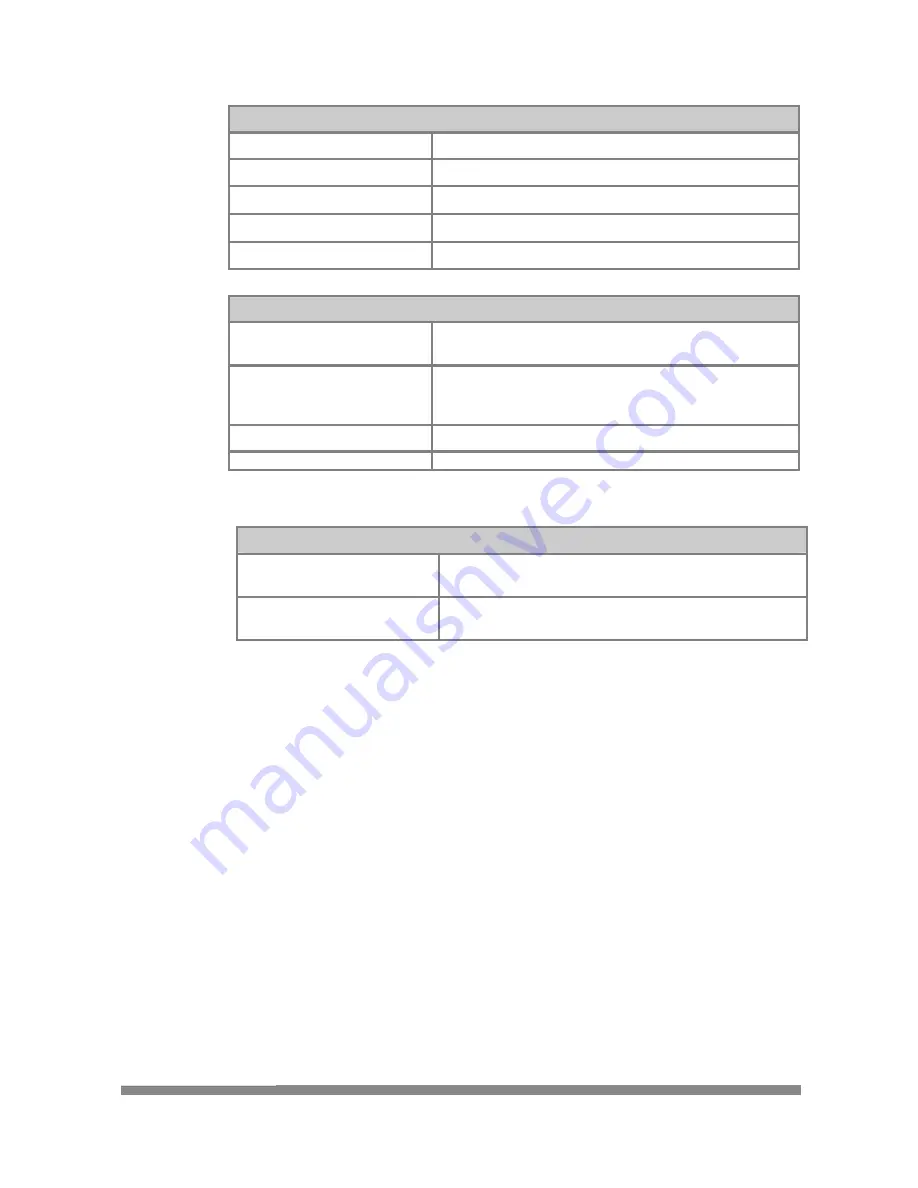
Technical Information
MetPak Base Station User Manual
Last Change
©
Gill Instruments Ltd
22 April, 2013
Page iii
Environmental – Base Station
Protection Class
IP65
EMC
EN 61326
Operating Temperature
-35
C to +70
C
Storage Temperature
-40
C to +80
C
Operating Humidity
0% to 100% Humidity
Mechanical – Base Station
External Construction
UV Stabilised white thermoplastic (Wind Sensor and
Hygroclip Mountings) and anodized Aluminium bracket.
Fittings
Stainless Steel 316 bracket fittings supplied for
clamping to a vertical pipe diameter of diameter 30mm
to 58mm.
Overall Dimensions
187mmx282mmx129mm (excluding bracket clamp)
Weight
1.6kg (including bracket)
Software – Base Station
MetView Display
Free Software providing the means of displaying data
and logging data
MetSet Configuration
Free Software providing the means of configuration of
the MetPak Base Station