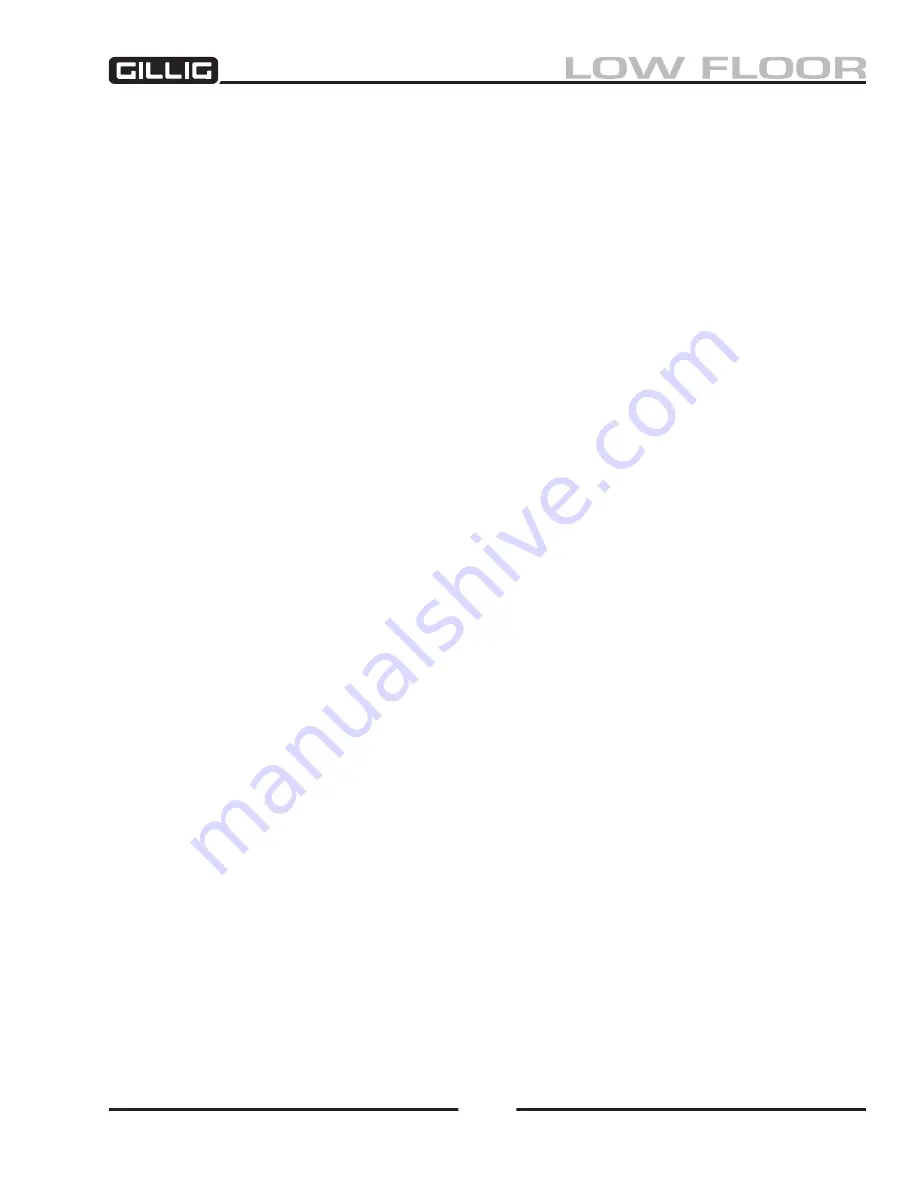
Air System
25
Assembly
Refer to Figure 6-
47
.
1. Place purge valve spring into cavity in the center of the top side of the end cover.
2. Lubricate the piston O-ring with a barium base lubricant and install the O-ring on the purge valve
piston and place the piston inside the spring installed in Step 1.
3. Turn the cover over on a flat, clean surface (Make sure the purge valve piston and spring remain
in position). Compress the spring by pushing down on the cover and align the square shank of
the purge valve piston into the mating hole in the end cover.
4. Place the washer, diaphragm retainer, diaphragm, and purge valve onto the purge valve cap
screw. Install the purge valve cap screw with the parts on it into the exhaust valve cover and
tighten the screw to 30–40 in lb (3.4–4.5 N-m) torque.
5. Install the safety valve, if removed, and tighten it to 10–35 ft-lb (15–45 N-m) torque, making
sure that the exhaust hole is pointed downward when the dryer in installed.
6. Install the thermostat, if removed. Refer to installation instruction later in this chapter.
7. Place a sealing ring on the bottom of the desiccant cartridge. Attach the cartridge to the plate
(smooth side of the plate opposite the cartridge) with four 1/4" socket head cap screws and lock
-
washers. Tighten the capscrews to 7–10 ft-lb (10–15 N-m) torque.
8. Lubricate and install the two sealing rings in the recesses of the end cover. Use a barium base
lubricant.
9. Install the check valve assembly into the end cover, making sure the holes in the metal stamping
are facing up and the tang on the check valve assembly fits into the mating recess in the cover.
10. Place the desiccant cartridge and sealing plate assembly onto the cover, taking care not to dis-
place the sealing rings. The large hole in the sealing plate must line up with the check valve and
the spiral pins in the sealing plate must enter the corresponding holes in the end cover.
11. Lubricate the outer sealing ring with the barium base lubricant and install it on the sealing plate.
Place the housing of the air dryer over the desiccant cartridge, lining up the marks made on the
end cover prior to disassembly, and retain the housing with the eight 3/8" hex head bolts, spe
-
cial washers, and crown nuts. Tighten the nuts to 25–30 ft-lb (30–40 N-m) torque. If these bolts
require replacement, ensure the replacements are at least Grade 5, as inferior grade bolts can
compromise the integrity of the air dryer and lead to premature failure.
12. Install the assembled air dryer unit on the coach by sliding it into the mounting brackets until the
mounting bracket hook catches under the lip of the cover. Tighten the mounting bolts to 6–8 ft-lb
(8–11 N-m) torque.
13. Reconnect the three air lines to the proper port as identified prior to disassembly. Reconnect the
heater wire and place the boot in position to protect the connection from the elements by forcing
the boot over the knob on the plastic cover.
14. Test the rebuilt air dryer as outlined in the Preventive Maintenance and Serviceability Checks in
the preceding section of this chapter.
Summary of Contents for LOW FLOOR
Page 18: ...Specifications 18...
Page 58: ...Preventive Maintenance 58...
Page 110: ...Engine 110...
Page 138: ...Transmission Driveline Rear Axle 138...
Page 182: ...Suspension 182...
Page 260: ...Air System 260...
Page 420: ...Electrical System 420 Deutsch DT Series Connectors...
Page 421: ...Electrical System 421...
Page 422: ...Electrical System 422 Deutsch HD 10 Series Connectors...
Page 423: ...Electrical System 423...
Page 424: ...Electrical System 424 Deutsch HD 30 Series Connectors...
Page 425: ...Electrical System 425...
Page 442: ...Heating Air Conditioning 442...
Page 492: ...Body and Interior 492 Figure 11 33 USSC Seat Assembly...
Page 493: ...Body and Interior 493 Figure 11 34 USSC Seat Suspension Assembly...
Page 495: ...Body and Interior 495 Figure 11 37 Seat Air Connections...