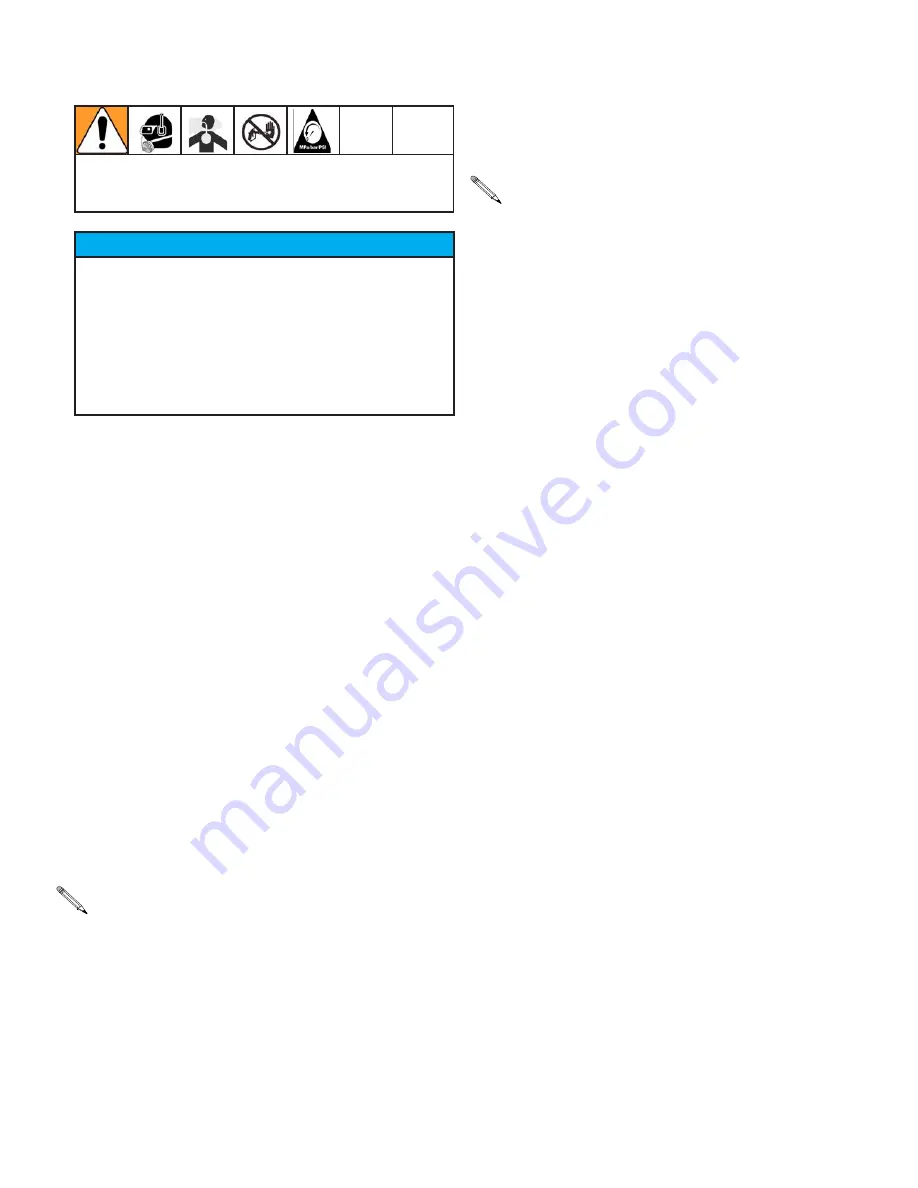
42
GC-1368N
Before performing any maintenance on this system -
Follow pressure relief procedures on page 8.
Due to the different O-Ring materials and lubricants
used in the Dispense Guns never submerge or soak any
dispense gun in any type of solvent!
Submerging or soaking any Dispense Gun will immedi-
ately void the Gun warranty.
Maintenance
It is recommended that the following service be
performed on a weekly basis.
1.
Inspect and lubricate Catalyst Slave Pump Linkage.
(See Catalyst Slave Pump User Manual.)
2.
Inspect Pump Shafts on Material and Catalyst
Pumps, making certain they are clean and free of
foreign material. Clean and lubricate as required.
For long term storage of your injection system, it is
recommended that the following procedures be
followed:
1.
Place dry nitrogen in the material drums and
secure drum.
2.
Make certain all air and material valves are in their
“OFF” position.
GlasCraft recommends that you contact your gel-
coat and/or resin supplier concerning material
pot-life during extended periods of shut-down. The
decision as to whether or not to leave material in
your system should be based on information from
your material suppliers as well as GlasCraft.
Consult your local authorized GlasCraft distributor for
more information concerning system storage.
Troubleshooting
Before altering catalyst percentage by moving the
catalyst pump to a new desired location on the ratio
arm ALWAYS ensure that the catalyst recirculation
valve is turned to the recirculation position, and the
air pressure is removed from the system.
It is absolutely essential that both streams of material
are pumped to the head without air or gas entrapped.
For example, if air is drawn into the resin stream through
the resin pump inlet system, i.e., via bad connection or
filter end coming out of resin surface, then this air if
not purged out of the machine by recirculating on by-
pass will naturally go to the head through the mixer and
into the RTM mold. This fault condition will manifest
itself in the molded part having very small bubbles;
almost in a froth like state, on the upper side of the
molded part once the mold is opened. The reason for
these bubbles being so small is due to the fact that air
coming through the mixer with the resin is mixed and
frothed before finally entering the mold.
Air or gas in the catalyst stream, leads to a different
type of fault in the molded part. This condition will be
manifest by observing when opening the mold after
injection and supposed cure, that there are wet patches
of uncured or semi-gelled resin in the molded part. The
causes attributed to this are:
1.
Air is drawn in by the catalyst pump through a bad
connection on the inlet stream from the catalyst
container or pump inlet connection.
2.
Catalyst contamination in the pump system causing
oxidation resulting in peroxide gas bubbles being
generated within the supposedly hydraulic sealed
system of the catalyst.
3.
The catalyst pump has faulty seals or is
contaminated with particles.
To ensure that the catalyst system is totally hydraulically
tight, it is expedient after a period of shut-down that the pro-
cedures in the instructions for commissioning the catalyst
stream should be repeated.
Maintenance
Isocyanate Conditions
Rev. G 6/17/2008
21
Isocyanate Conditions
Material Self-ignition
Moisture Sensitivity of
Isocyanites
Isocyanites (ISO) are catalysts used in two component
foam and polyurea coatings. ISO will react with moisture
(such as humidity) to form small, hard, abrasive crystals,
which become suspended in the fluid. Eventually a film
will form on the surface and the ISO will begin to gel,
increasing in viscosity. If used, this partially cured ISO
will reduce performance and the life of all wetted parts.
To prevent exposing ISO to moisture:
•
Always use a sealed container with a desiccant
dryer in the vent, or a nitrogen atmosphere.
Never
store ISO in an open container.
•
Keep the ISO lube pump reservoir (if installed) filled
with Graco Throat Seal Liquid (TSL), Part 206995.
The lubricant creates a barrier between the ISO and
the atmosphere.
•
Use moisture-proof hoses specifically designed for
ISO, such as those supplied with your system.
•
Never use reclaimed solvents, which may contain
moisture. Always keep solvent containers closed
when not in use.
•
Never use solvent on one side if it has been contam-
inated from the other side.
•
Always lubricate threaded parts with ISO pump oil
or grease when reassembling.
Keep Components A and
B Separate
Foam Resins with 245 fa
Blowing Agents
Some foam blowing agents will froth at temperatures
above 90°F (33°C) when not under pressure, especially
if agitated. To reduce frothing, minimize preheating in a
circulation system.
Spraying materials containing isocyanates creates
potentially harmful mists, vapors, and atomized partic-
ulates.
Read material manufacturer’s warnings and material
MSDS to know specific hazards and precautions
related to isocyanates.
Prevent inhalation of isocyanate mists, vapors, and
atomized particulates by providing sufficient ventila-
tion in the work area. If sufficient ventilation is not
available, a supplied-air respirator is required for
everyone in the work area.
To prevent contact with isocyanates, appropriate per-
sonal protective equipment, including chemically
impermeable gloves, boots, aprons, and goggles, is
also required for everyone in the work area.
Some materials may become self-igniting if applied
too thickly. Read material manufacturer’s warnings
and material MSDS.
The amount of film formation and rate of crystalli-
zation varies depending on the blend of ISO, the
humidity, and the temperature.
NOTICE
To prevent cross-contamination of the equipment’s
wetted parts,
never
interchange component A (isocy-
anate) and component B (resin) parts.
Isocyanate Conditions
Rev. G 6/17/2008
21
Isocyanate Conditions
Material Self-ignition
Moisture Sensitivity of
Isocyanites
Isocyanites (ISO) are catalysts used in two component
foam and polyurea coatings. ISO will react with moisture
(such as humidity) to form small, hard, abrasive crystals,
which become suspended in the fluid. Eventually a film
will form on the surface and the ISO will begin to gel,
increasing in viscosity. If used, this partially cured ISO
will reduce performance and the life of all wetted parts.
To prevent exposing ISO to moisture:
•
Always use a sealed container with a desiccant
dryer in the vent, or a nitrogen atmosphere.
Never
store ISO in an open container.
•
Keep the ISO lube pump reservoir (if installed) filled
with Graco Throat Seal Liquid (TSL), Part 206995.
The lubricant creates a barrier between the ISO and
the atmosphere.
•
Use moisture-proof hoses specifically designed for
ISO, such as those supplied with your system.
•
Never use reclaimed solvents, which may contain
moisture. Always keep solvent containers closed
when not in use.
•
Never use solvent on one side if it has been contam-
inated from the other side.
•
Always lubricate threaded parts with ISO pump oil
or grease when reassembling.
Keep Components A and
B Separate
Foam Resins with 245 fa
Blowing Agents
Some foam blowing agents will froth at temperatures
above 90°F (33°C) when not under pressure, especially
if agitated. To reduce frothing, minimize preheating in a
circulation system.
Spraying materials containing isocyanates creates
potentially harmful mists, vapors, and atomized partic-
ulates.
Read material manufacturer’s warnings and material
MSDS to know specific hazards and precautions
related to isocyanates.
Prevent inhalation of isocyanate mists, vapors, and
atomized particulates by providing sufficient ventila-
tion in the work area. If sufficient ventilation is not
available, a supplied-air respirator is required for
everyone in the work area.
To prevent contact with isocyanates, appropriate per-
sonal protective equipment, including chemically
impermeable gloves, boots, aprons, and goggles, is
also required for everyone in the work area.
Some materials may become self-igniting if applied
too thickly. Read material manufacturer’s warnings
and material MSDS.
The amount of film formation and rate of crystalli-
zation varies depending on the blend of ISO, the
humidity, and the temperature.
NOTICE
To prevent cross-contamination of the equipment’s
wetted parts,
never
interchange component A (isocy-
anate) and component B (resin) parts.
Notice
Summary of Contents for Spartan 3
Page 12: ...12 GC 1368N 4 Push for set up screen Start Up ...
Page 26: ...26 GC 1368N REVISION A 23280 02 SPARTAN 3 ASSEMBLY 01 Assembly Drawings ...
Page 27: ...27 GC 1368N REVISION A 23280 02 SPARTAN 3 ASSEMBLY Assembly Drawings ...
Page 28: ...28 GC 1368N REVISION A 23280 02 SPARTAN 3 ASSEMBLY Assembly Drawings ...
Page 30: ...30 GC 1368N REVISION J 23250 00 SPARTAN 3 CONTROL BOX ASSEMBLY Sub Assembly Drawings ...
Page 31: ...31 GC 1368N REVISION J 23250 00 SPARTAN 3 CONTROL BOX ASSEMBLY Sub Assembly Drawings ...
Page 32: ...32 GC 1368N REVISION J 23250 00 SPARTAN 3 CONTROL BOX ASSEMBLY Sub Assembly Drawings ...
Page 35: ...35 GC 1368N REVISION J 23250 00 SPARTAN CONTROL BOX SCHEMATIC Sub Assembly Drawings ...
Page 43: ...43 GC 1368N REVISION P 23280 00 SPARTAN 3 W PAC ASSEMBLY 01 Accessories ...
Page 44: ...44 GC 1368N REVISION P 23280 00 SPARTAN 3 W PAC ASSEMBLY Accessories ...