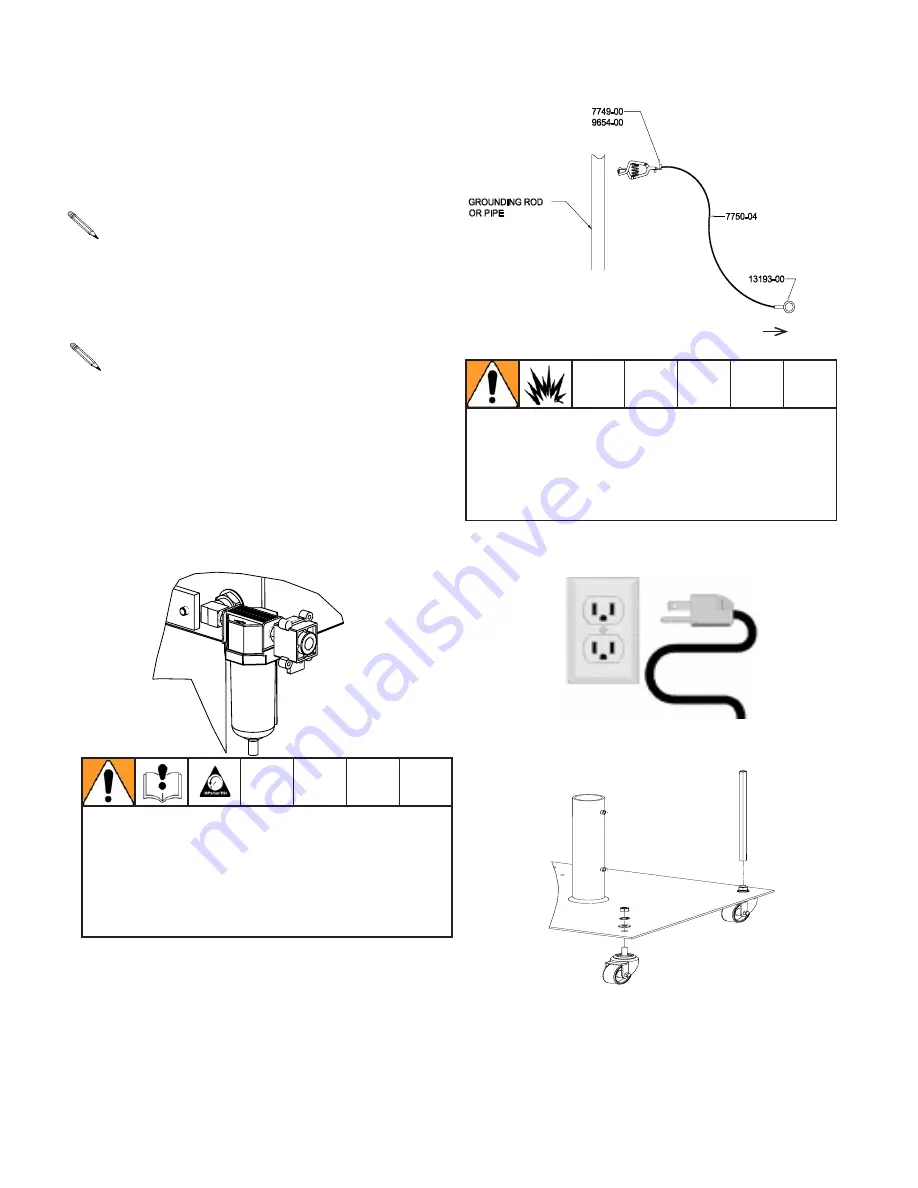
7
GC-1368N
The Spartan 3 comes complete and fitted with all
resin hoses, catalyst bottle and filters. The injection
head is fully connected to the machine circuit and
tested and secured against leaks prior to dispatch.
The following instructions are to be used as a guide
for consistent and continual operation. Any devia-
tion from the “standard operation”, usually requires
more maintenance to the equipment and material
formulation to assure consistent results. For
example: the use of fillers in resins.
Refer to specific user manuals (if available) for
detailed component start-up and shut-down instruc-
tions.
1.
Select a clean, dry air supply.
It is very important to have a clean air supply.
2.
Attach a 3/8” or larger air hose to the Air Inlet on the
yellow air lock-out valve.
Quick disconnect fittings
should not be used because they can severely limit
air flow.
3.
Attach Grounding Clamp Assembly, P/N 17440-00, to
System. Use a convenient Nut and Bolt to
secure Lug, P/N 13193-00, to slave pump.
4.
Securely attach Clamp, P/N 7749-00 to permanently
grounded rod or pipe.
5.
Plug the electrical cord into a 110 outlet.
6.
Attach 4 casters with provided lock washer, washer and
nut. Attach solvent tank support rod on back left caster.
7.
Attach solvent tank to solvent tank support rod with
provided rubber strap.
Set-Up
Isocyanate Conditions
Rev. G 6/17/2008
21
Isocyanate Conditions
Material Self-ignition
Moisture Sensitivity of
Isocyanites
Isocyanites (ISO) are catalysts used in two component
foam and polyurea coatings. ISO will react with moisture
(such as humidity) to form small, hard, abrasive crystals,
which become suspended in the fluid. Eventually a film
will form on the surface and the ISO will begin to gel,
increasing in viscosity. If used, this partially cured ISO
will reduce performance and the life of all wetted parts.
To prevent exposing ISO to moisture:
•
Always use a sealed container with a desiccant
dryer in the vent, or a nitrogen atmosphere.
Never
store ISO in an open container.
•
Keep the ISO lube pump reservoir (if installed) filled
with Graco Throat Seal Liquid (TSL), Part 206995.
The lubricant creates a barrier between the ISO and
the atmosphere.
•
Use moisture-proof hoses specifically designed for
ISO, such as those supplied with your system.
•
Never use reclaimed solvents, which may contain
moisture. Always keep solvent containers closed
when not in use.
•
Never use solvent on one side if it has been contam-
inated from the other side.
•
Always lubricate threaded parts with ISO pump oil
or grease when reassembling.
Keep Components A and
B Separate
Foam Resins with 245 fa
Blowing Agents
Some foam blowing agents will froth at temperatures
above 90°F (33°C) when not under pressure, especially
if agitated. To reduce frothing, minimize preheating in a
circulation system.
Spraying materials containing isocyanates creates
potentially harmful mists, vapors, and atomized partic-
ulates.
Read material manufacturer’s warnings and material
MSDS to know specific hazards and precautions
related to isocyanates.
Prevent inhalation of isocyanate mists, vapors, and
atomized particulates by providing sufficient ventila-
tion in the work area. If sufficient ventilation is not
available, a supplied-air respirator is required for
everyone in the work area.
To prevent contact with isocyanates, appropriate per-
sonal protective equipment, including chemically
impermeable gloves, boots, aprons, and goggles, is
also required for everyone in the work area.
Some materials may become self-igniting if applied
too thickly. Read material manufacturer’s warnings
and material MSDS.
The amount of film formation and rate of crystalli-
zation varies depending on the blend of ISO, the
humidity, and the temperature.
NOTICE
To prevent cross-contamination of the equipment’s
wetted parts,
never
interchange component A (isocy-
anate) and component B (resin) parts.
Isocyanate Conditions
Rev. G 6/17/2008
21
Isocyanate Conditions
Material Self-ignition
Moisture Sensitivity of
Isocyanites
Isocyanites (ISO) are catalysts used in two component
foam and polyurea coatings. ISO will react with moisture
(such as humidity) to form small, hard, abrasive crystals,
which become suspended in the fluid. Eventually a film
will form on the surface and the ISO will begin to gel,
increasing in viscosity. If used, this partially cured ISO
will reduce performance and the life of all wetted parts.
To prevent exposing ISO to moisture:
•
Always use a sealed container with a desiccant
dryer in the vent, or a nitrogen atmosphere.
Never
store ISO in an open container.
•
Keep the ISO lube pump reservoir (if installed) filled
with Graco Throat Seal Liquid (TSL), Part 206995.
The lubricant creates a barrier between the ISO and
the atmosphere.
•
Use moisture-proof hoses specifically designed for
ISO, such as those supplied with your system.
•
Never use reclaimed solvents, which may contain
moisture. Always keep solvent containers closed
when not in use.
•
Never use solvent on one side if it has been contam-
inated from the other side.
•
Always lubricate threaded parts with ISO pump oil
or grease when reassembling.
Keep Components A and
B Separate
Foam Resins with 245 fa
Blowing Agents
Some foam blowing agents will froth at temperatures
above 90°F (33°C) when not under pressure, especially
if agitated. To reduce frothing, minimize preheating in a
circulation system.
Spraying materials containing isocyanates creates
potentially harmful mists, vapors, and atomized partic-
ulates.
Read material manufacturer’s warnings and material
MSDS to know specific hazards and precautions
related to isocyanates.
Prevent inhalation of isocyanate mists, vapors, and
atomized particulates by providing sufficient ventila-
tion in the work area. If sufficient ventilation is not
available, a supplied-air respirator is required for
everyone in the work area.
To prevent contact with isocyanates, appropriate per-
sonal protective equipment, including chemically
impermeable gloves, boots, aprons, and goggles, is
also required for everyone in the work area.
Some materials may become self-igniting if applied
too thickly. Read material manufacturer’s warnings
and material MSDS.
The amount of film formation and rate of crystalli-
zation varies depending on the blend of ISO, the
humidity, and the temperature.
NOTICE
To prevent cross-contamination of the equipment’s
wetted parts,
never
interchange component A (isocy-
anate) and component B (resin) parts.
Before turning on main air:
a. Check all fittings, making certain they are securely
tightened.
b. Make sure all regulators are set to zero (turn all
the way to the left).
This should be done before air or material of any kind
is introduced into the system.
Fire and Explosion Hazard
14
Rev. G 6/17/2008
Skin Injection Hazard
Use with high pressure equipment, generally equipment with pressure rating of 900 psi or higher. There are 2 ver-
sions of this section.
1)
manual guns,
2)
UL-1450 compliant equipment
3)
automatic guns,
/
dispense valves,/lubrica-
tion valves,
4)
heated hoses. Since the text contains mostly “Do not” statements, the symbols have lines through
them.
WARNING
SKIN INJECTION HAZARD
- Basic
High-pressure fluid from gun, hose leaks, or ruptured components will pierce skin. This may look like just
a cut, but it is a serious injury that can result in amputation.
Get immediate surgical treatment.
•
Do not point gun at anyone or at any part of the body.
•
Do not put your hand over the spray tip.
•
Do not stop or deflect leaks with your hand, body, glove, or rag.
•
Do not spray without tip guard and trigger guard installed.
•
Engage trigger lock when not spraying.
•
Follow
Pressure Relief Procedure
in this manual, when you stop spraying and before cleaning,
checking, or servicing equipment.
SKIN INJECTION HAZARD
- Use with UL1450 Compliance
Do not aim the gun at, or spray any person or animal.
•
Keep hands and other body parts away from the discharge. For example, do not try to stop leaks with
any part of the body.
•
Always use the nozzle tip guard. Do not spray without nozzle tip guard in place.
•
Use Graco nozzle tips.
•
Use caution when cleaning and changing nozzle tips. in the case where the nozzle tip clogs while
spraying, follow the
Pressure Relief Procedure
for turning off the unit and relieving the pressure
before removing the nozzle tip to clean.
•
Do not leave the unit energized or under pressure while unattended. When the unit is not in use, turn
off the unit and follow the
Pressure Relief Procedure
for turning off the unit.
•
High-pressure spray is able to inject toxins into the body and cause serious bodily injury. In the event
that injection occurs,
get immediate surgical treatment
.
•
Check hoses and parts for signs of damage. Replace any damaged hoses or parts.
•
This system is capable of producing
XXXX
psi. Use Graco replacement parts or accessories that are
rated a minimum of
XXXX
psi.
•
Always engage the trigger lock when not spraying. Verify the trigger lock is functioning properly.
•
Verify that all connections are secure before operating the unit.
•
Know how to stop the unit and bleed pressure quickly. Be thoroughly familiar with the controls.
Whenever flammable or combustible liquids are trans
-
ferred from one container to another, both containers
shall be effectively bonded and grounded to dissipate
static electricity.
For further information see.....
NFPA 77,Recommended Practice on Static Electricity.
TO SLAVE PUMP
Summary of Contents for Spartan 3
Page 12: ...12 GC 1368N 4 Push for set up screen Start Up ...
Page 26: ...26 GC 1368N REVISION A 23280 02 SPARTAN 3 ASSEMBLY 01 Assembly Drawings ...
Page 27: ...27 GC 1368N REVISION A 23280 02 SPARTAN 3 ASSEMBLY Assembly Drawings ...
Page 28: ...28 GC 1368N REVISION A 23280 02 SPARTAN 3 ASSEMBLY Assembly Drawings ...
Page 30: ...30 GC 1368N REVISION J 23250 00 SPARTAN 3 CONTROL BOX ASSEMBLY Sub Assembly Drawings ...
Page 31: ...31 GC 1368N REVISION J 23250 00 SPARTAN 3 CONTROL BOX ASSEMBLY Sub Assembly Drawings ...
Page 32: ...32 GC 1368N REVISION J 23250 00 SPARTAN 3 CONTROL BOX ASSEMBLY Sub Assembly Drawings ...
Page 35: ...35 GC 1368N REVISION J 23250 00 SPARTAN CONTROL BOX SCHEMATIC Sub Assembly Drawings ...
Page 43: ...43 GC 1368N REVISION P 23280 00 SPARTAN 3 W PAC ASSEMBLY 01 Accessories ...
Page 44: ...44 GC 1368N REVISION P 23280 00 SPARTAN 3 W PAC ASSEMBLY Accessories ...