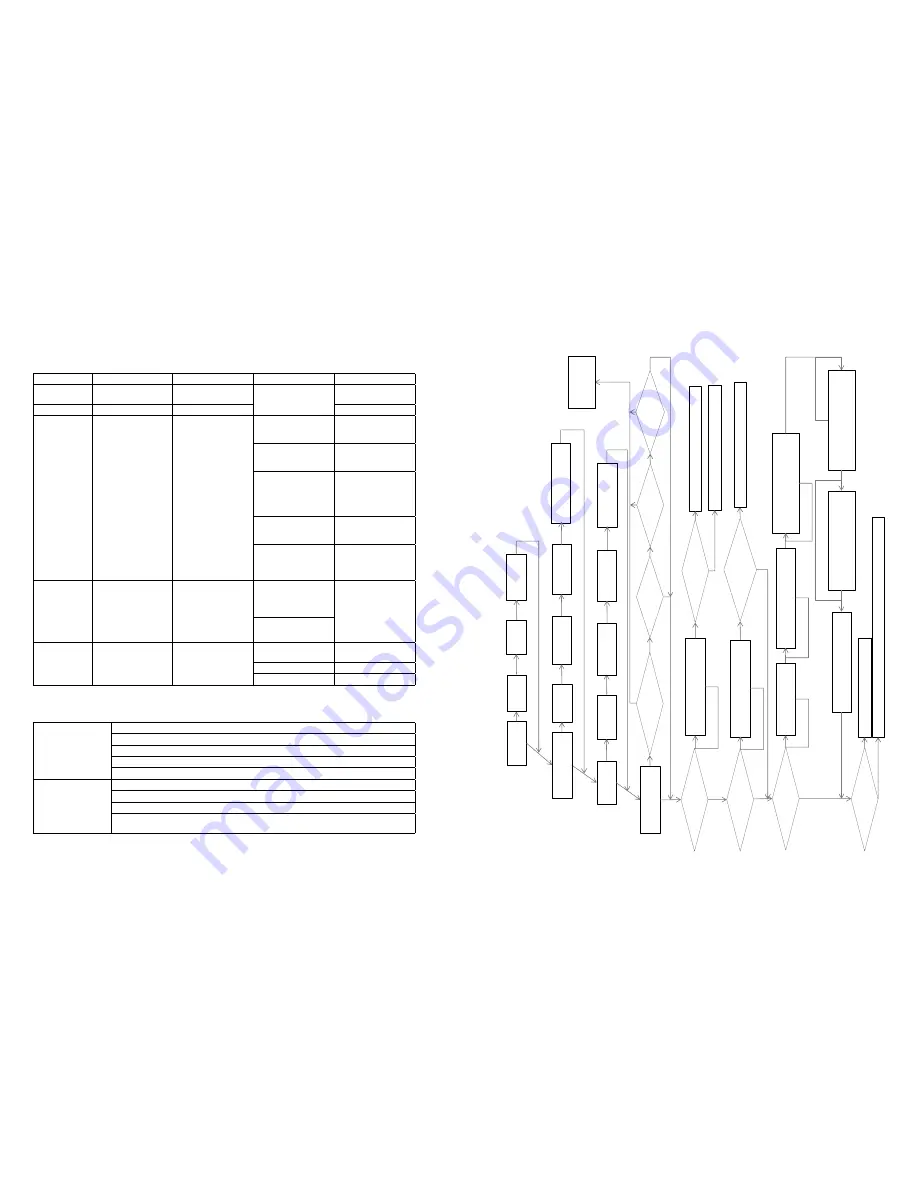
Page 28
Page 29
SERVICING AND MAINTENANCE
FAULT FINDING
Check pump electrical circuits
LED
Meaning
Diagnosis
Cause
Remedy
Lights green
Normal running
Pump runs according
PWM input
Normal operation
n/a
Blinks quick green
Normal stopped
Pump in standby
n/a
Blinks red/ green
Abnormal running mode
-pump stopped but still
functional
The pump has stopped
due to external failure
Pump restarts by itself
after the fault has
disappeared
Under voltage U<160 V
or
Over voltage U>253 V
Check voltage supply
195 V <U< 253 V
Pump overheating:
temperature inside motor
too high
Check water and
ambient temperature
Over speed:
the pump rotor is driven
by an external flow above
the maximum allowed
value
Ensure that there is no
other external flow (other
pump running) on
system
Over current:
the stator winding is in
short circuit due to water
Check for leakage
application on
application
Overload of motor:
friction due to particles
and/or impeller blocked
with debris
Check installation water
quality, clean system if
debris
Blinks red
Pump out of function
Pump stopped (blocked)
Blockage:
the pumps is fully
blocked due to debris in
system
Check for blockage.
Turn ON/OFF to reset
the pump by unplugging
the power supply
If the pumps still blinking
red after a power reset
then replace the pump
Faulty electronic module
and/or faulty motor
LED off
No power supply
No voltage on electronics Pump is not connected to
power supply
Check cable connection
LED is damaged
Check if pump is running
Electronics are damaged
Replace pump
Check plumbing components
CW In line filter
Isolate the CW mains supply at the servicing valve
Open HW taps to relieve the pressure
Undo securing nut ensuring that any remaining water is collected
Remove filter and clean it
The flow regulator can be checked at the same time by removing the upper pipe section.
Thermal store return
check valve + return
servicing valve
Isolate both servicing valves
Drain water from the section between the servicing valves
Remove the bottom pipe section
Check for free movement of the check valve incorporated in the body. Remove and replace if the check
valve sticks.
SERVICING AND MAINTENANCE
FAULT FINDING
Che
ck
pl
um
bi
ng
TS
fu
ll
of
w
at
er?
W
ate
r
m
ai
ns
o
n?
PH
E
pi
pe
wo
rk
air
lo
cke
d?
Che
ck
se
ns
ors
Ov
er
he
at
lin
k
pr
ese
nt
in
J7
Se
nso
rs
pl
ug
ge
d
in
se
cu
rely?
Sen
sor
s p
rov
id
in
g
cor
rect
sig
na
l t
o
PC
B?
Che
ck
El
ect
rical
suppl
y
Elect
rica
lly
sa
fe
?
Co
m
po
ne
nt
s
sh
or
t c
ircu
ited
?
W
iri
ng
a
s pe
r
ci
rc
ui
t di
ag
ram
?
Pum
p
LE
D
on
?
N
Ch
eck
c
ab
le
con
nect
ion
s
ecu
re
an
d
res
ist
an
ce
in
ca
ble
Pum
p
run
ni
ng
?
LED
is
da
m
ag
ed
pu
m
p
re
pl
ac
em
ent
o
pt
io
na
l
OK
?
Y
Reso
lv
e
N
Elect
ron
ics
d
am
ag
ed
rep
la
ce
pum
p
LE
D
Bl
inks r
ed?
Y
Y
Che
ck
fo
r bl
oc
kag
e
in
pi
pe
wo
rk
or
p
um
p
ho
us
ing
N
LED
con
tin
ues
to
Blin
k
red
a
fter
p
ow
er
re
set
Y
M
ot
or
o
r El
ec
tr
oni
cs
da
m
ag
ed
re
pl
ac
e
pu
m
p
OK
?
OK
?
OK
?
OK
?
OK
?
OK
?
OK
?
W
iri
ng
a
s pe
r c
irc
ui
t di
ag
ram
&
p
ola
rit
y
cor
rect
?
OK
?
OK
?
Sen
sor
s in
cor
rect
loca
tion
?
OK
?
OK
?
OK
?
N
OK
?
OK
?
LE
D
Bl
inks r
ed
&
gr
een
?
Reso
lv
e
OK
?
U
nder
v
ol
tag
e
U<
160
V
or
Over
vo
ltag
e U>
253
V
Reso
lv
e
OK
?
Pum
p
ov
er
he
at
ing
: C
hec
k
wat
er
an
d
am
bi
ent
te
m
pe
rat
ur
es
Reso
lv
e
Pum
p
O
ve
r s
pe
ed
E
ns
ur
e t
ha
t t
he
re
is
no
oth
er
ex
ter
na
l f
low
(ot
he
r
pu
m
p
run
ni
ng
) on
sy
st
em
OK
?
Reso
lv
e
O
ve
r c
ur
re
nt
t
he
st
at
or
wi
nd
ing
is in
sh
or
t c
ircu
it
due
to
wat
er
. C
he
ck
for
lea
k
OK
?
Reso
lv
e
Ov
er
loa
d
of
m
ot
or
: f
rict
ion
d
ue
to
pa
rt
icles
or
im
pe
llor
b
lock
ed
. C
lea
n
de
br
is
fr
om
sys
tem
N
ot
e p
um
p
wi
ll
re
st
ar
t b
y i
tse
lf
whe
n
the
fau
lt
di
sa
pp
ear
s
OK
?
Reso
lv
e
LE
D
Bl
ink
s gr
ee
n?
N
or
m
al
st
opp
ed:
pu
m
p
in
st
an
db
y
N
or
m
al
run
ni
ng
: p
um
p
run
s ac
co
rdi
ng
to
P
W
M
si
gna
l an
d
the
L
ED
wi
ll
be
c
ons
tan
tly
o
n
Y
N
Che
ck
board
out
put
to
pum
p
Ch
ec
k
po
we
r o
ut
pu
t t
o
pu
m
p
J8
L(
10)
,
N(8
),
E(6
)
Ch
ec
k
PW
M
fr
eq
uen
cy
Che
ck
Du
ty
Cy
cle
Y
Bo
ard
el
ect
ro
nics
da
m
ag
ed
N
Sop
his
tica
ted
m
ul
ti
m
et
er
av
ai
lab
le
Y
N
OK
?
OK
?
N
N