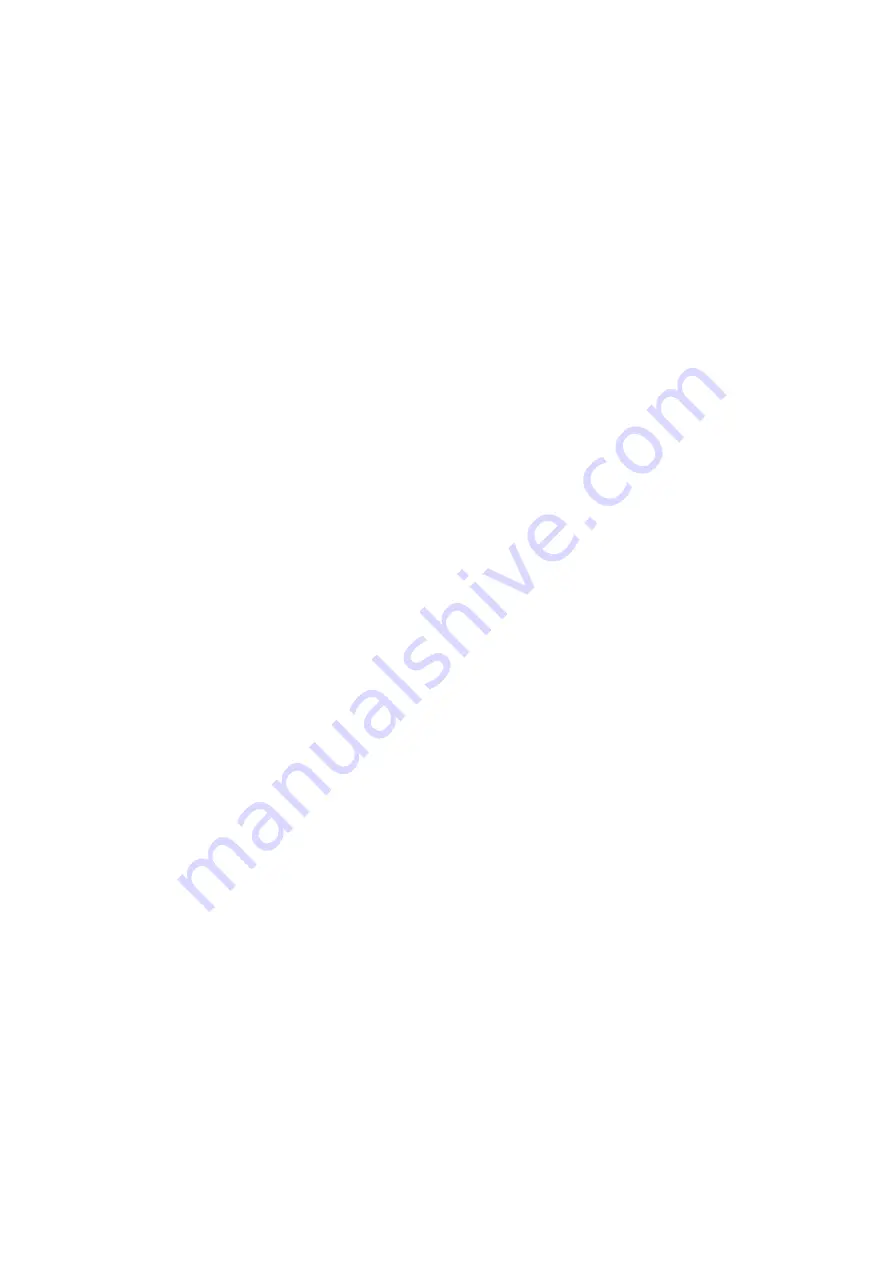
Page 39
SERVICING AND MAINTENANCE
FAULT FINDING
Circulating Fluid In Thermal Store Pipework
• The BoilerMate and the thermal store pipework must have completed filling prior
to switching the electricity supply to the PWM controller PCB. If there is no water
in these pipes then there may be significant wear on the PWM pump.
• This can be confirmed by
-
Checking the thermal store pipework servicing valves are open
-
Loosening the connection points on the thermal store pipework in a
systematic manner and checking for water presence.
-
Confirming that the feed and expansion tank has completed filling and the
servicing valve is open.
Cold Mains Water Supply To Plate Heat Exchanger And Hot Water Taps
• Confirm that the CW mains stop valve is open
• Open all HW taps and confirm that the water runs freely and that any air is bled
from the DHW system
• Determine the maximum flow rate obtained and record
• 15l/min for all BoilerMate products currently limited with a flow restrictor
• If flow rate not as expected determine the cause and rectify
-
Clean inline strainer
-
Check the flow restrictor is present and not blocked. It is located in the top
of the inline strainer
Power On
• Switch on the Local fuse spur and observe the PWM pump
• Open a HW tap and observe the PWM pump
• The green LED will be constantly lit showing the pump has a power supply and is
running to generate HW
NOTE: -The thermal store will only produce hot water when it is hot enough. A mid
40°C thermal store temperature will provide some hot water, higher thermal store
temperatures will provide more.
Inline Scale Inhibitor (If Ftted)
• Check power supply
• PWM Controller PCB supplies a maximum of 12vDC/300mA to the Scale inhibition
board. (From J3)
• Check dip switches set correctly
Summary of Contents for BOILERMATE OV PP
Page 47: ...Page 47 APPENDIX APPENDIX B ...