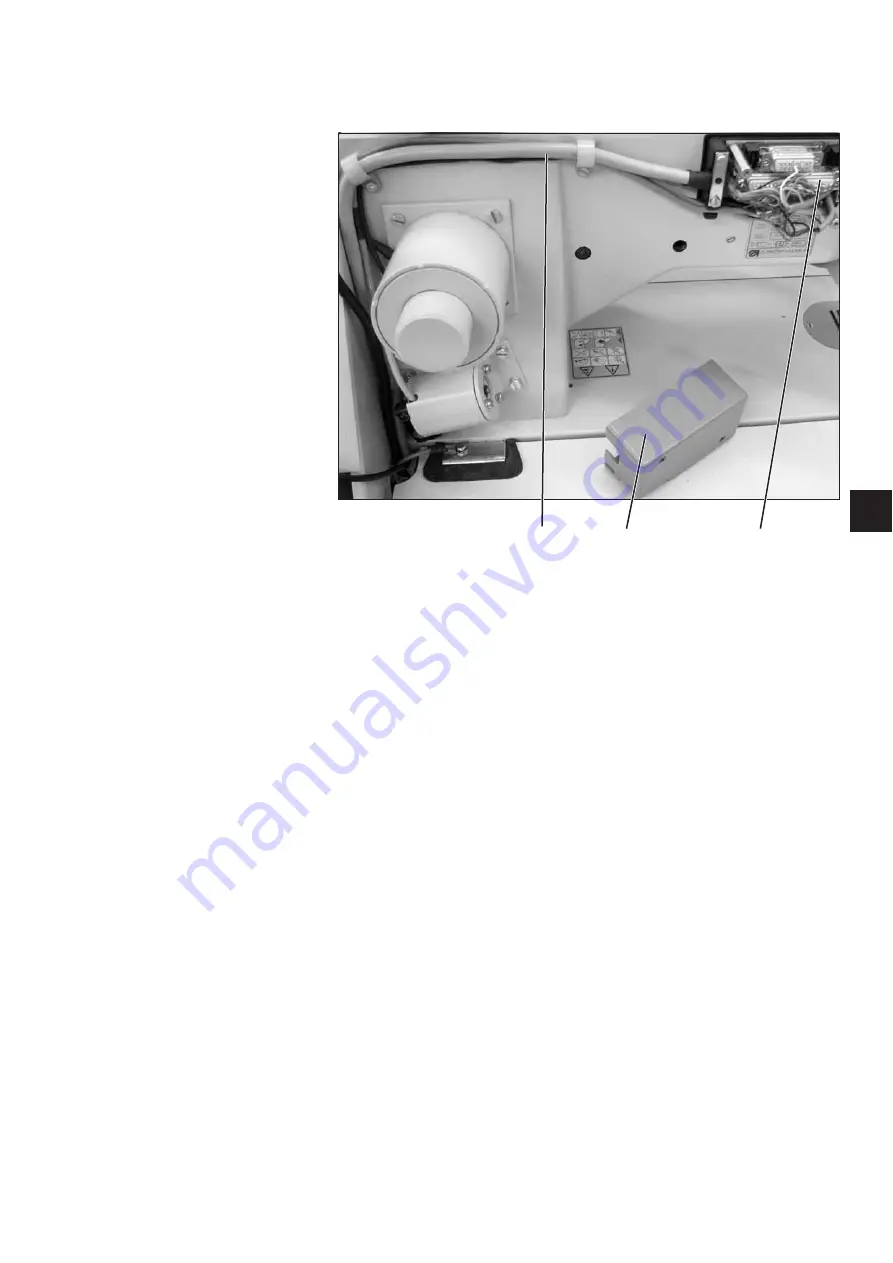
4.5
Mounting of connecting cable
–
If the machine is equipped with the positioning motor, the machine
head is electrically connected to the motor control box by means of
a connecting cable (1). The connecting cable is included in the
accessories.
–
Remove the distribution case cover (2).
–
Install the connecting cable (1) according to the picture.
–
Connect the connector (3) and mount the distribution box cover
back again.
–
Pull the connecting cable (1) under the table top according to the
picture and connect it to the motor control box.
15
GB
1
2
3
www.ae-sewingmachines.co.uk