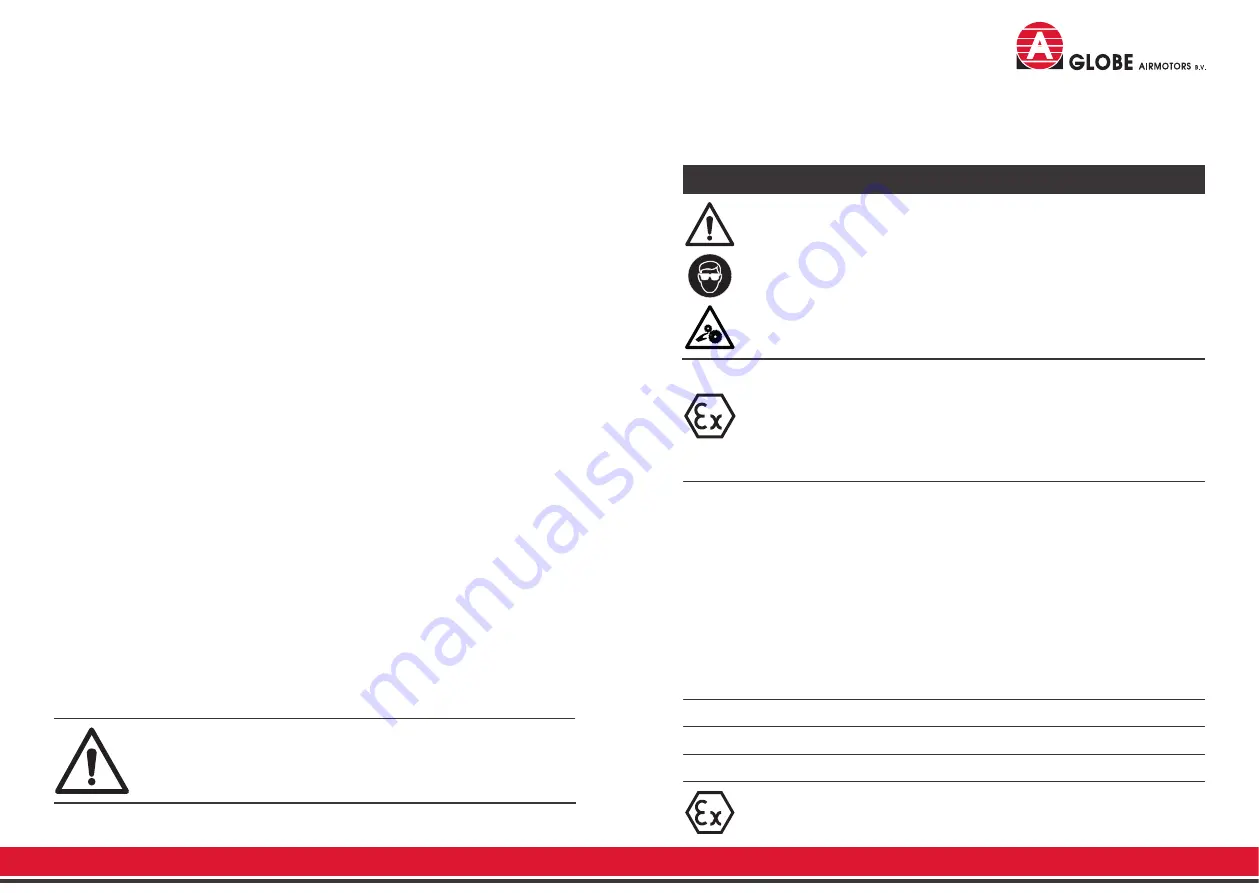
4 ·
· 5
MANUAL | VA10J&X | VS10C | VA10C | ATEX certified
MANUAL | VA10J&X | VS10C | VA10C | ATEX certified
»
To check that the air motor is designed for use
in hazardous applications read the air motor
label:
»
Hazardous zone
»
Hazardous category
»
Equipment group
»
Temperature class
»
Maximum surface temperatures
»
Check the air motor before installation and
operation to see if it’s not damaged.
»
Any products that are driven by the air motor
must meet appropriate ATEX approval as well
to be used in a hazardous area.
»
The air motor should be connected to the
earth with a maximum earth resistance of
1Mohm. The motor can be earthed by con-
necting the motor to a base plate/gearbox
etc.
»
The ambient temperature range of the motor
(-20°C to +60°C) should be observed at all
times.
»
When mounting the engine on a construction
or when something is mounted on the shaft of
the air motor. Make sure that the alignment is
straight to prevent too much force on the shaft.
»
An air filter should be placed in the airline
with at least 64 micron near the air motor.
»
Clean surface of air motor unit thoroughly of
all dustproofing products, contaminants and
other impurities. Do this outside the hazardous
area or clean only with a damp cloth.
»
A lubricator must be placed inside the main
airline near the motor. The lubricator unit
should have a bowl with enough oil for
operation and should allow the user to control
the amount of oil drop per minute going to
the motor.
»
Check airline oil every time before starting.
Air motor should be supplied with oil of a
viscosity of 32. This type of oil is flammable at
a temperature of 218°C.
»
Air supply to the motor should always be
taken from non-hazardous area.
»
In case the motor is exposed to high vibrati-
ons during operation and when not in ope-
ration, please contact the manufacturer. High
vibrations might lead to increased inspection
interval of the bearings.
»
Mounting positions
It’s important that no dust or debris can
accumulate at the output shaft. This may
damage the shaft seal. If the motor is
built in a closed system or construction
so that no dust or debris can get in
contact with the output shaft the air
motor can be used in any orientation.
If the motor is used is such way that the
output shaft is in contact with explosive
environment the mounting position
is limited from horizontal to vertical
downwards. It is not allowed for the
shaft to point in any angle upwards.
Checklist to comply to ATEX:
WARNING: POTENTIAL ELECTROSTATIC CHARGING HAZARD
Before use clean only with damp cloth.
Installation
Correct installation is your responsibility!
Make sure you have the proper installation conditions.
Install proper guard around the output shaft if needed.
WARNING - Injury hazard
Wear eye protection: Airflow from product may contain solid or liquid materials that can
result in eye or skin damage.
Failure to follow these instructions can result in serious injury or property damage.
It’s important that no dust or debris can accumulate at the output shaft. This may
damage the shaft seal. If the motor is built in a closed system or construction so that
no dust or debris can get in contact with the output shaft the air motor can be used
in any orientation. If the motor is used is such way that the output shaft is in contact
with explosive environment the mounting position is limited from horizontal to vertical
downwards. It is not allowed for the shaft to point in any angle upwards.
In order to guarantee the maximum performance and service life of these motors it is essential that
the following points are strictly observed and obeyed.
Mounting to construction
»
Mount the unit to the construction. Care should be taken, when fitting drive components to the
shaft, that excessive force is not used. This will upset the shaft alignments which has been kept to a
minimum in order to give high motor performance.
»
Use the proper sized fasteners.
»
Axial loads must be kept to a minimum.
»
Max. radial load midway along shaft as shown in graph below:
Air motor
V1
V2
V4
V6
V8
V10
V12
LBF
4
90
40
70
140
400
157
N
18
400
170
300
620
1.750
700
Ground the motor to the earth with a maximum earth resistance of 1Mohm.