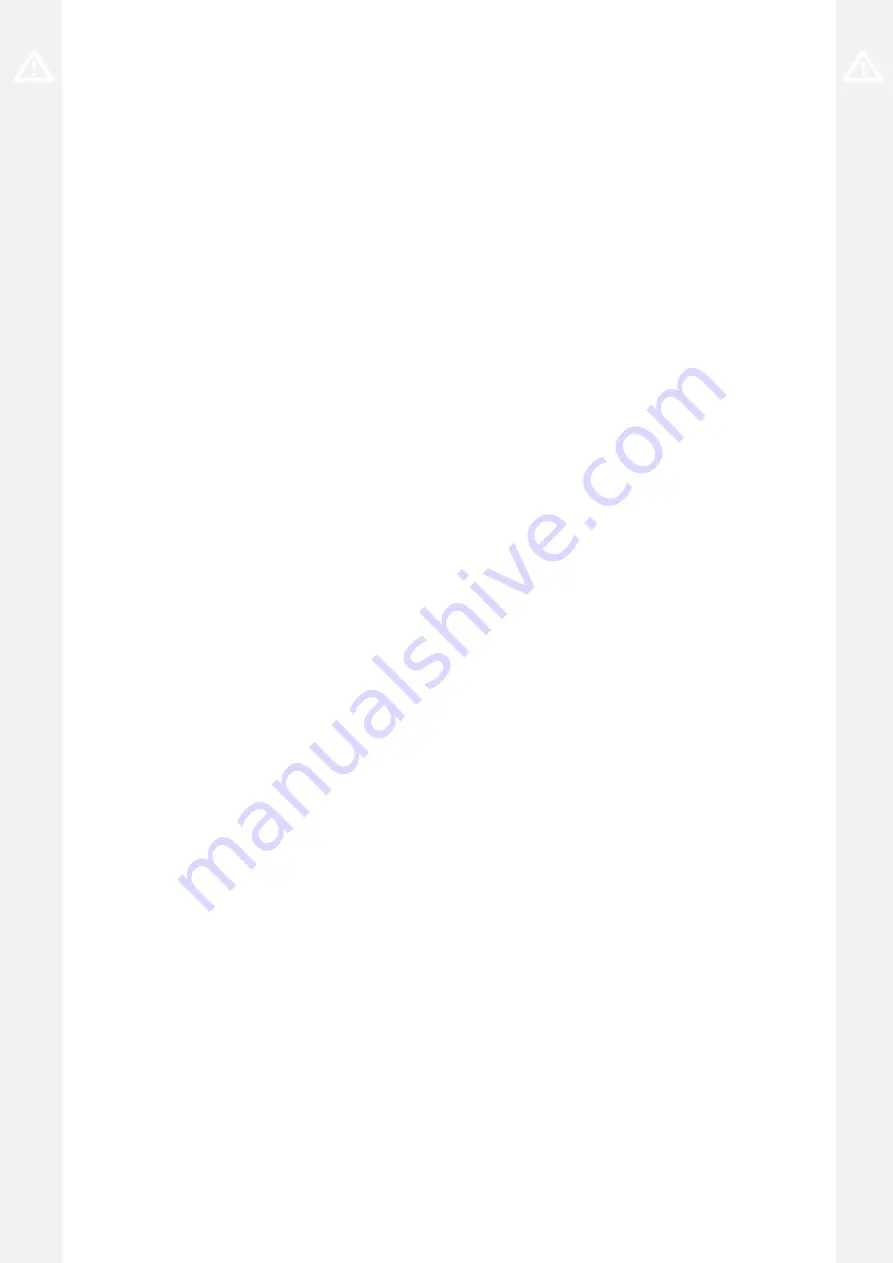
4
Installation and maintenance instructions Compact 0020313973_01
▶
Do not use any electrical switches, mains
plugs, doorbells, telephones or other com-
munication systems in the building.
▶
If it is safe to do so, close the emergency
control valve or the main isolator.
▶
If possible, close the gas stopcock on the
product.
▶
Warn other occupants in the building by
yelling or banging on doors or walls.
▶
Leave the building immediately and ensure
that others do not enter the building.
▶
Notify the gas supply company or
the Emergency Service Provider
+44 (0) 800 111999 by telephone once you
are outside of the building.
1.3.2 Flue gas
Flue gases may cause poisoning, while hot
flue gases may also cause burns. Flue gases
must therefore never be allowed to escape
uncontrollably.
What to do if you smell flue gas in the prop-
erty:
▶
Open all accessible doors and windows
fully to provide ventilation.
▶
Decommission the product.
▶
Check the flue gas routes in the product
and the flue gas diversions.
To prevent flue gas exit:
▶
Only operate the product if the air/flue pipe
has been completely installed.
▶
With the exception of short periods for
testing purposes, only operate the product
when the front casing is installed and
closed.
▶
In order to operate the product, ensure that
the condensate siphon is always full.
–
Water seal level for B23 or B23P unit
types with condensate siphon (third-
party accessory):
≥
200 mm
To ensure that the seals are not damaged:
▶
Instead of grease, use only water or com-
mercially available soft soap to aid installa-
tion.
1.3.3 Air supply
Unsuitable or insufficient combustion and
room air may lead to material damage, but
also to life-threatening situations.
To ensure that the combustion air supply is
sufficient during open-flued operation:
▶
Ensure that the air supply to the product's
installation room is permanently unobstruc-
ted and sufficient in accordance with the
relevant ventilation requirements. This also
applies, in particular, for cupboard installa-
tions.
To prevent corrosion on the product and in
the flue system:
▶
Ensure that the combustion air supply is
free from sprays, solvents, chlorinated
cleaning agents, paint, adhesives, am-
monia compounds, dust or similar sub-
stances.
▶
Ensure that no chemical substances are
stored at the installation site.
▶
If you are installing the product in
hairdressing salons, painter's or joiner's
workshops, cleaning businesses or similar
locations, choose a separate installation
room in which the room air is technically
free of chemical substances.
1.3.4 Electricity
The power supply terminals L and N remain
live.
To prevent electric shocks, proceed as fol-
lows before working on the product:
▶
Disconnect the product from the power
supply by switching off all power supplies
at all poles (electrical partition with a con-
tact gap of at least 3 mm, e.g. fuse or cir-
cuit breaker) or remove the mains plug (if
present).
▶
Secure against being switched back on
again.
▶
Wait at least three minutes until the con-
densers have discharged.
▶
Check that there is no voltage.
1.3.5 Weight
To prevent injuries when transporting the
product:
▶
Make sure that the product is transported
by at least two people.
1.3.6 Explosive and flammable substances
To prevent explosions and fire:
Summary of Contents for Compact 24c-AS/1
Page 59: ......