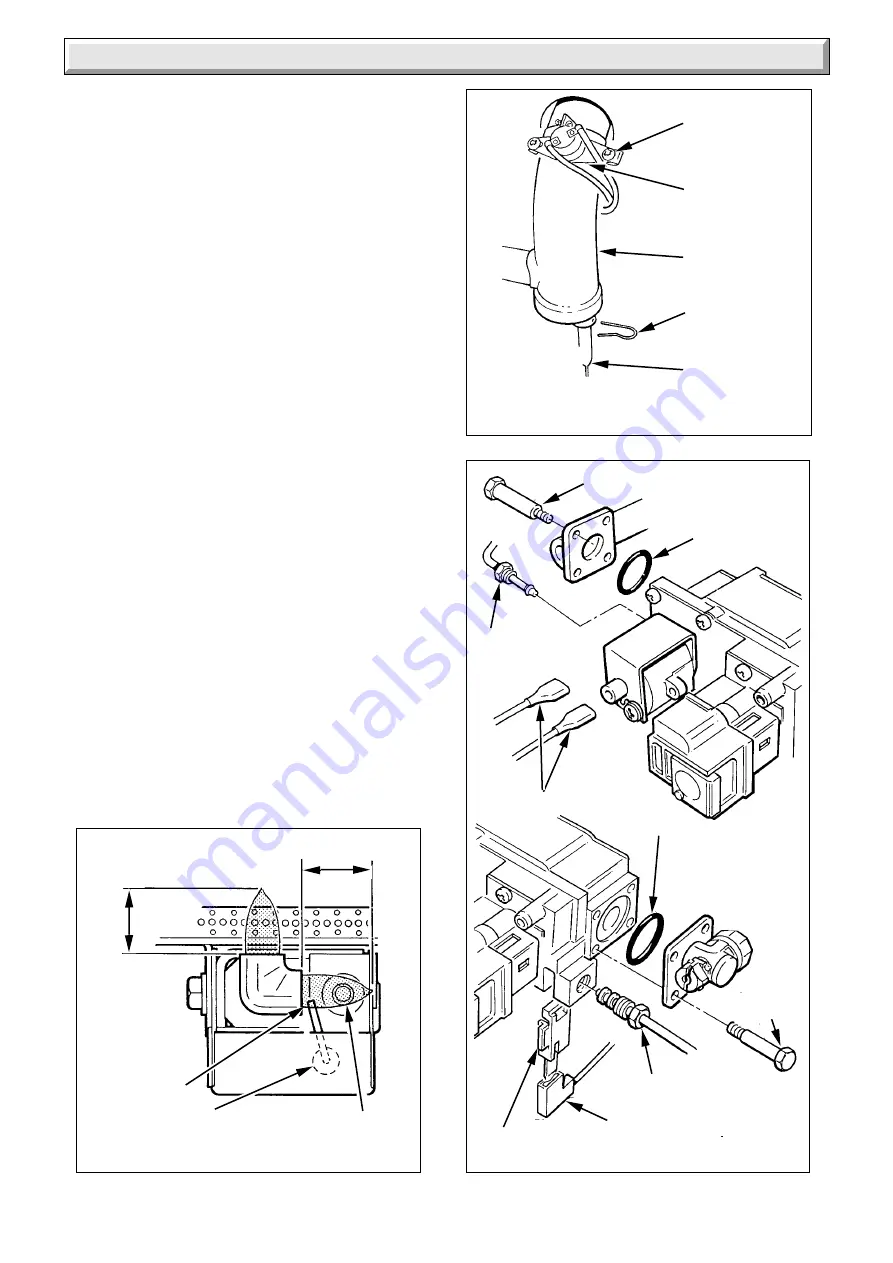
16
221462C
7 Servicing and Replacement of Parts
7.4 Pilot Burner and Injector - Service
Generally follow the instructions given in Section 7.1.
With the main case, inner case and controls cover etc., removed
as above, pull off ignition lead from the electrode.
Unscrew the tubing nut at the base of the pilot burner, releasing
the pilot pipe. Remove the pilot injector by unscrewing from the
pilot burner.
Unscrew the thermocouple nut to release the thermocouple
from the pilot burner.
Support the main burner and remove the two screws and
washers securing the pilot burner and shield to burner.
Remove the complete assembly.
Lift the pilot burner off.
Take care not to damage the electrode.
When replacing make sure the spark gap is as shown in diagram
7.7.
Check the pilot burner flame lengths are as shown in diagram
7.7.
7.5 Thermocouple
Generally follow the instructions given in Section 7.1.
Unscrew the thermocouple nut to release from the pilot burner,
see diagram 7.3.
Disconnect the thermocouple from the gas valve, see diagram
7.9.
Use the old thermocouple as a pattern when fitting the new one.
Do not tighten more than a quarter turn beyond finger tight at the
gas valve.
Check the electrode spark gap, see diagram 7.7.
Diagram 7.7
PILOT FLAME AND
SPARK GAP
14 to 17mm
14 to 17mm
THERMOCOUPLE
ELECTRODE
SPARK GAP
3 TO 4mm
1053
Diagram 7.8
THERMOSTAT
PHIAL/OVERHEAT
CUT-OFF
OVERHEAT
CUT-OFF
HEAT
EXCHANGER
RETAINING
CLIP
THERMOSTAT
PHIAL
CUT-OFF
SECURING
SCREW(S)
0951
GAS VALVE ASSEMBLY
Diagram 7.9
GAS SERVICE
COCK
(Shown Off)
'O' RING
INTERRUPTER
EXT. SCREW (4)
'O' RING
PILOT
TUBE
NUT
GAS
VALVE
CONNECTORS
THERMOCOUPLE NUT
ELECTRICAL
CONNECTOR
2414
EXT.
SCREW (4)