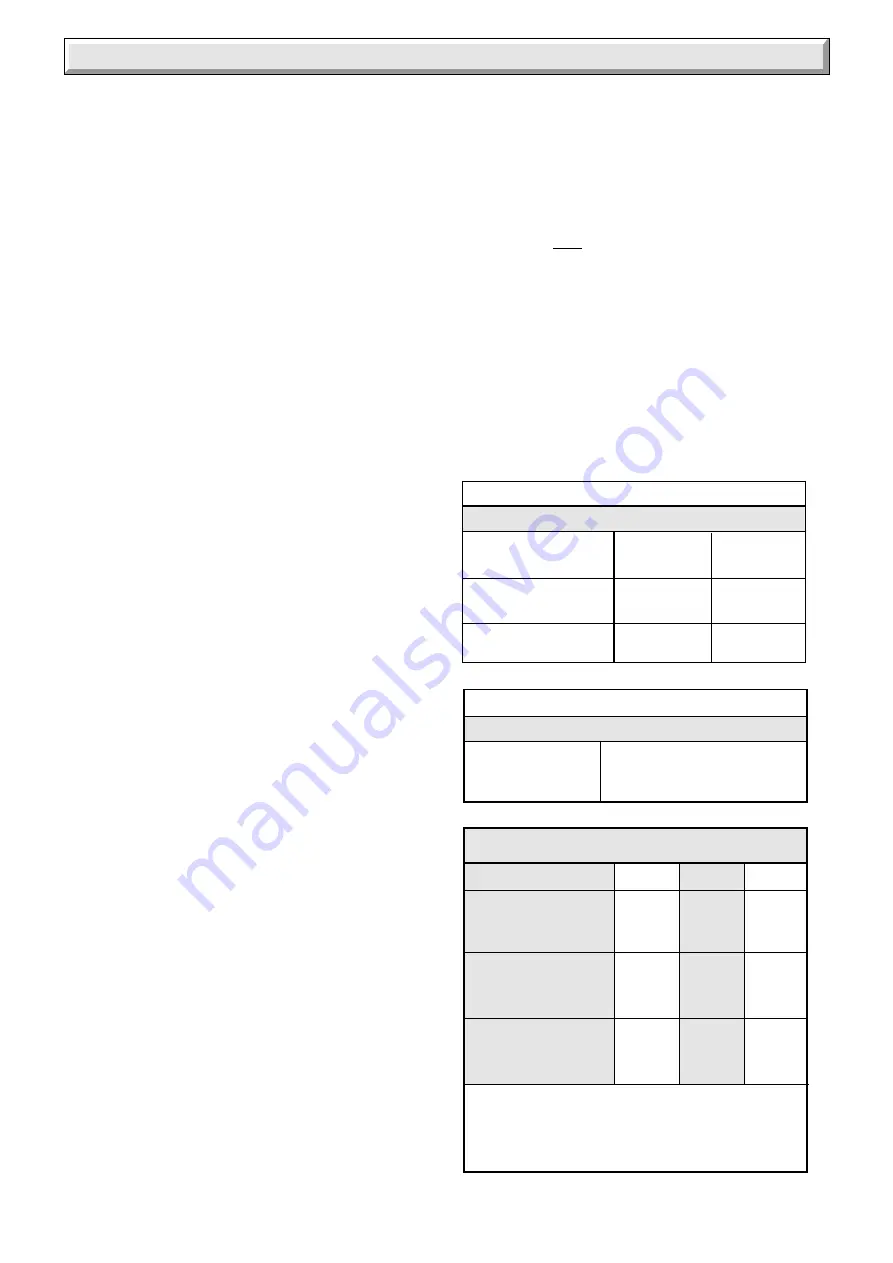
7
221462C
2 Flue and Ventilation
Important note
The boiler is fitted with a Flue Blockage Safety Device, which
will shut down the boiler if there is an unacceptable spillage of
products at the draught diverter.
This safety device MUST NOT under any circumstances be
interferred with or put out of action.
The safety device must only be replaced with the Glow-worm
parts.
2 Flue Connection
The integral draught diverter on the boiler makes the combustion
performance independent of the conditions in the secondary
flue, but in common with other fuels an efficient flue is necessary
to ensure a trouble free installation.
The flue outlet on the boiler is designed to take flue pipes to
BS567. If a flue pipe to BS715 is to be used an adapter must
be fitted to the boiler flue socket.
The flue must be in accordance with the current issue of
BS5440 Part 1.
Give maximum possible vertical rise from the boiler, at least a
minimum of 600mm, before any offset or bend. The use of 90
o
bends is not recommended.
An existing flue must be lined and end, at least above ridge
height, with a certificated terminal.
A chimney previously used for solid fuel must be swept and any
damper or register plate left in the locked open position or
removed.
2.1 Boilers in a Compartment
Where the installation of the boiler will be in an unusual location,
special procedures are necessary, the current issue of BS6798
gives detailed guidance on this aspect.
A compartment used to enclose the boiler must be designed
and constructed specifically for this purpose.
An existing cupboard or compartment modified for the purpose
may be used. Details of essential features of cupboard or
compartment design are given in the current issue of BS6798.
The doorway opening should be of sufficient size to allow for
easy removal of the boiler.
Where the boiler is fitted in a cupboard or compartment,
permanent high and low level ventilation must be provided.
The minimum ventilation areas required are given in Table “A”.
2.2 Boiler Installed in a Room or Space
A purpose designed ventilation opening must be provided on an
outside wall of the premises, refer to the current issue of
BS5440 Part 2 for further information.
The opening may be either, directly into the room or space
containing the boiler or into an adjacent room or space which
has an internal permanent air vent of the same size as the room
containing the boiler.
DO NOT ventilate through a private garage, bedroom, bedsitting
room or a room containing a bath or shower.
Air vents through a cavity wall must be ducted.
When the boiler is installed in a space already containing a fuel
burning appliance account must be taken of the TOTAL air
requirement.
2.3 Extract Fans
If an extract fan is fitted in the premises there is a possibility that
if adequate air openings are not provided spillage of products
from the boiler may occur.
When openings are fitted in accordance with the
recommendations of the current issue of BS5440 Part 1 and this
Section, extract fans should not cause spillage, but where such
an installation is found spillage tests as the current issue of
BS5440 Part 1 must be carried out.
The necessary action should then be taken.
See also Section 6.6.
Range Rating
Nominal
kW
Heat
Input
(GROSS)
Btu/h
14.73
16.60
18.46
50,250
56,600
63,000
min
medium
max
Burner
m bar
Setting
Pressure
in.w.g
Nominal
kW
Heat
Output
Btu/h
11.72
13.19
14.65
40,000
45,000
50,000
8.8
10.7
13.2
3.5
4.3
5.3
Table 1 ECONOMY PLUS 50C
Burner Injector Marking:
1.35
Burner Injector Size:
1.35 X 7
Pilot Injector Marking:
7218
TABLE "A" COMPARTMENT AIR VENTS
ECONOMY PLUS 50C
High Level
Vent Area
Low Level
Vent Area
Ventilation
Requirements
Air from room or
internal space
167cm
2
333cm
2
Air direct from
outside
83cm
2
167cm
2
ECONOMY PLUS 50C
TABLE "B" ROOM/SPACE AIR VENTS
Effective area
of vent
52cm
2