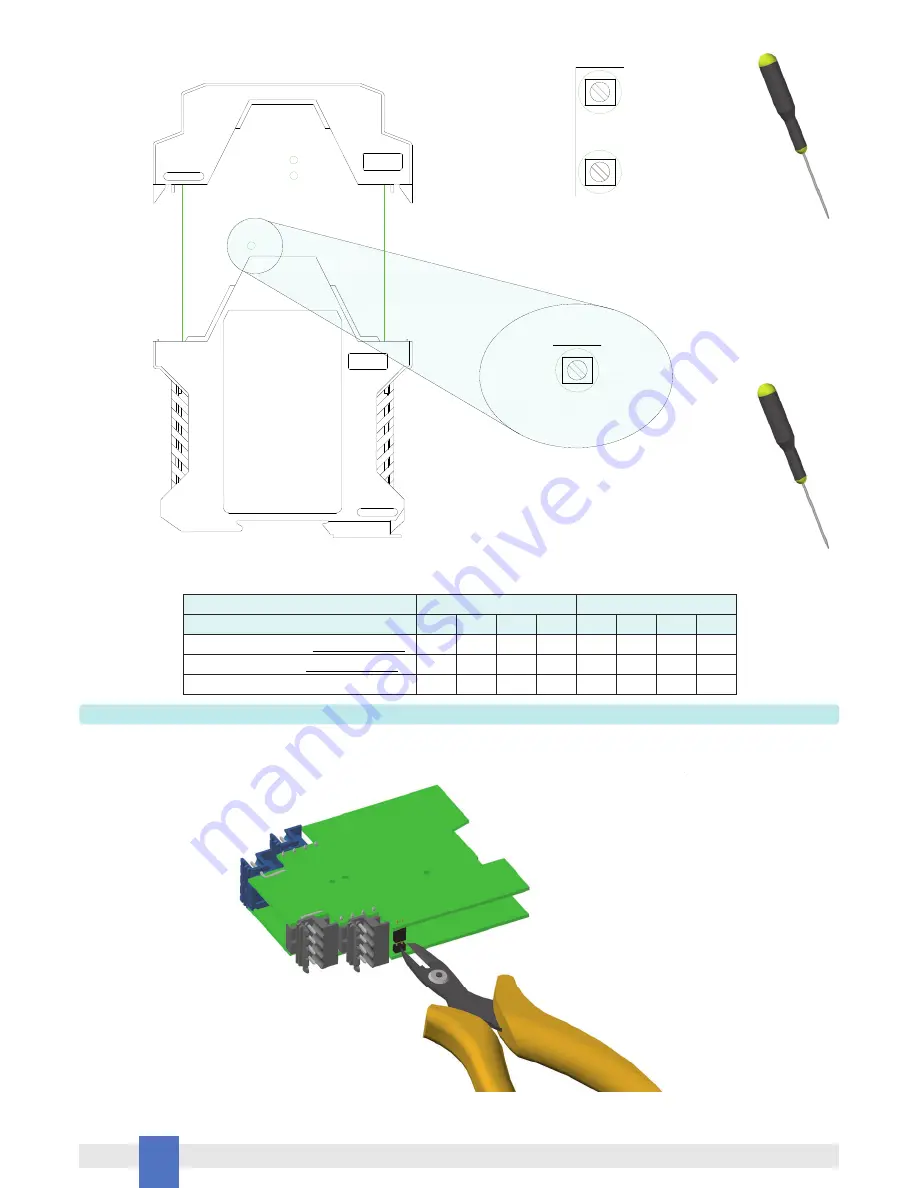
D1014
- SIL 2 Repeater Power Supply Hart compatible
G.M. International ISM0052-16
10
Side B Panel View
Calibration Trimmer Ch2
Span Trimmer
CH2
Zero Trimmer
CH2
Vtx Adjust Ch2
Screwdriver
for Trimmers
2 x 0.5 mm
Screwdriver
for Trimmers
1 x 0.5 mm
Terminal “3” and terminal “4” are internally connected to terminal “7” and terminal “8” for factory default. To supply the unit with different supply voltage or different power supply, open the
wiring between the terminals (see the following figure); consult factory for detailed information. When using Power Bus enclosure the power supply is the same for all channels there for
don’ t separate the terminals because one channel remains switched off.
Different power supply
Cut both pins of the connector to open the wiring between the terminals, using a wire cutter
Turn the trimmer clockwise to Increase Output
value or turn the trimmer counterclockwise if
you want to decrease Output value.
Turn the trimmer clockwise to
Increase Output value or turn
the trimmer counterclockwise
if you want to decrease Output
value.
Channel
Output Operation
4-20 mA Source Mode (for SIL application)
4-20 mA Sink Mode (for SIL application)
1-5 V (on 250
Ω
internal shunt)
Dip switch Configuration Summary Table
SW1
ON
OFF
ON
SW2 SW3 SW4
ON
OFF
OFF
OFF
OFF
ON
OFF
ON
ON
SW5
ON
OFF
ON
SW6 SW7 SW8
ON
OFF
OFF
OFF
OFF
ON
OFF
ON
ON
1
2