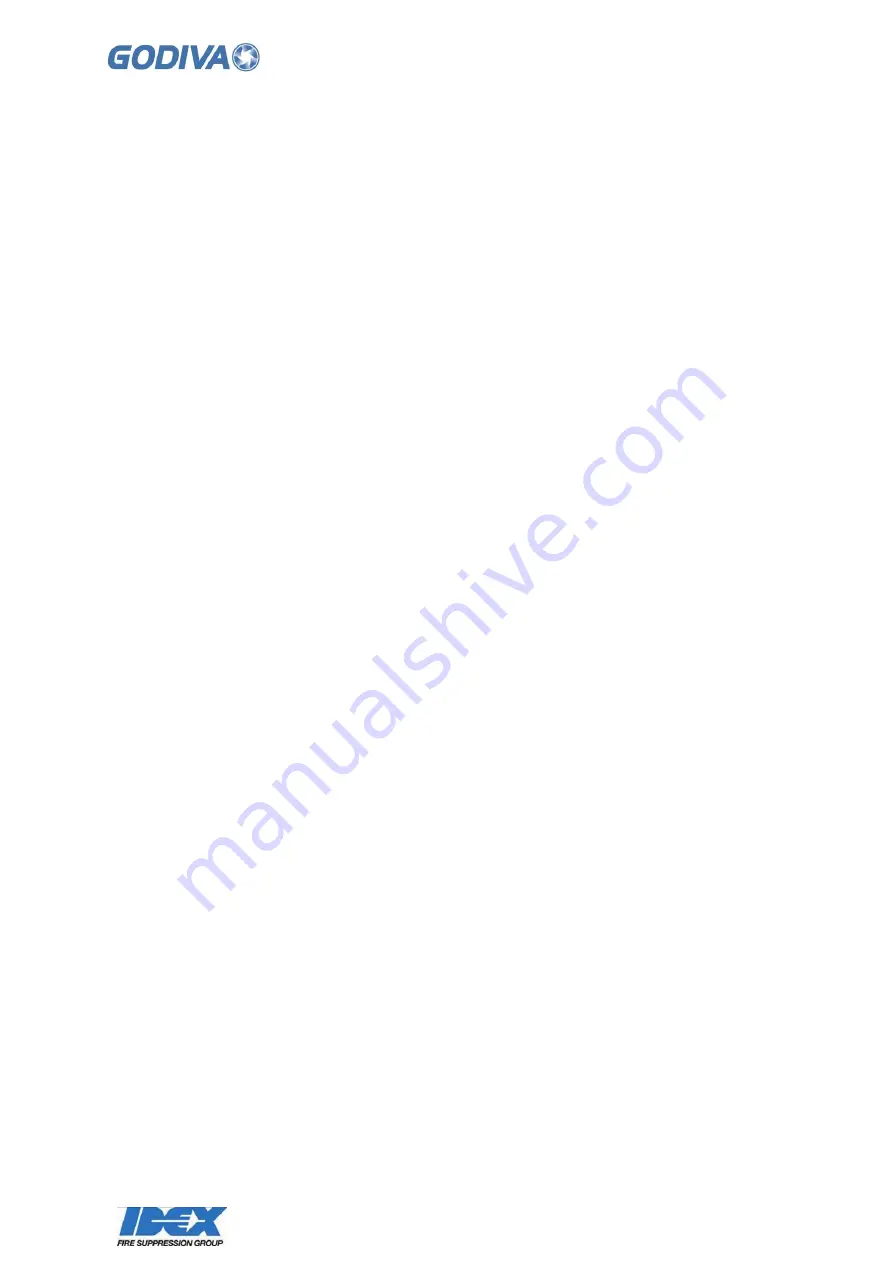
18
©Godiva Ltd. Our policy is one of continuous development. We therefore reserve the
right to amend specifications without notice or obligation.
SYSTEM OVERVIEW
The PC1_ or PC2_ is a Compressed Air Foam System comprising of three major
components (in addition to the main water pump)
– Air compressor, FoamLogix (foam
proportioning unit) and Manifold (foam mixing and control system).
The FoamLogix components (foam pump and motor assembly) are mounted separately
from the water pump and are designed to be remotely mounted according to the vehicle
builders requirements.
A metered amount of foam concentrate is introduced into the Manifold and mixed with
water from the pump discharge manifold to produce a solution. The foam and water
blend is then fed to a control valve (ARC) where wet or dry foam may be selected (air
ratio control section of manifold). Compressed air is then injected and the resulting foam
/ water / air combination is completely mixed by the X-mixers during discharge.
Safety interlocks are provided to ensure that:
1. Foam concentrate cannot be introduced unless water is flowing through the unit.
Compressed air cannot be introduced unless foam concentrate is flowing.
2.
‘Slugging’ (unmixed air and water) in the discharge line is prevented. Air cannot
be injected in the absence of foam and water.
3. Air injection when the foam tank is empty is prevented. Foam tank low level
switches are provided and MUST be fitted.
Compressor
There are two levels of compressor used
–
For Prima SmartCAFS50 systems
The rotary twin-screw compressor is rated at 50 scfm @ 7 bar
For Prima SmartCAFS100 systems
The rotary twin-screw compressor is rated at 100 scfm @ 7 bar
Both compressors are driven by a Polydrive belt. The compressor is engaged, or
disengaged from the pump drive, via an electro-magnetic clutch, which is activated by
the CAFS selector switch.
Compressor lubricating oil is cooled by water taken from the main pump, via the water
supply line; cooling water being supplied from pump delivery and returned to pump
suction. The compressor will reject approx. 8.0 kW (Tempest 3) / 22.0 kW (Tempest 6)
of heat energy to cooling. The installer must consider this additional thermal load.
When the compressor is stationary, residual system pressure is vented by a blow-down
valve.
NOTE:
The compressor should not be run without cooling water.