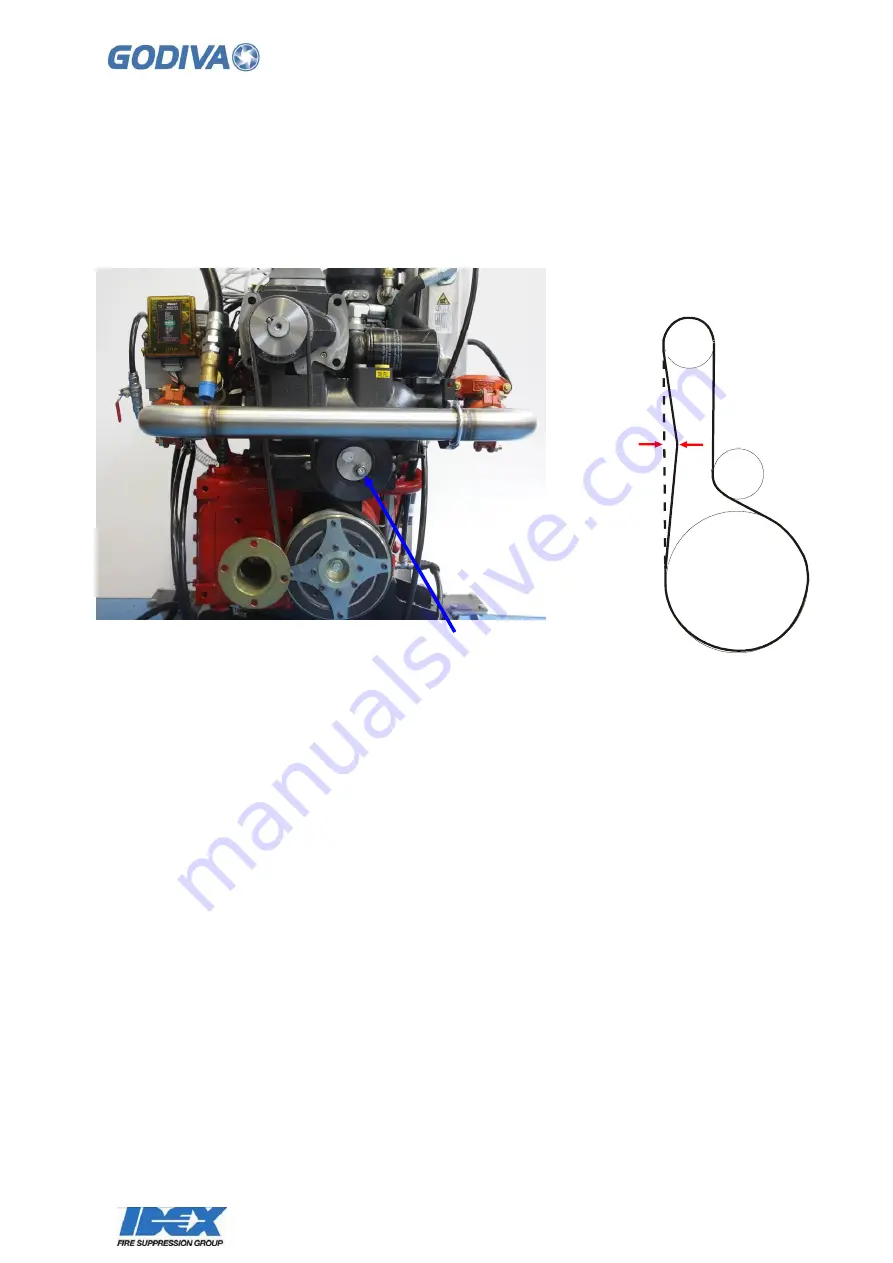
29
©Godiva Ltd. Our policy is one of continuous development. We therefore reserve the
right to amend specifications without notice or obligation.
Slacken this bolt, rotate
tensioner to achieve specified
deflection and secure
Compressor Drive Belt
– Prima SmartCAFS100
The compressor is driven by a
Poly V drive
belt, specification 9 PL 1270.
The installer must allow for access to adjust the jockey pulley belt tensioner. Tension
the belt to achieve an 5-7mm deflection with a 10kg load applied at mid span, see
diagram below.
Optical Belt Tension Meter
If an optical belt tension meter is available, e.g. the Clavis Optical Belt Tensioner, then
the belt can be tightened correctly by measuring the vibration frequency. Follow these
steps
–
1. Tighten the belt so it is reasonably taut.
2. Operate the optical belt tensioner according to the manufacturer’s instructions.
3. The device will register a frequency reading when the belt has been tapped. It is
recommended several readings are taken to obtain a representative figure.
4. For the Prima SmartCAFS100 belt the frequency setting must be 65 Hz.
5. If the measured frequency is too low, tighten the belt via the tensioner.
6. If the measured frequency is too high, loosen the belt via the tensioner.
7. Take another reading to confirm the frequency is 65 Hz.
5-7mm