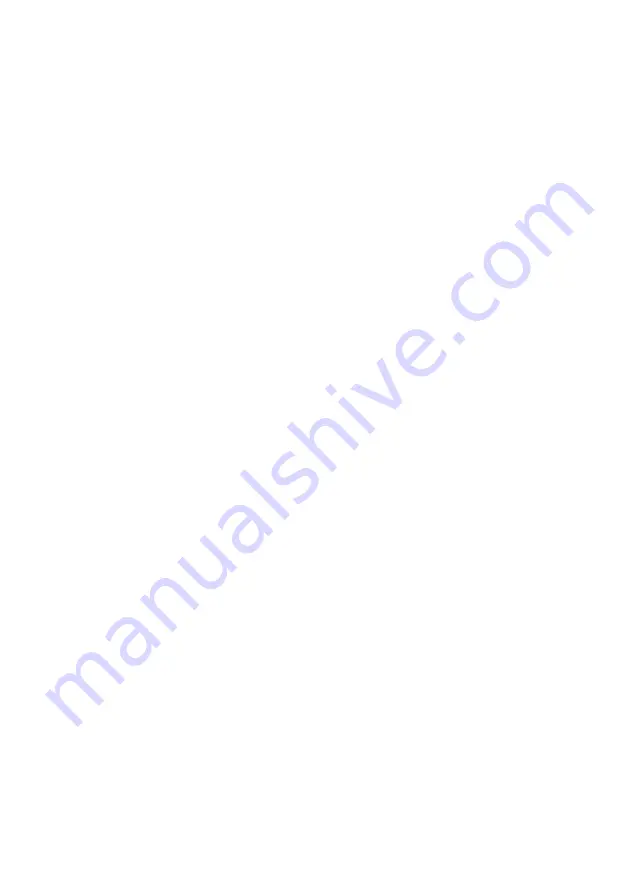
27
Diaphragm Pump
IMPORTANT:
Never overfill pump with oil as
damage to seals & oil bowl may result. Do not
operate diaphragm pumps above 540 RPM.
NOTE:
The pump will perform optimally
operating between 400 and 540 RPM. At lower
speeds excessive pulsation will occur, while
pump and diaphragm damage can result at
higher revs. Diaphragm pumps are a positive
displacement pump that utilises a number
of rubber diaphragms and non-return check
valves to pump (displace) the fluid. Diaphragm
pumps are fitted as standard equipment
on all Goldacres sprayers and are very well
suited to chemical spraying applications. To
ensure that you get the most from your pump,
using it correctly and carrying out periodic
maintenance are essential in obtaining the
best possible performance from your sprayer.
Please follow the following guidelines for safe
and efficient use:
1. When the pump is operating, the oil should
be visible in the bowl.
2. Whilst the pump is running, frequently
check the oil level and colour.
IMPORTANT:
A change in either colour or level
indicates probable damage to diaphragms or
valves.
Stop the pump immediately.
3. Inspect all hoses to make sure they are the
correct size, fitted securely and that there
is no restriction or leaking.
4. Do not start the pump with the pump
delivery under pressure.
5. Make sure that the pump PTO shaft cover
is fitted correctly to prevent accidental
injury.
6. Make sure the strainer in the suction filter
is clean and correctly installed.
7. Regularly lubricate the PTO shaft
according to recommendations (see “PTO
SHAFT”) to prevent the shaft from binding.
8. Always flush pump with clean water at
the end of each spraying day. Prolonged
chemical contact can severely damage
seals and diaphragms.
9. Regularly check the pump mounting bolts.
10. Change the pump oil after the first 50
hours of operation and then after every
300-350 hours. Be careful to use the
correct oil (use SAE 30W40 motor oil) and
do not overfill. Rotate pump manually (by
hand) to remove air locks when filling with
oil.
11. Do not leave water in pump if sprayer is
to be left in a cold environment. The water
may freeze and cause damage to pump
if pumping is attempted while water is
frozen. Empty pump of all water (run the
pump dry for 15-20 seconds) and cover
pump (i.e. with bag) to ensure this situation
does not arise. If this has not been done
and there is a possibility there may be
frozen water in the pump and/or in the
lines, wait until any ice has completely
thawed before using pump.
NOTE:
Ensure that the pump can be turned
over by hand before starting.
Pump Diaphragms
The pump diaphragms are wearing
components that need to be replaced during
the life of the pump. Life expectancy depends
upon the operation and maintenance and its
suitability for the task.
• Pump diaphragms should be replaced
prior to diaphragm failure.
• For large operations, where the sprayer
is used extensively, the pump should be
reconditioned once a season, including
replacing diaphragms, seals and valve
springs.
• It is recommended to keep a spare pump
repair kit (including diaphragms, seals,
valve o-rings and springs) on hand in
case of a breakdown. The main causes of
premature diaphragm failure are:
• Blocked or incorrectly fitted suction filter
restricting flow to the pump.
• Incorrect air damper chamber pressure.
• Running pump at speeds greater than 540
RPM.
• Exceeding the pressure limit of the pump.
• Failure to wash chemicals from pump after
use.
• Incompatibility of the diaphragm material
and the chemicals used.