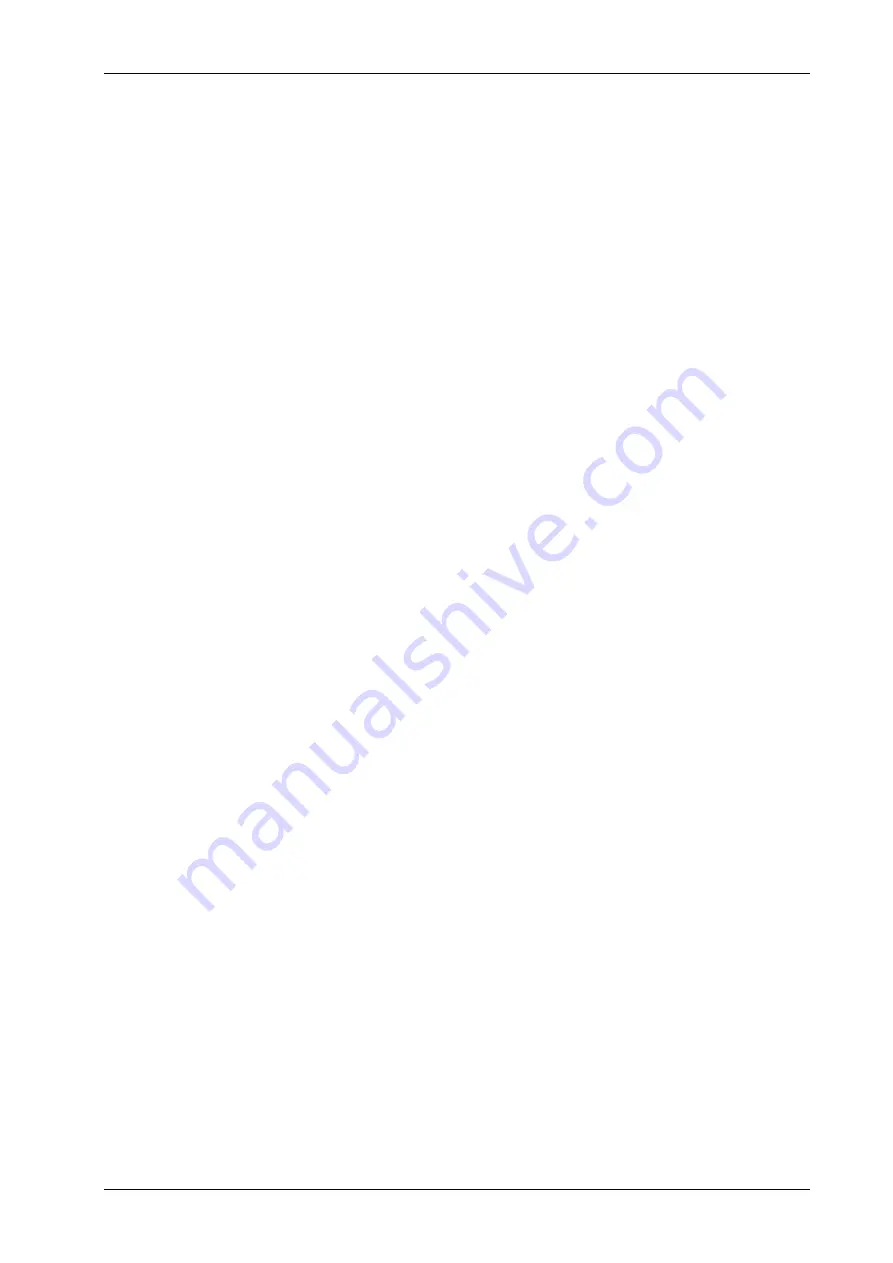
F870S
1 Operation instruction for explosion protected device
Page 4
Gönnheimer Elektronic GmbH
Tel.: +49 (6321) 49919-0
Fax: +49 (6321) 49919-41
1
Operation instruction for Explosion protected device
Application and Standards
This instruction manual applies to explosion-protected devices of types below. This apparatus is
only to be used as defined and meets requirements of EN 60 079 particularly EN60 079-14
"electrical apparatus for potentiality explosive atmospheres".
Use this manual in hazardous locations, which are hazardous due to gases and vapors accord-
ing to the explosion group and temperature class as stipulated on the type label. When installing
and operating the explosion protected distribution and control panels you should observe the
respective nationally valid regulations and requirements.
General Instructions
Work on electrical installations and apparatus in operation is generally forbidden in hazardous
locations, with the exception of intrinsically safe circuits. In special cases work can be done on
non-intrinsically safe circuits, on the condition that during the duration of such work no explosive
atmosphere exists.
Only explosion protected certified measuring instruments may be used to ensure that the appa-
ratus is voltage-free. Grounding and short-circuiting may only be carried out, if there is no ex-
plosion hazard at the grounding or short circuit connection.
To achieve an impeccable and safety device operation, please take care for adept transporta-
tion, storage and mounting, as well as accurate service and maintenance. Operation of this de-
vice should only be implemented by authorized persons and in strict accordance with local safe-
ty standards.
The electrical data on the type label and if applicable, the "special conditions" of the test certifi-
cate BVS 10 ATEX E 112are to be observed.
For outdoor installation it is recommended to protect the explosion protected distribution and
control panel against direct climatic influence, e.g. with a protective roof. The maximum ambient
temperature is 40°C, if not stipulated otherwise.
Terminal compartment in Increased Safety
When closing, it is to be ensured that the gaskets of the terminal compartment remain effective,
thus maintaining degree of protection IP 54 according to EN 60529. Close unused entries by
impact-proof stopping plugs, which are secured against self-loosening and turning.
Do not open the device in Ex area, as long the device is energized.
Inside area with explosive dust do clean the inner of the housing of the dust before closing the
housing.
Maintenance Work
The gaskets of Ex e enclosures are to be checked for damages and replaced, if required. Ter-
minals, especially in the Ex e chamber are to be tightened. Possible changes in color point to
increased temperature. Cable glands, stopping plugs and flanges are to be tested for tightness
and secure fitting.
Intrinsically Safe Circuits
Erection instructions in the testing certificates of intrinsically safe apparatus are to be observed.
The electrical safety values stipulated on the type label must not be exceeded in the intrinsically
safe circuit. When interconnecting intrinsically safe circuits it is to be tested, whether a voltage
and/or current addition occurs. The intrinsic safety of interconnected circuits is to be ensured.
(EN 60079-14, section 12)
Summary of Contents for F870S
Page 1: ...User s manual Pressurized enclosure system F870S Manual_F870S_v1 0 2_2016 doc...
Page 34: ......
Page 35: ......
Page 36: ......
Page 37: ......
Page 38: ......
Page 39: ......
Page 40: ......
Page 41: ......
Page 42: ......
Page 43: ......
Page 44: ......
Page 45: ......
Page 46: ......
Page 47: ......