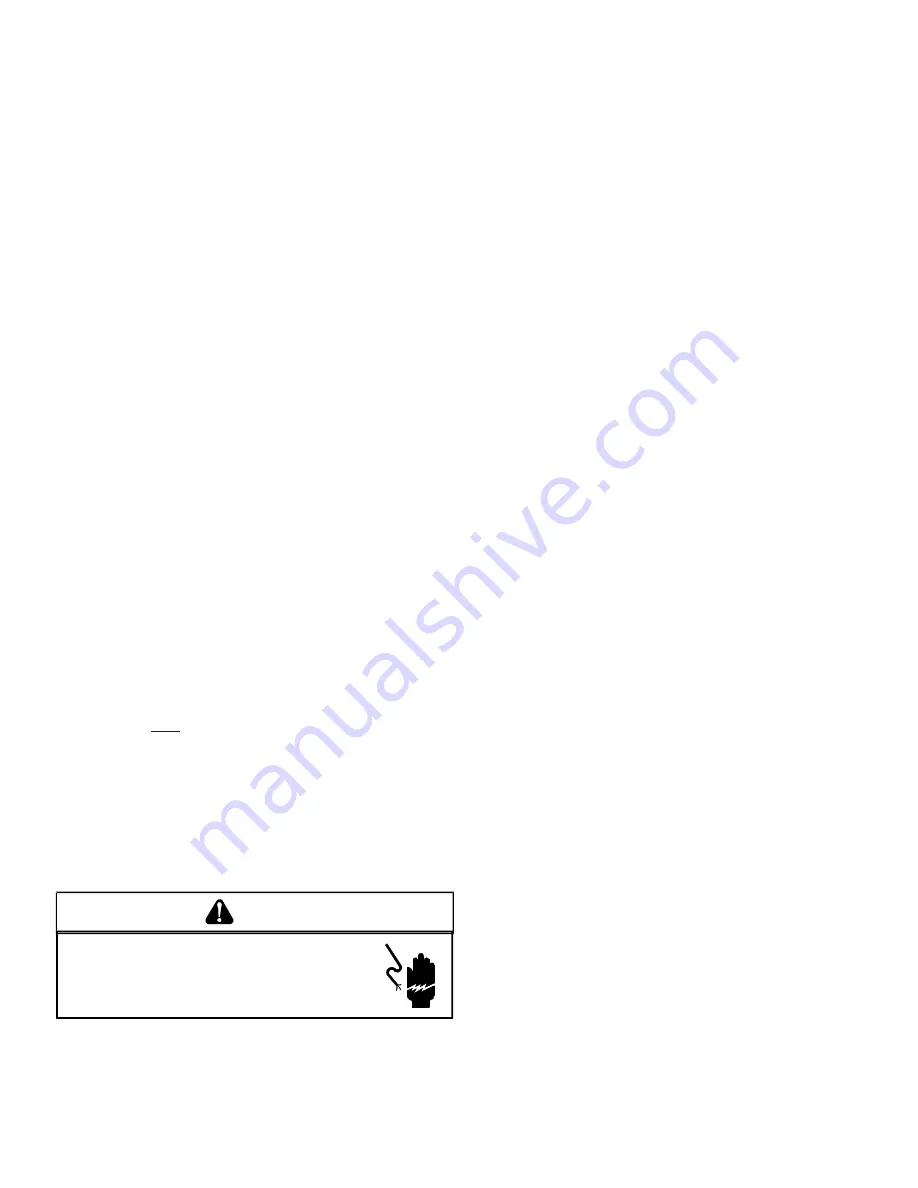
13
R
EFRIGERATION
S
YSTEM
C
HECKS
Ensure the hold-down bolts on the compressor are secure
and have not vibrated loose during shipment. Check that vi-
bration grommets have been installed. Visually check all pip-
ing and clamps. The entire refrigeration system has been
factory charged and tested, making it unnecessary to field
charge. Factory charges are shown in Appendix C and on
the unit nameplate.
Install service manifold hoses. Gauges should read satura-
tion pressure corresponding to ambient temperature. Charge
should be checked to obtain 12° to 15° of sub-cooling per
system (i.e. compressor circuits).
S
TART
-U
P
P
ROCEDURE
AND
C
HECKLIST
Begin with power turned off at all disconnects.
1. Turn thermostat system switch to “Cool,” and fan
switch to “Auto” and turn temperature setting as high
as it will go.
2. Inspect all registers and set them to the normal open
position.
3. Turn on the electrical supply at the disconnect.
4. Turn the fan switch to the “ON” position. The blower
should operate after a 7-second delay.
5. Turn the fan switch to “Auto” position. The blower
should stop after a 65 second delay.
6. Slowly lower the cooling temperature until first stage
COOL (LOW COOL) starts. The blower, both fans,
and first stage compressor should now be operating.
Allow the unit to run 10 minutes, make sure cool air is
being supplied by the unit.
7. Lower the cooling temperature further until second
stage COOL (HIGH COOL) starts. The blower, both
fans, and both compressors should now be operating.
Allow the unit to run 10 minutes, make sure cool air is
being supplied by the unit.
8. Turn the temperature setting to the highest position,
stopping the unit. The indoor blower will continue to
run for 65 seconds.
9. Turn the thermostat system switch to “OFF” and
disconnect all power when servicing the unit.
HIGH VOLTAGE!
D
ISCONNECT
ALL
POWER
BEFORE
SERVICING
OR
INSTALLING
THIS
UNIT
. M
ULTIPLE
POWER
SOURCES
MAY
BE
PRESENT
. F
AILURE
TO
DO
SO
MAY
CAUSE
PROPERTY
DAMAGE
,
PERSONAL
INJURY
OR
DEATH
.
WARNING
F
INAL
S
YSTEM
C
HECKS
10. Check to see if all supply and return air grilles are
adjusted and the air distribution system is balanced
for the best compromise between heating and cooling.
11. Check for air leaks in the ductwork. See Sections on
Air Flow Adjustments.
12. Make sure the unit is free of “rattles”, and the tubing
in the unit is free from excessive vibration. Also make
sure tubes or lines are not rubbing against each other
or sheet metal surfaces or edges. If so, correct the
trouble.
13. Set the thermostat at the appropriate setting for
cooling and heating or automatic change over for
normal use.
14. Be sure the Owner is instructed on the unit operation,
filter, servicing, correct thermostat operation, etc.
R
EFRIGERATION
P
ERFORMANCE
C
HECK
Under normal summertime (full load) operating conditions,
superheat should be between 8°F and 12°F and sub-cooling
measured at the condenser outlet should be 15°F (nominal).
A 25°F to 35°F temperature difference should exist between
the entering condenser air and the temperature correspond-
ing to the compressor saturated discharge pressure. Check
that compressor RLA corresponds to values shown in Ap-
pendix C. RLA draw can be much lower than values listed at
low load conditions and low ambient condensing tempera-
tures. Values in Appendix C can slightly exceed at high load
conditions and high ambient condensing temperatures.
AIR FLOW ADJUSTMENTS
The drive on the supply fan is typically set in the middle of the
RPM range. The drive motor sheave pitch diameter is field
adjustable for the required airflow. Refer to “Drive
Adjustments” section below.
When the final adjustments are complete, the current draw
of the motor should be checked and compared to the full
load current rating of the motor. The amperage must not ex-
ceed the service factor stamped on the motor nameplate.
The total airflow must not be less than that required for op-
eration of the electric heaters or the furnace.
If an economizer is installed, check the unit operating bal-
ance with the economizer at full outside air and at minimum
outside air. Upon completion of the air flow balancing, we
recommend replacing the variable pitched motor sheave with
a properly-sized fixed sheave. A matching fixed sheave will
provide longer belt and bearing life and vibration free opera-
tion. Initially, it is best to have a variable pitched motor sheave
for the purpose of airflow balancing, but once the balance
has been achieved, fixed sheaves maintain alignment and
minimize vibration more effectively. For direct drive units, move
green wire for fan.
NOTE:
Never run CFM below 350 CFM per ton, evaporator
freezing or poor unit performance is possible.