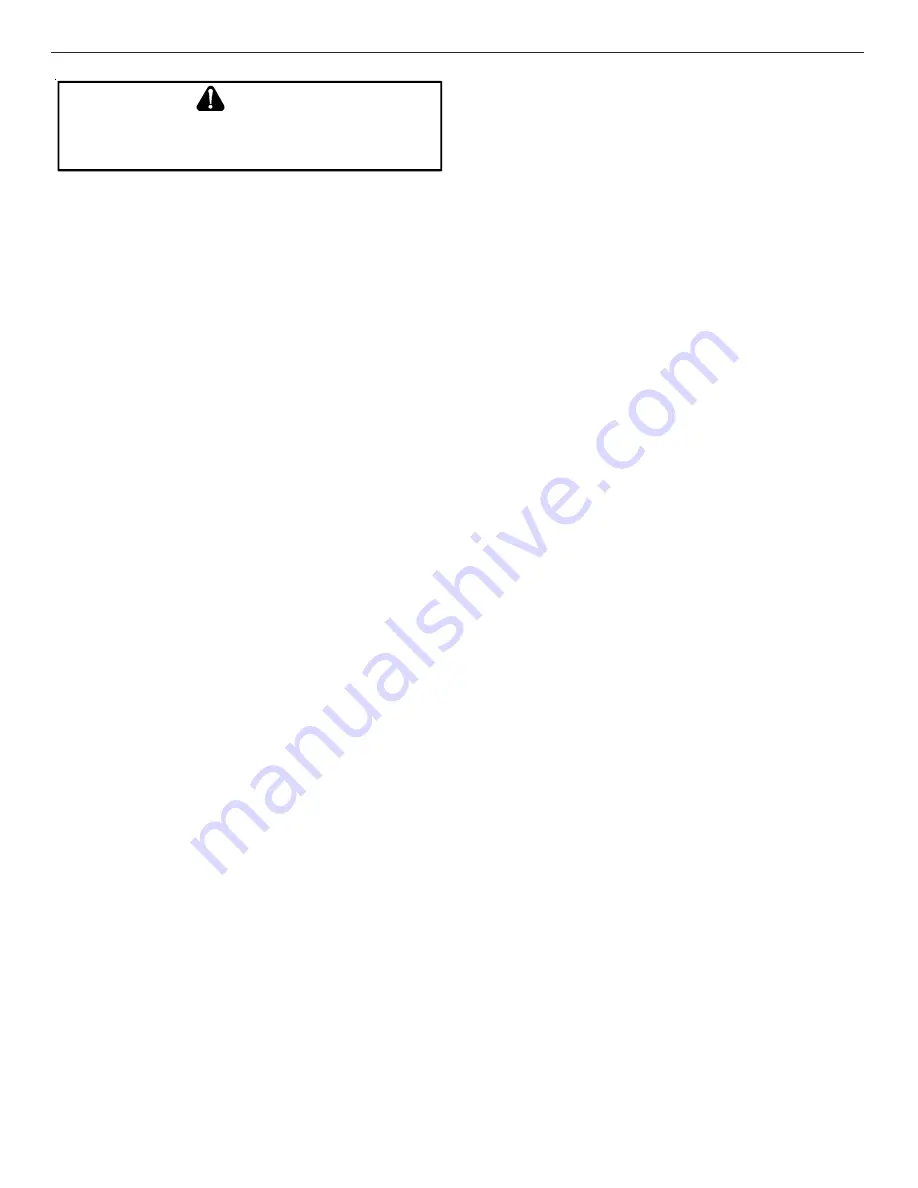
7
T
O
PREVENT
PROPERTY
DAMAGE
,
PERSONAL
INJURY
OR
DEATH
DUE
TO
FIRE
,
DO
NOT
INSTALL
THIS
FURNACE
IN
A
MOBILE
HOME
,
TRAILER
,
OR
RECREATIONAL
VEHICLE
.
WARNING
P
RODUCT
D
ESCRIPTION
F
EATURES
This furnace is a part of the ComfortNet™ family of products. The
CTK0*AA thermostat kit allows this furnace to be installed as part
of a digitally communicating system. The ComfortNet system pro-
vides automatic airflow configuration, enhanced setup features,
and enhanced diagnostics. It also reduces the number of thermo-
stat wires to a maximum of four. It may be also installed as part of
a non-communicating system using a standard 24 VAC thermo-
stat.
This product may be installed with the ComfortNet thermostat and
a non-ComfortNet compatible single stage air conditioning unit.
However, this reduces the benefits of the ComfortNet system as
the enhancements will only apply to the furnace.
The modulating furnace operation is based off of negative pres-
sure created by the the draft inducer. The Integrated Furnace
Control (IFC) receives commands from the room thermostat.
The IFC then controls the RPM of the (3 phase) inducer by
varying the frequency and voltage to the inducer. This is known
as variable frequency drive (VFD). The inducer, pressure
switches, and gas valve are linked by pneumatic tubing. The
gas valve modulates based on this negative pressure.
P
RODUCT
A
PPLICATION
This furnace is primarily designed for residential home-heating ap-
plications. It is NOT designed or certified for use in mobile homes,
trailers or recreational vehicles. Neither is it designed or certified
for outdoor applications. The furnace
must
be installed indoors
(i.e., attic space, crawl space, or garage area provided the garage
area is enclosed with an operating door).
This furnace can be used in the following non-industrial commer-
cial applications:
Schools, Office buildings, Churches, Retail stores,
Nursing homes, Hotels/motels, Common or office areas
In such applications, the furnace must be installed with the follow-
ing stipulations:
•
It must be installed per the installation instructions
provided and per local and national codes.
•
It must be installed indoors in a building constructed on
site.
•
It must be part of a ducted system and not used in a free
air delivery application.
•
It must not be used as a “make-up” air unit.
•
It must be installed with two-pipe systems for combustion
air, especially if VOC’s or other contaminants are present
in the conditioned space.
•
All other warranty exclusions and restrictions apply This
furnace is an ETL dual-certified appliance and is
appropriate for use with natural or propane gas (
NOTE:
If
using propane, a propane conversion kit is required).
Dual certification means that the combustion air inlet pipe is op-
tional and the furnace can be vented as a:
Non-direct vent (single pipe) central forced air furnace in
which combustion air is taken from the installation area
or from air ducted from the outside or,
Direct vent (dual pipe) central forced air furnace in which
all combustion air supplied directly to the furnace burners
through a special air intake system outlined in these
instructions.
This furnace may be used as a construction site heater
ONLY
if
all of the following conditions are met:
•
The vent system is permanently installed per these
installation instructions.
•
A room thermostat is used to control the furnace. Fixed
jumpers that provide continuous heating CANNOT be
used and can cause long term equipment damage.
•
Return air ducts are provided and sealed to the furnace.
•
A return air temperature range between 60ºF (16ºC) and
80ºF (27ºC) is maintained.
•
Air filters are installed in the system and maintained during
construction replaced as appropriate during construction,
and upon completion of construction.
•
The input rate and temperature rise are set per the furnace
rating plate.
•
100% outside air is provided for combustion air
requirements during construction. Temporary ducting can
be used.
NOTE:
Do not connect the temporary duct directly to the
furnace. The duct must be sized for adequate combustion
and ventilation in accordance with the latest edition of
the National Fuel Gas Code NFPA 54/ANSI Z223.1 or
CAN/CSA B149.1 Installation Codes
.
•
The furnace heat exchanger, components, duct system,
air filters and evaporator coils are thoroughly cleaned
following final construction clean up.