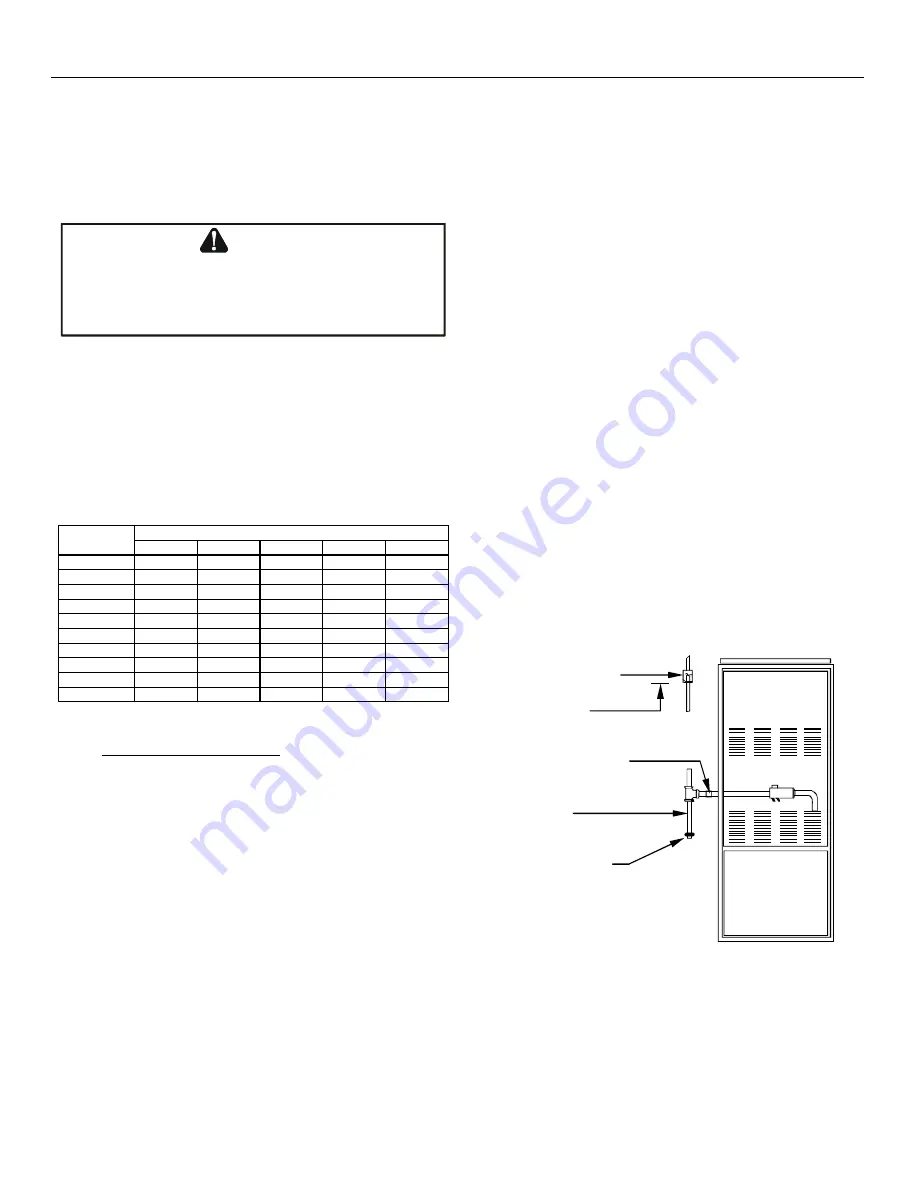
20
G
AS
S
UPPLY
AND
P
IPING
Contact your distributor for a tabular listing of appropriate
manufacturer’s kits for propane gas and/or high altitude instal-
lations. The indicated kits must be used to insure safe and
proper furnace operation. All conversions must be performed
by a qualified installer, or service agency.
G
AS
P
IPING
C
ONNECTIONS
T
O
AVOID
POSSIBLE
UNSATISFACTORY
OPERATION
PMENT
,
USE
THE
PROPER
SIZE
OF
NATURAL
/
PROPANE
GAS
PIPING
NEEDED
WHEN
RUNNING
PIPE
FROM
THE
METER
/
TANK
TO
THE
FURNACE
.
OR
EQUIPMENT
DAMAGE
DUE
TO
UNDERFIRING
OF
EQUI
WARNING
When sizing a trunk line, be sure to include all appliances
which will operate simultaneously.
The gas piping supplying the furnace must be properly sized
based on the gas flow required, specific gravity of the gas, and
length of the run. The gas line installation must comply with
local codes, or in their absence, with the latest edition of the
National Fuel Gas Code, NFPA 54/ANSI Z223.1.
Natural Gas Capacity of Pipe
In Cubic Feet of Gas Per Hour (CFH)
Length of
Nominal Black Pipe Size
Pipe in Feet
1/2"
3/4"
1"
1 1/4"
1 1/2"
10
132
278
520
1050
1600
20
92
190
350
730
1100
30
73
152
285
590
980
40
63
130
245
500
760
50
56
115
215
440
670
60
50
105
195
400
610
70
46
96
180
370
560
80
43
90
170
350
530
90
40
84
160
320
490
100
38
79
150
305
460
(Pressure 0.5 psig or less and pressure drop of 0.3" W.C.; Based on
0.60 Specific Gravity Gas)
CFH = BTUH Furnace Input
Heating Value of Gas (BTU/Cubic Foot)
To connect the furnace to the building’s gas piping, the installer
must supply a ground joint union, drip leg, manual shutoff valve,
and line and fittings to connect to gas valve. In some cases,
the installer may also need to supply a transition piece from 1/
2" pipe to a larger pipe size.
The following stipulations apply when connecting gas piping.
•
Use black iron or steel pipe and fittings for the building
piping.
•
Use pipe joint compound on male threads only. Pipe
joint compound must be resistant to the action of the
fuel used.
•
Use ground joint unions.
•
Install a drip leg to trap dirt and moisture before it can
enter the gas valve. The drip leg must be a minimum
of three inches long.
•
Install a 1/8" NPT pipe plug fitting, accessible for test
gage connection, immediately upstream of the gas
supply connection to the furnace.
•
Use two pipe wrenches when making connection to
the gas valve to keep it from turning. The orientation
of the gas valve on the manifold must be maintained
as shipped from the factory.
•
Install a manual shutoff valve between the gas meter
and unit within six feet of the unit. If a union is installed,
the union must be downstream of the manual shutoff
valve, between the shutoff valve and the furnace.
•
Tighten all joints securely.
•
Connect the furnace to the building piping by one of
the following methods:
–
Rigid metallic pipe and fittings.
–
Semi-rigid metallic tubing and metallic fittings.
Aluminum alloy tubing must not be used in exterior
locations.
–
Use listed gas appliance connectors in accordance
with their instructions. Connectors must be fully in
the same room as the furnace.
–
Protect connectors and semi-rigid tubing against
physical and thermal damage when installed.
Ensure aluminum-alloy tubing and connectors are
coated to protect against external corrosion when
in contact with masonry, plaster, or insulation, or
subjected to repeated wetting by liquids such as
water (except rain water), detergents, or sewage.
Drip Leg
Ground Joint Pipe Union
To Be Installed Ahead of
Gas Valve
Reducing Coupling
1/2” x 1/8” with 1/8”
Pipe Plug to Measure
Line Gas Pressure
Height Required
By Local Code
Location of Manual Valve
(Installed Ahead of
Ground Joint Pipe Union)
``
General Furnace Layout
U
PFLOW
I
NSTALLATIONS
When the gas piping enters through the right side of the fur-
nace
, the installer must supply the following fittings (starting
from the gas valve):
•
90 degree elbows (2).
•
Close nipple.
•
Straight pipe to reach the exterior of the furnace .