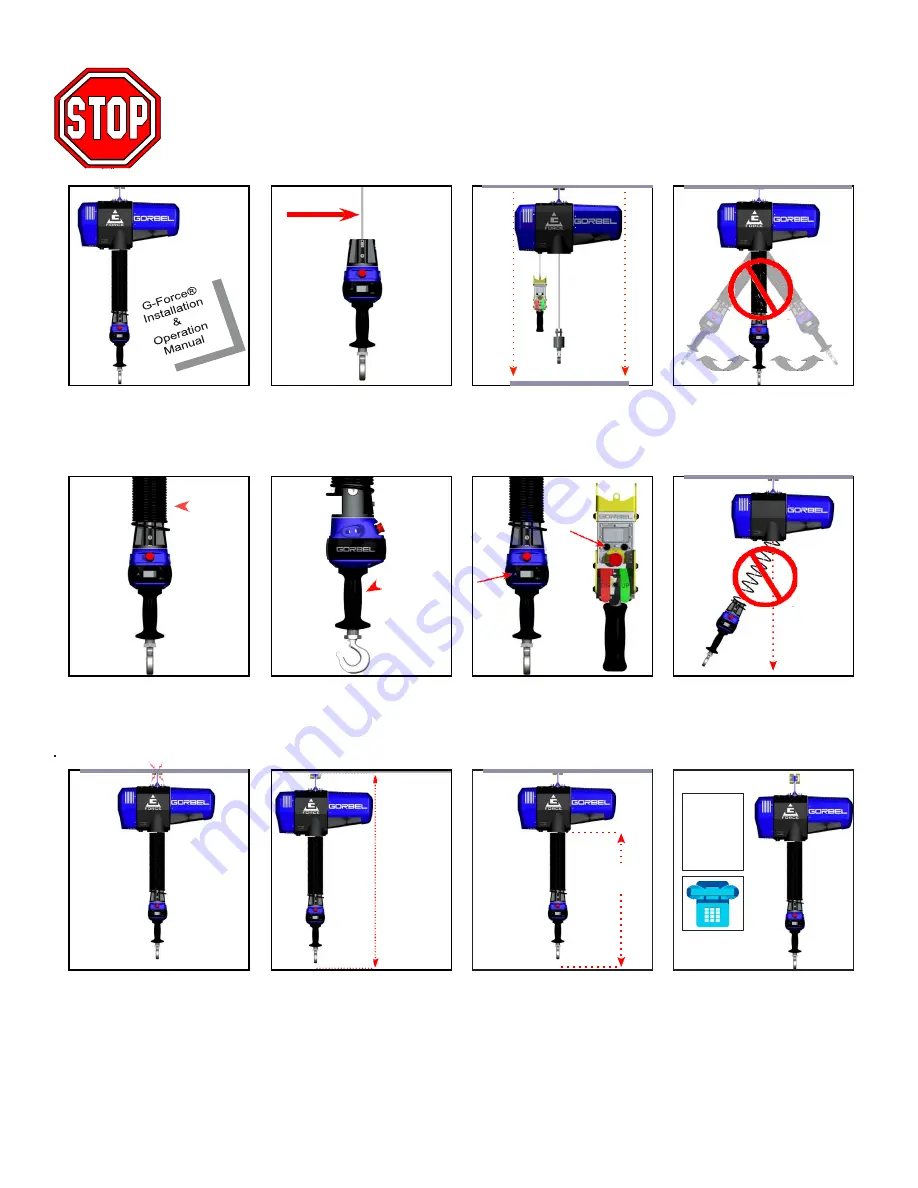
G-FORCE
®
OPERATIONAL GUIDELINES
All operators should read the G-Force® Installation and Operation Manual before
operating the unit. Please follow the instructions contained in this manual for your
safety and the optimum trouble-free operation of your G-Force®.
0
Maximum
Trolley Saddle is
Read and follow all
instructions and warning
information on or attached
to the G-Force®.
Check Wire Rope for
improper seating, twisting,
kinking, wear or defects
before operating.
Center G-Force® over the
load before lifting a load.
Do not end or side load.
Avoid swinging of load or
load hook when traveling
with the G-Force®.
Check the coil cord for
improper seating, twisting,
kinking, wear or defects
before operating.
The operator’s hand should
not leave the handle grip at
any time the G-Force® is in
use (excluding Float Mode).
Float Mode – press the
G-Force® button with only the
load weight hanging from the
unit. Applying additional force
will cause unit to drift.
The wire rope should never be
>15
°
out of vertical while the
G-Force® is in use. The G360
must be level at all times.
Do not impact the
G-Force® into end stops
repeatedly or at a speed
faster than a normal
walking pace.
Maximum Trolley Saddle or
the G-Force® with standard
in-line slide handle is 14’.
What is
Trolley
Saddle?
The
distance
from
bottom of
wheels to
floor.
Questions about G-Force®?
Call your local Gorbel®
distributor or Gorbel®
Customer Service at
(800) 821-0086.
The maximum available
wire rope travel for the
G-Force® is 11’.
For H5 duty cycle, the
maximum working stroke
is 8’.
11’
?
4