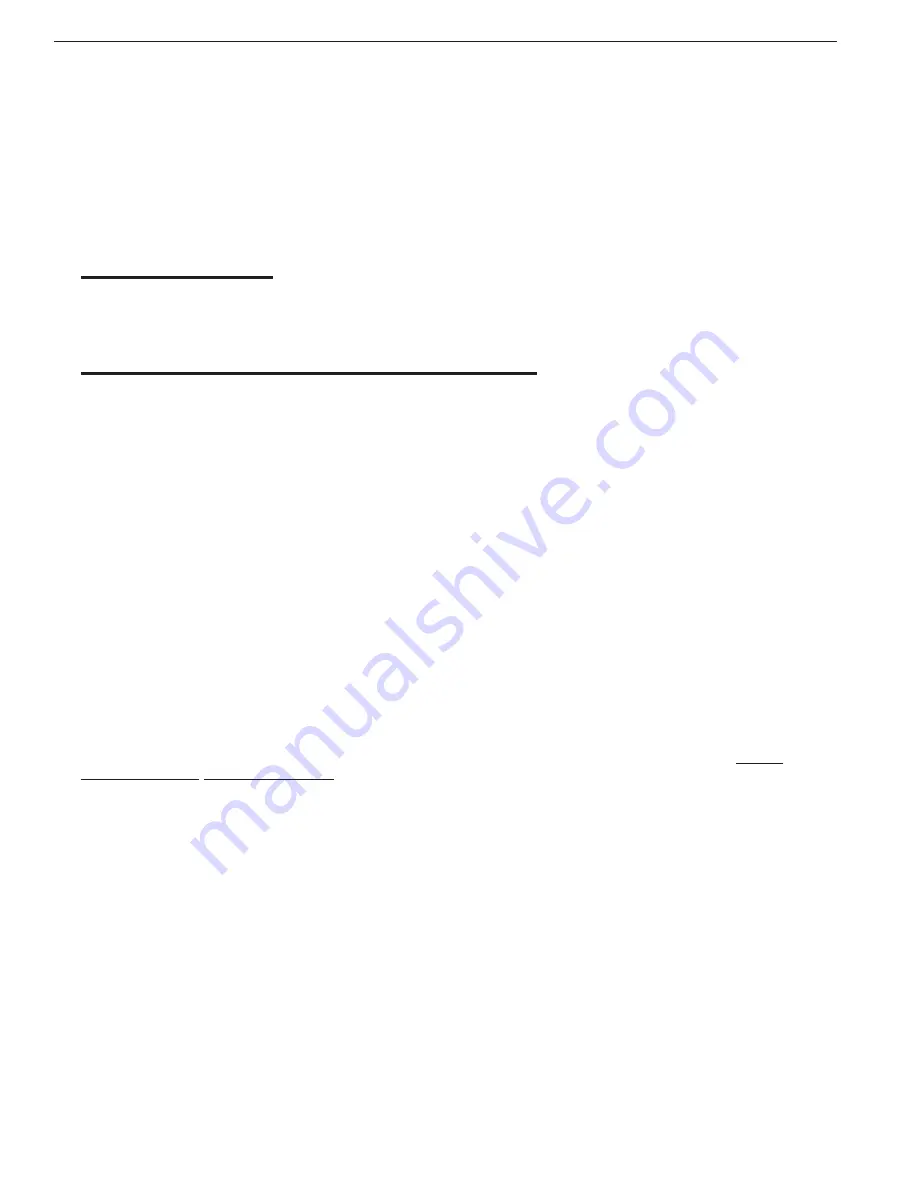
Error #32011, 32189 & 6015 – COMMUNICATION_FAILURE
Description:
Communication is faulty on the G-Force®.
Reaction:
Lift is shut down for all drive faults or warnings.
Cause / Remedy:
On a powered down unit:
(a)
Verify all external and internal cabling is making contact and no wires are pinched, abraded or broken.
(b)
Inspect the G360® slipring swivel assembly. Clean and lubricate slipring (Deoxit) or replace if warn excessive-
ly.
(c)
Please contact Gorbel® After the Sales Service at 800-821-0086 or 585-924-6262.
C Command Warnings
Error #10000 - WARNING_LIFT
Description:
Starting index to non-critical warnings.
C.1. Command Warnings - Process and Display Mode
Error #10404 - WARN_PROG_ERROR_LOADCELL_COEF
Description:
This warning is generated when system attempts to program the load cell coe
ffi
cient, as com-
manded through PROGRAM MODE \ CONFIGUR MENU \ CALIBRAT LOD COEF and resulted in an invalid set-
ting number.
Reaction:
Handle OLED displays the warning while unit is allowed to continue to run. The invalid
coe
ffi
cient is cleared and all previously programmed weights for Q2 and iQ2 features are reset.
Cause / Remedy:
Load cell calibration procedure composed of three steps: (1) zero the empty handle and any
clevis or hook), (2) pick up a maximum capacity and set the load cell coe
ffi
cient, and (3) set unit in slack and set
a true zero weight. This error is generated when performing (2). The possible causes can be:
(a) Step (1) is not correctly performed with an empty handle.
(b) The pickup weight does not match the rated capacity.
(c) The programming sequences are not followed correctly.
(d) Problem with the load cell electronics. This may include a damaged load cell, loose load cell ca-
ble connection to the actuator main interface board or to the servo drive.
Error #10405 - WARN_PROG_OVER_RANGE_LOADCELL_BIAS
Description:
The sampled minimum load cell signal (bias) is greater than the acceptable range from the nor-
mal bias value for this unit. The acceptable range of this parameter is empirically determined and selected for
di
ff
erent models and capacities.
Reaction:
Handle OLED displays the warning while unit is allowed to continue to run. The over-
range warning indicates the potential error in programming the parameter without altering the value.
The sample value is still retained.
Cause / Remedy:
The load cell minimum signal (bias) is sampled during procedure steps (1) and (3) (see
Warning #10404). However, the normal bias value selected is based on step (3), when the unit is in slack.
Therefore, if a handle, tooling, or additional parts are tare in step (1), this warning will be triggered. Ignore
this warning if it is triggered in step (1). If this warning is triggered while the unit should be in slack, the pos-
sible causes can be:
(a) The unit may appear to be in slack while the load plate is still exerting pressure on the load cell. This
may be due to some binding or drag in the rotary geartrain mechanism. Ensure the unit is in slack such
that the rotary geartrain mechanism is pushed back (i.e. push up onto the white plastic wear ring at the
bottom of the unit) and the unit cannot move down with a handle controller.
(b) The metal mounting bracket of the white plastic wear ring may be bent such that the wear ring cannot
move back far enough and is touching the cast housing opening prematurely. When the unit is loaded,
the wear ring should be situated near the center of the circular opening without contact. The bracket
may be bent back if it is o
ff
set near a particular side signi
fi
cantly. Readjust the bracket or replace it.
(c) Problem with the load cell electronics. This may include a damaged load cell or loose load cell cable
connection to the actuator main interface board or to the servo drive.
(d) The actuator PCB board which processes the load cell signal may be damaged or out of spec. Replace
the PCB board.
G-Force® & Easy Arm Q2 - iQ2 Service Manual
Gorbel Inc.
Revised 5/21
6 - 15