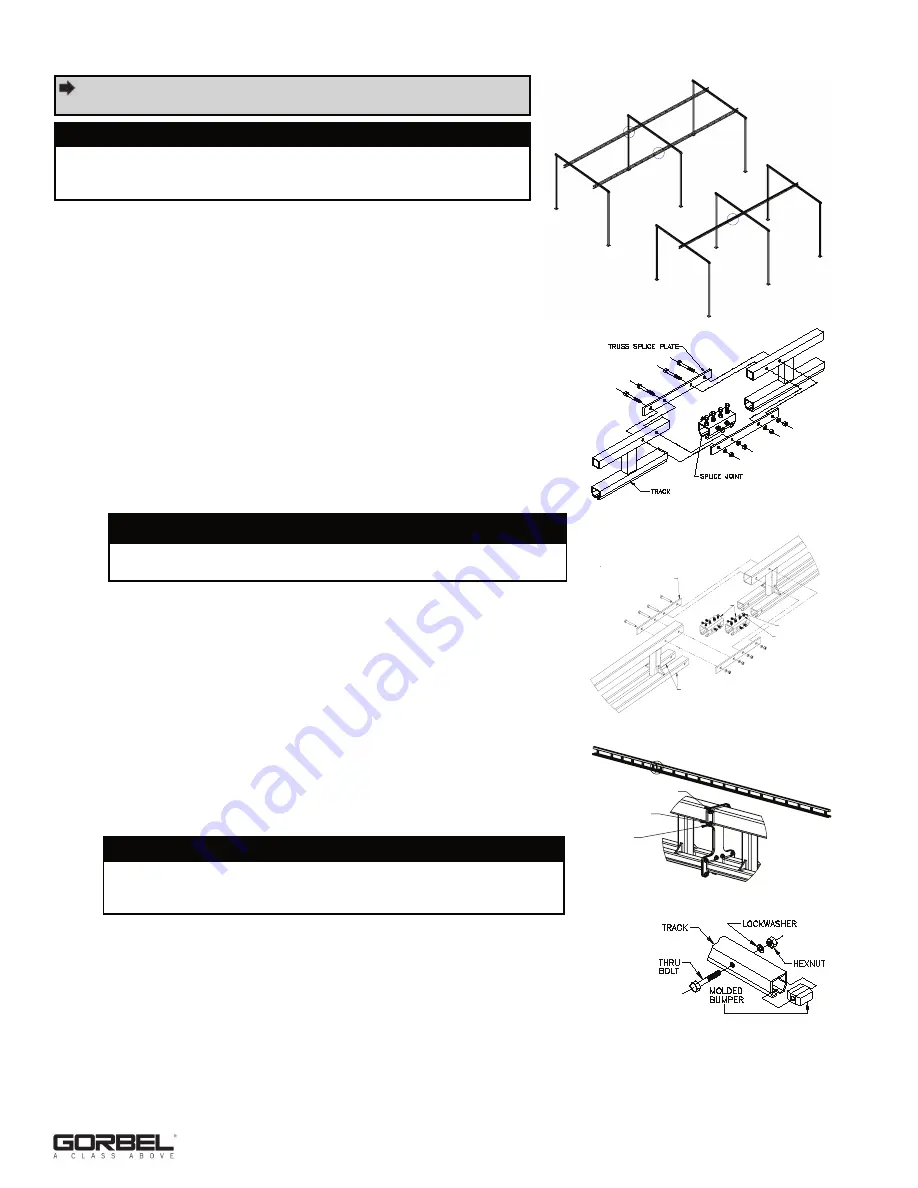
STEP 4 - RUNWAY OR MONORAIL INSTALLATION (CONTINUED)
4.8
Place a truss splice plate on each side of runway truss tube and bolt
into place, as shown in
diagram 4C
or
4D
. “Hand- tighten” bolts.
Note:
Do not torque bolts until track has been attached to header
weldment and adjusted for smooth transition - Steps 4.9 through 4.10.
4.9
To attach track to header weldment, repeat Steps 4.2 through 4.4,
on page 7.
4.10
To adjust track for smooth transition, use bolts along
top of splice joint
to force track down onto lower flanges of splice. Check to see that
transition from one track to the other is smooth: no raised areas to inhibit
trolley or end truck operation. Use bolts along the
sides of splice joint
to
align track laterally. Check to see that track portion of runway is
horizontally and vertically flush: transition from one track to the other is
smooth. Tighten jam nuts to lock bolts in place (refer to
diagram 4C
or
4D
).
Note:
Track running-surface misalignment at joints shall be adjusted
within 1/32” (1mm) when installed.
4.11
Tighten nuts on truss splice plate to full compression of lockwasher, do
not exceed 40 ft.-lbs.
For Z and ZD tracks:
4.12
Refer to the General Arrangement Drawing to plan the sequence in
which the monorail sections will be installed. Monorail sections that have
splice plate style connections (Z and ZD styles) may need to be
assembled to the mating monorail section prior to lifting and installing on
the headers. Do not lift greater than two assembled (splice plate style
connection only) monorail sections at a time. Do not lift assemblies
greater than 54 feet long. Do not allow more than 13 feet of track to
extend past the header without support. For sleeve and truss plate style
connections (S, SL, SLX and SLD styles), only lift these sections
individually (not assembled).
4.13
Splice Joint Plate Style Connections:
Align mating monorail sections and install
hardware (
diagram 4E
). Verify track flanges (trolley wheel running surfaces) are aligned
before tightening. Run a finger on the inside of the track flange and use a soft blow
mallet to align plates until no lip is felt. Also check alignment of mating sections for bow
and camber. Steel shims (by others) may be used between the splice plates to adjust
any misalignment. Tighten hardware to 50 ft.-lbs. of torque per nut.
4.14
Repeat Steps 4.6 through 4.11 for remaining runways.
4.15
Install end stops as shown in
diagram 4F
(molded bumper with thru bolt) to one end of runway or monorail
(leaving other end open for bridge or trolley installation). Tighten nut on thru bolt to full compression of
lockwasher.
WARNING
Do not over-tighten bolts on splice joints; this may permanently
deform track and cause binding.
IMPORTANT:
To install additional runway sections, runways
must be spliced together.
Diagram 4C.
Splicing tracks together.
Diagram 4F.
Installing end stop.
8
9/18 Rev C
WARNING
Do not deviate from the dimensions specified in the General
Arrangement Drawing for maximum space from header center to
splice joint. Typically 48” maximum.
JAM NUT
TRUSS SPLICE PLATE
CLAMPING BOLT
DUAL TRACK
SPLICE JOINTS
Diagram 4D.
Splicing dual trussed track.
1/2"-13 X 1-1/2" HHCS
FLAT WASHER
LOCK NUT
Diagram 4E.
Plate style splice joint detail.
WARNING
The locations of the runways cannot deviate from the locations
shown on the drawing. Changing the locations will void the design
and the warranty.