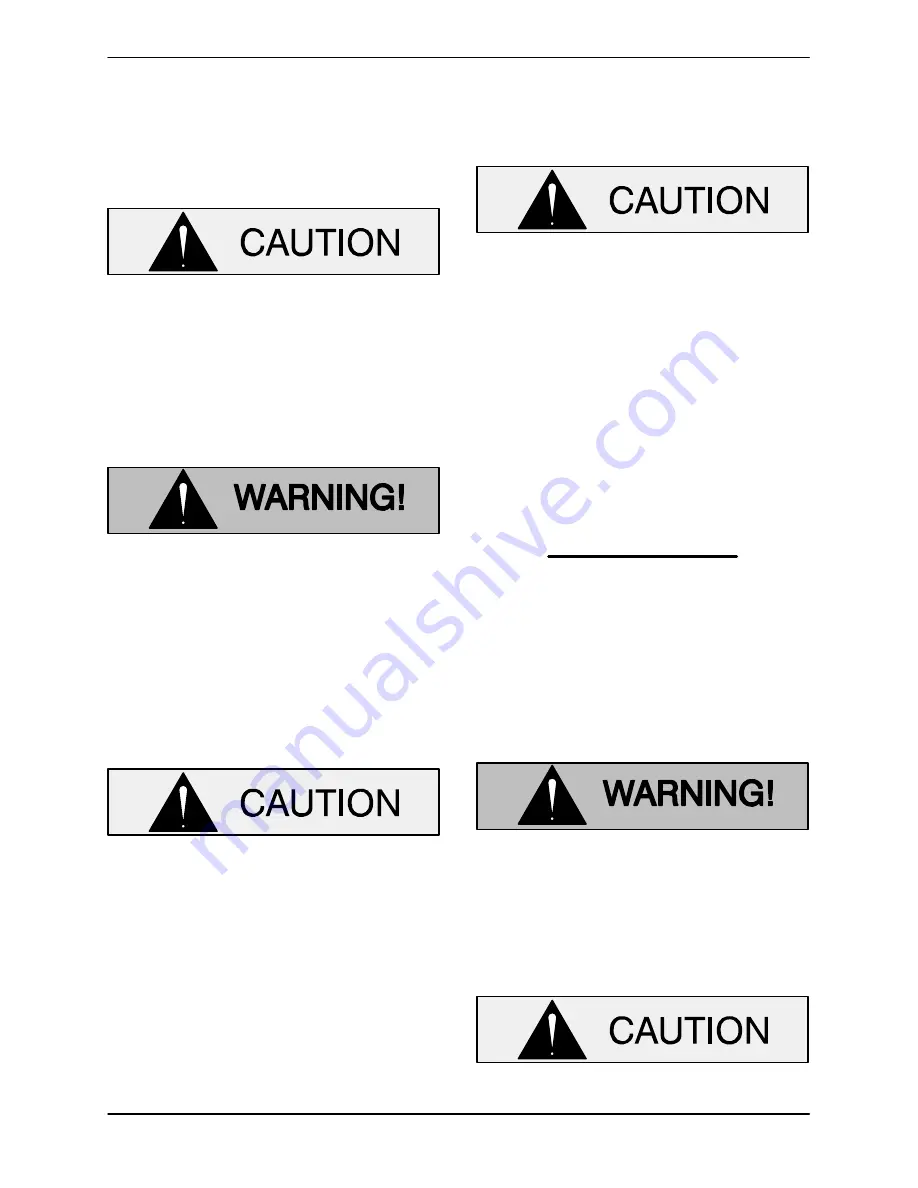
VGH SERIES
OM-06114
MAINTENANCE & REPAIR
PAGE E - 6
outboard bearing (19) from the shaft. Remove the
inboard bearing spacer (21).
After removing the shaft and bearings, clean and
inspect the bearings as follows.
It is
strongly
recommended that the bear
ings be replaced
any
time the shaft and
bearings are removed.
Clean the bearing housing, shaft and all compo
nent parts (except the bearings) with a soft cloth
soaked in cleaning solvent. Inspect the parts for
wear or damage and replace as necessary.
Most cleaning solvents are toxic and
flammable. Use them only in a well ven
tilated area free from excessive heat,
sparks, and flame. Read and follow all
precautions printed on solvent contain
ers.
Clean the bearings
thoroughly in
fresh
cleaning
solvent. Dry the bearings with filtered compressed
air and coat with light oil.
Bearings must be kept free of all dirt and
foreign material. failure to do so will greatly
shorten bearing life.
Do not
spin dry bear
ings. This may scratch the balls or races
and cause premature bearing failure.
Rotate the bearings by hand to check for rough
ness or binding and inspect the bearing rollers and
balls. If rotation is rough or the bearing rollers or
balls are discolored, replace the bearings.
Replace the bearings, shaft, or bearing housing as
required if the proper bearing fit is not achieved.
Shaft and Bearing Reassembly And Installation
Clean and inspect the bearings as indicated in
Shaft and Bearing Removal and Disassembly
.
It is
strongly
recommended that the bear
ings be replaced
any
time the shaft and
and bearings are removed.
The outboard bearing (19) and the inner race of the
inboard bearing (31) may be heated to ease instal
lation. An induction heater, hot oil bath, electric
oven, or hot plate may be used to heat the bearing.
Bearings should
never
be heated with a direct
flame or directly on a hot plate.
NOTE
If a hot oil bath is used to heat the bearing, both the
oil and the container must be
absolutely
clean. If
the oil has been previously used, it must be
thor
oughly
filtered.
Install the inboard bearing spacer (21).
Heat the outboard bearing and inner race of the in
borad bearing (31) to a uniform temperature
no
higher than
250
_
F (120
_
C), and slide the bearings
it onto the shaft, one at a time, until fully seated.
This should be done quickly, in one continuous
motion, to prevent the bearings from cooling and
sticking on the shaft.
Use caution when handling hot bear
ings to prevent burns.
After the bearings have been installed and allowed
to cool, check to ensure that they have not moved
out of position in shrinking. If movement has oc
curred, use a suitably sized sleeve and a press to
reposition the bearings.
When installing the bearings onto the
shaft,
never
press or hit against the outer