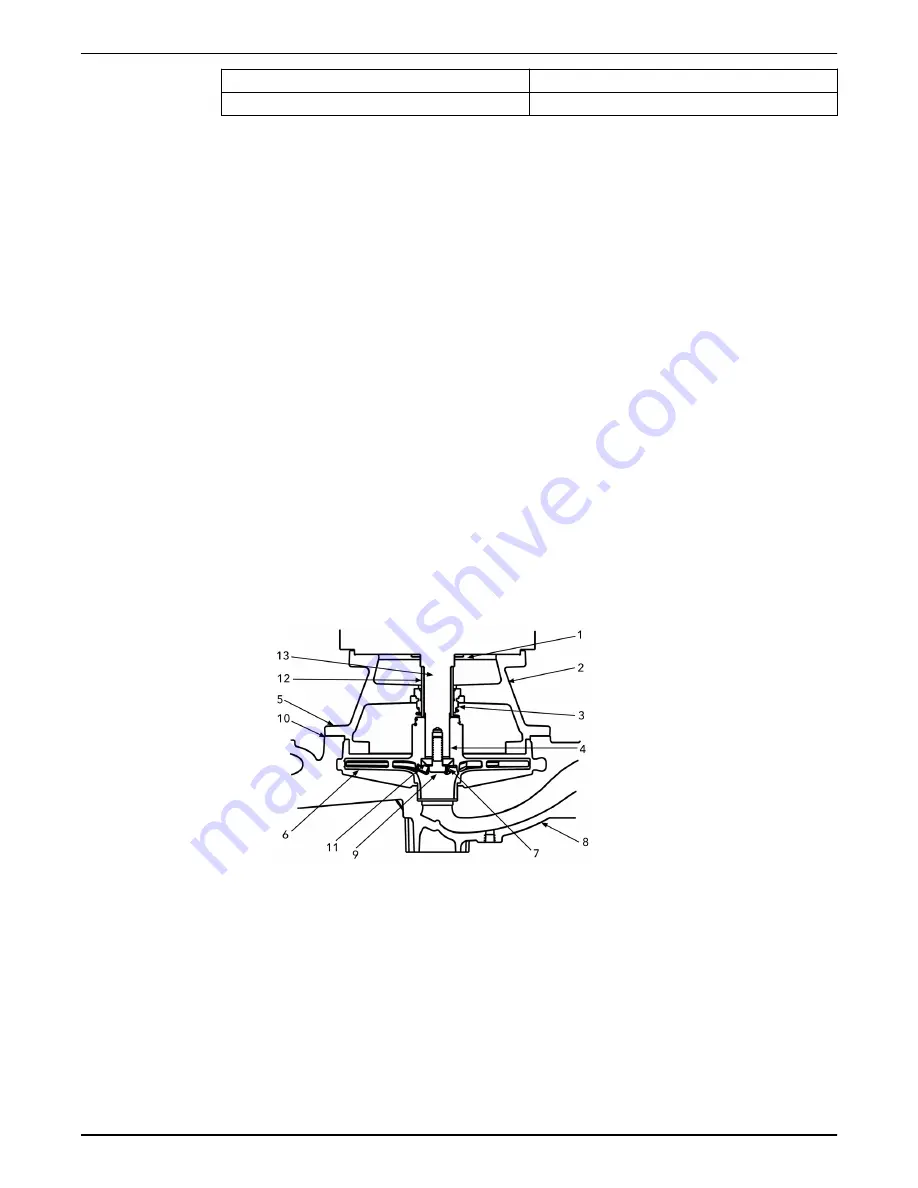
Impeller parts
When to replace
Vane edges
When you see cracks, pitting, or corrosion damage
Gaskets, O-rings, and seats replacement
• Replace all gaskets and O-rings at each overhaul and disassembly.
• Inspect the seats. They must be smooth and free of physical defects.
6.3.2 Shaft inspection
Inspection criteria
Inspect the shaft according to this criteria:
• Thoroughly clean the shaft .
• Thoroughly clean the coverplate seal cavity.
• Inspect the surface for damage such as pitting, corrosion, nicks, and scratches.
Replace these parts if they are damaged.
6.4 Reassembly
6.4.1 Assemble the standard mechanical seal (e-1500-F)
1. Lubricate the shaft sleeve and coverplate seal cavity with soapy water.
Do not use a petroleum lubricant.
2. Install a new insert gasket.
3. Install a new seal insert and make sure that the indentation is against the insert gasket.
4. Slide a new rotating seal assembly onto the shaft sleeve.
5. Push the top of the compression ring with a screwdriver until the seal is tight against
the seal insert.
6. Install the seal spring and point the narrow end toward the seal.
1. Slinger
2. Bracket coverplate
3. Seal assembly
4. Impeller key
5. Volute capscrew
6. Impeller
7. Impeller lockwasher
8. Volute
9. Impeller capscrew
10.Volute gasket
11.Impeller washer
12.Shaft sleeve
13.Shaft
Figure 11: Standard mechanical seal
6 Maintenance
Series e-1500 INSTRUCTION MANUAL
23
Summary of Contents for e-1500 Series
Page 1: ...INSTRUCTION MANUAL P2002884 Rev B Series e 1500 ...
Page 2: ......