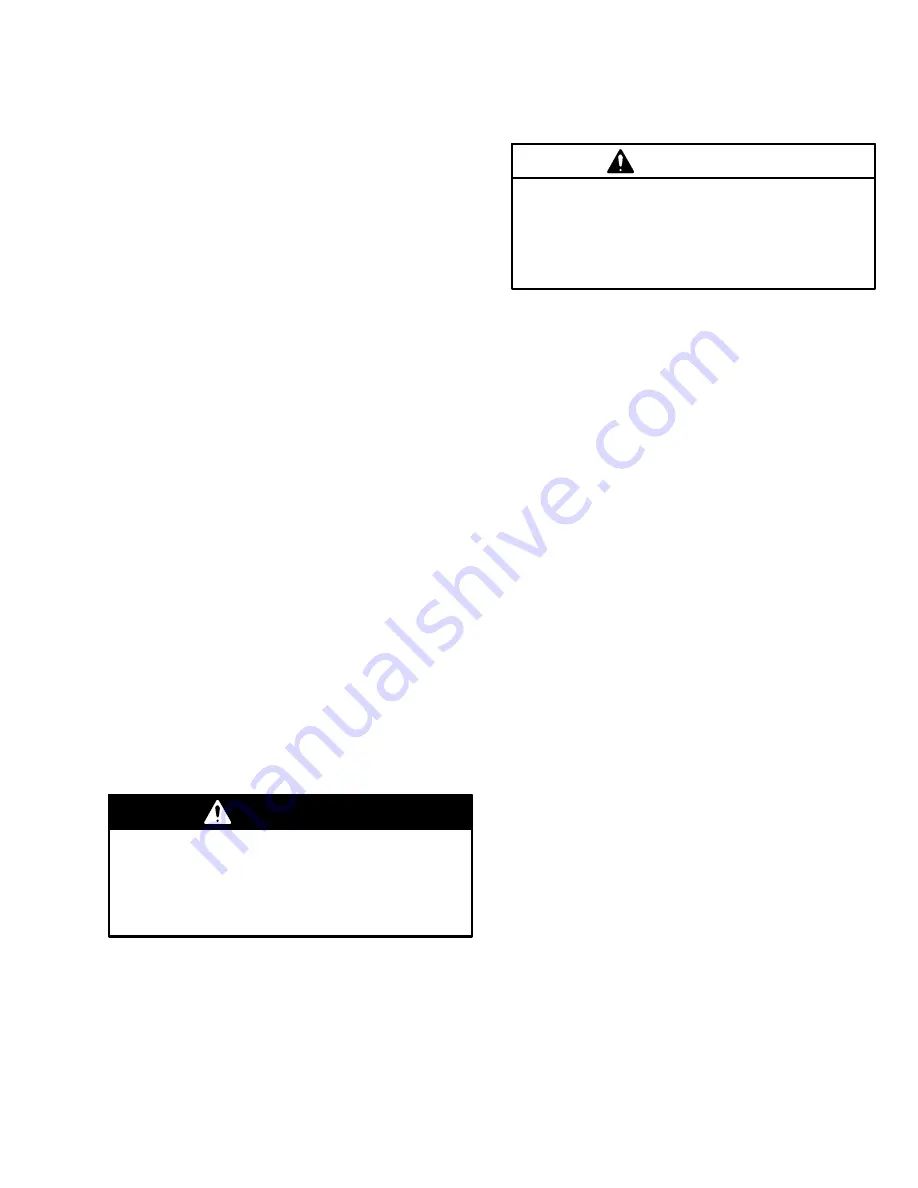
9
308-457
Operation
IV.
Set the fluid and air pressure.
1.
Install the spray tip and air cap on the gun.
2.
Adjust the pump air pressure regulator until the
pressure shown on the fluid filter gauge is about
800 psi (56 bar). This should require approximately
35 psi (2.4 bar) air pressure to the pump.
3.
Test spray a pass or stationary horizontal pattern.
Hold the gun 10 to 12 in. (250 to 300 mm) from the
paper. Stripes in the outer edges of the pass or
spots at the ends of the stationary pattern are
likely at this point.
NOTE: If there are no stripes or spots, lower the
fluid pressure until they appear
before turning on
the air to the gun.
4.
Partially trigger the gun so only air is emitted. Set
the gun air regulator to 20 psi (1.4 bar).
5.
Retest the spray pattern. Trigger the gun and
adjust the gun’s air control valve (C) to add air to
the aircap and to eliminate stripes or spots. If there
are no stripes or spots, you are ready to start
spraying.
6.
If there are stripes or spots in the spray pattern,
raise the pump air pressure until you raise the fluid
outlet pressure by about 100 psi (6.9 bar) and try
again. Continue to raise the fluid pressure in
100 psi (6.9 bar) increments until the pattern is full
and clean. Do not exceed 120 psi (8.3 bar)
incoming air pressure or 2760 psi (190 bar) fluid
working pressure.
NOTE: Always use the lowest fluid and air pres-
sure required for good atomization and spray pat-
tern for maximum fluid efficiency. Air pressure over
approximately 30 psi (2.1 bar) will cause turbu-
lence in the fan pattern, dirty air caps and slower
production capability.
WARNING
This system has a maximum air working pressure
of 120 psi (8.3 bar) which produces a maximum
fluid working pressure of 2760 psi (190 bar). Higher
pressure can cause the system to rupture or mal-
function and result in serious injury.
V.
You are now ready for production
spraying.
CAUTION
When using catalyzed fluids, observe the pot life
as recommended by the fluid manufacturer. Always
flush the system before the pot life has expired to
prevent dried fluid which may be difficult to clean
out and may damage the system.
VI.
When to shut down the system.
Shut down the system at the end of the work shift and
before checking, adjusting, cleaning or repairing the
system. Always follow the Pressure relief procedure
on page 8.