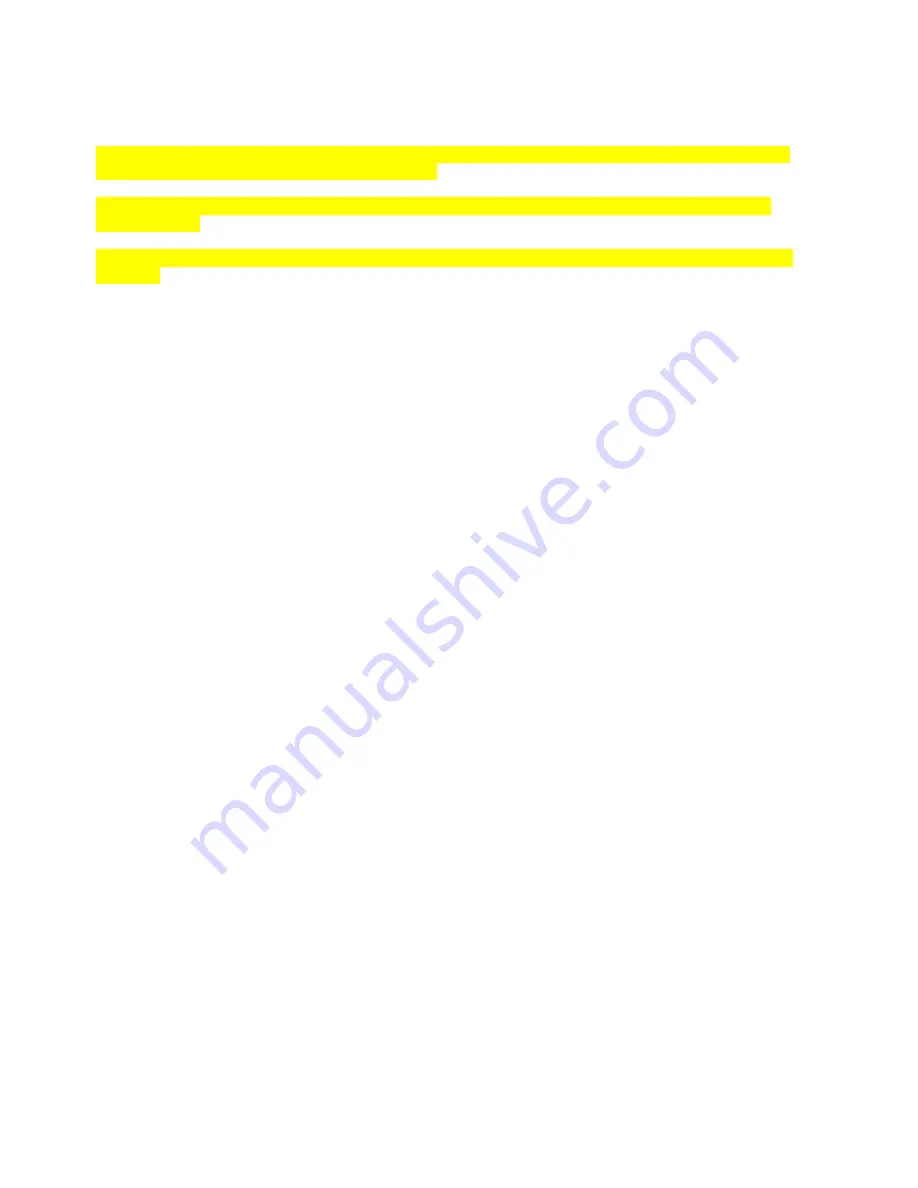
Cartridge Replacement
Warning:
Do not exceed 100 psi (6.9 bar) air pressure to the reservoir extend side of the ram, or 100 psi
(6.9 bar) air pressure on the retract side of the ram.
Caution:
Raise the slide valve towards the regulator; this will release the air pressure from the extend
side of the ram.
Note:
It is not necessary to turn the air supply off at the air source, or disconnect the air supply line to the
regulator.
Move the slide valve towards the regulator
(up typical)
.
This relieves air pressure from the extend side of
the ram, and relieves material outlet pressure.
Apply retract air pressure to the retract air port of the ram, this will send the ram into the up position
releasing pressure on the cartridge retainer. Remove the material hose from the red fitting1/4-inch female
FNPT fitting on the bottom of the plastic cartridge. Remove red outlet fitting from cartridge.
Loosen the four retaining knobs and swing them down and away from the reservoir cap. Slide the retainer
ring and the retainer down, away from the reservoir cap.
Insert the cartridge into the retainer. Slide the retainer and the retainer ring back up to the reservoir cap.
Align the slots in the reservoir cap with the hold-down links. Move the four retaining knobs up to their
retaining position. Tighten these retaining knobs securely. Insert the red outlet fitting to the material
cartridge;
do not apply PTFE tape or pipe sealant and hand tighten only
. Install the material hose to
the red fitting1/4-inch female FNPT fitting on the bottom of the plastic cartridge. Remove air pressure from
the retract side of the ram. Move the slide valve away from the regulator (down typical) to pressurize the
extend ram. Apply the material pressure air to the extend side of the ram; increase the pressure to 20 psi
(1.4 bar) to start. Check all air fittings and the retainer for leaks. Purge the dispense valve until the desired
flow rate is achieved.
The cartridge retainer is ready to be placed in service.
You must adjust the pressure to the extend ram according to the type of material being dispensed. Too
low a pressure will give an inconsistent dispensed volume because the dispense valve does not fill
completely during cycling. Too high a pressure may cause material separation or packing. Use the
minimum pressure needed to get smooth material flow during the purge cycle.
Cleanup
Clean all aluminum parts with a suitable solvent. Do not damage the o-ring that is inside of the pusher
drive cylinder.
4
Summary of Contents for 24H683
Page 14: ...Hall Sensor Information 14 ...