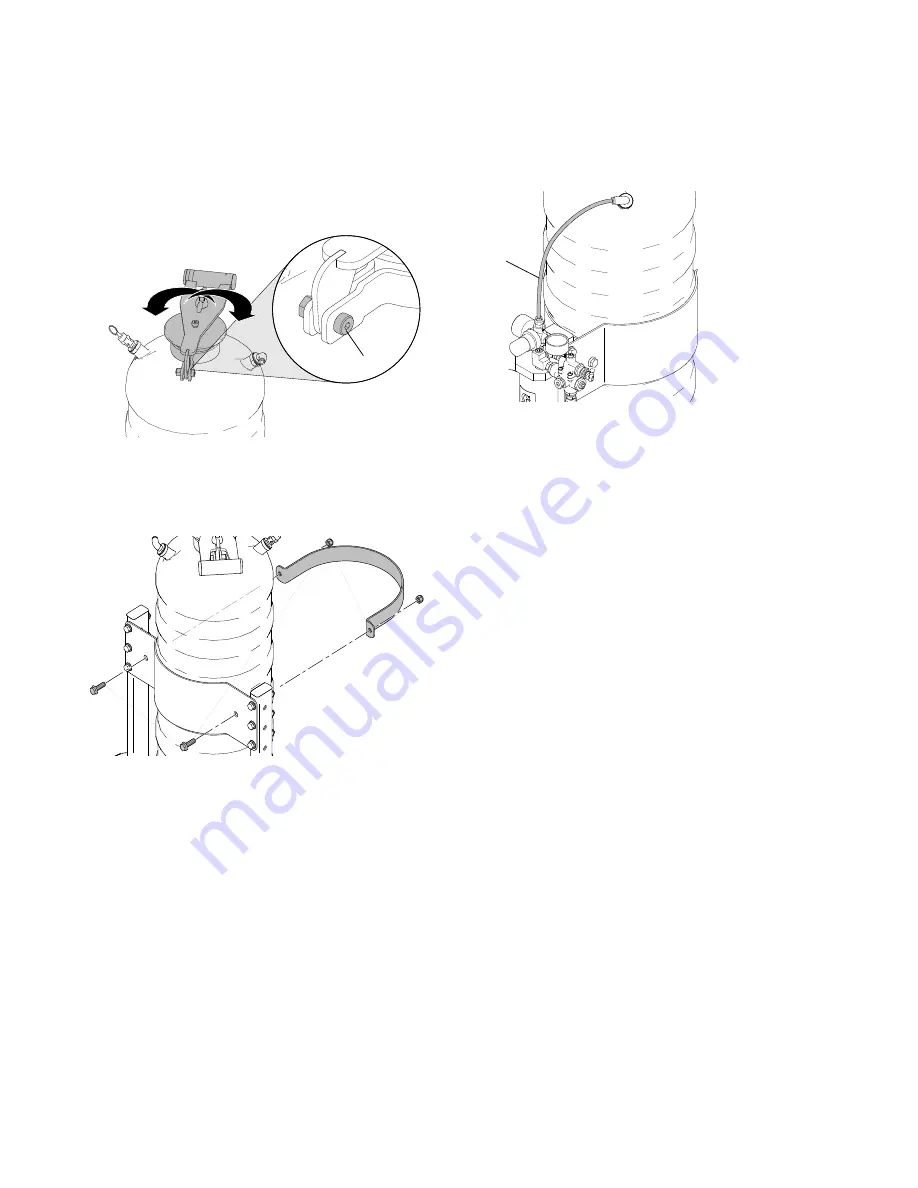
LL200 Compressor Installation
16
332230P
Bead Tank Mounting
1. Place bead tank on supporting base with outlet fit-
tings facing compressor.
NOTE:
Position handle to best suit filling needs.
Loosen bolt (aa) to help swivel, then retighten.
2. Place clamping band around tank and secure with
mounting hardware shown below. Tighten until
there is no movement between clamp and bead
tank.
NOTE:
The flats on the clamp are not intended to
touch the hopper bracket when tightened.
3. Install 36 in. nylon air line (dd) from top of regulator
to swivel fitting on top of bead hopper. Cut air line to
desired length. Push air line into fitting until end
touches bottom of fitting.
ti20704a
aa
ti21193a
ti21195a
dd