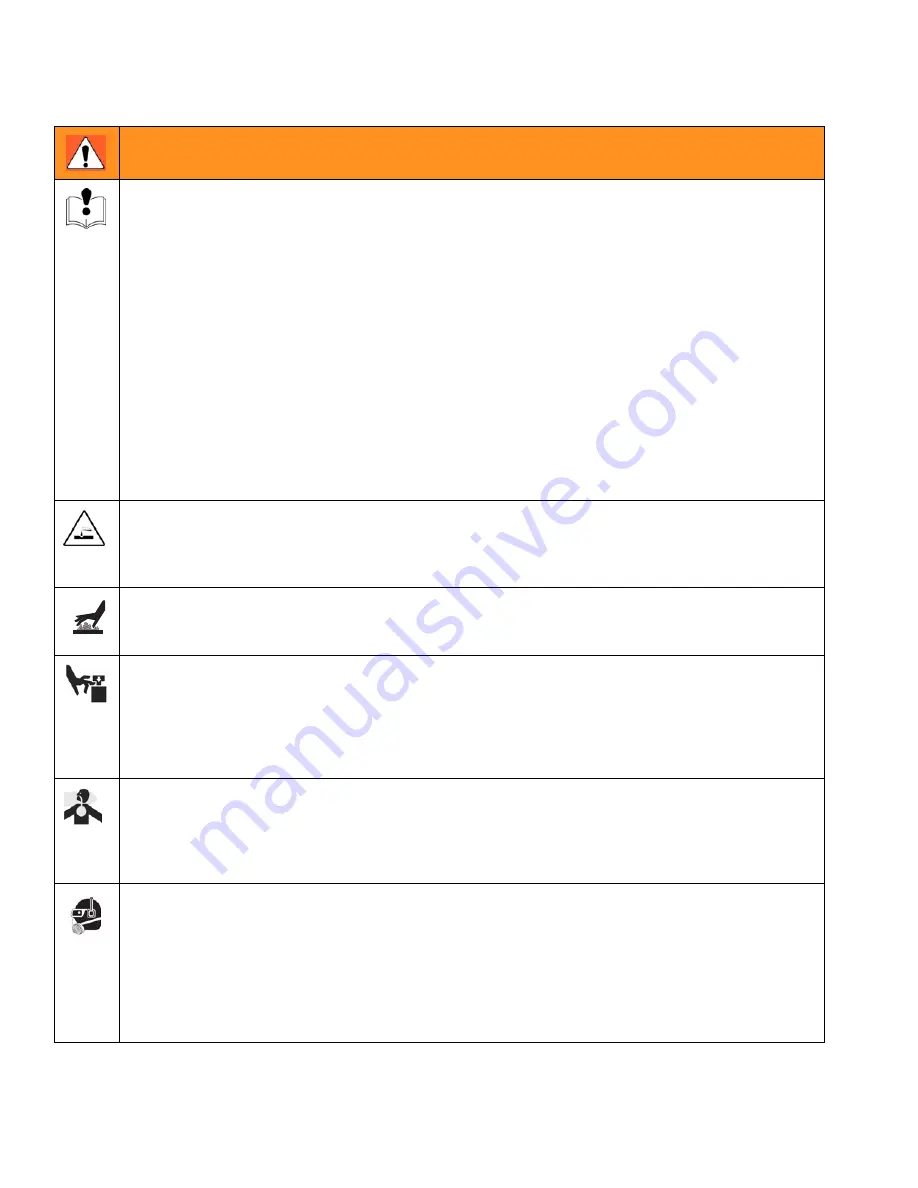
Warning
4
311737B
WARNING
EQUIPMENT MISUSE HAZARD
Misuse can cause death or serious injury.
•
Do not exceed the maximum working pressure or temperature rating of the lowest rated system
component. Read
Technical Data
in all equipment manuals.
•
Use fluids and solvents that are compatible with equipment wetted parts. Read
Technical Data
in all
equipment manuals. Read fluid and solvent manufacturer’s warnings. For complete information
about your material, request MSDS from distributor or retailer.
•
Check equipment daily. Repair or replace worn or damaged parts immediately with genuine Graco
replacement parts only.
•
Do not alter or modify equipment.
•
Use equipment only for its intended purpose. Call your Graco distributor for information.
•
Route hoses and cables away from traffic areas, sharp edges, moving parts, and hot surfaces.
•
Do not kink or overbend hoses or use hoses to pull equipment.
•
Keep children and animals away from work area.
•
Comply with all applicable safety regulations.
•
Keep children and animals away from work area.
•
Do not operate the unity when fatigued or under the influence of drugs or alcohol.
PRESSURIZED ALUMINUM PARTS HAZARD
Do not use 1,1,1-trichloroethane, methylene chloride, other halogenated hydrocarbon solvents or fluids
containing such solvents in pressurized aluminum equipment. Such use can cause serious chemical
reaction and equipment rupture, and result in death, serious injury, and property damage.
BURN HAZARD
Equipment surfaces can become very hot during operation. To avoid severe burns, do not touch hot
equipment. Wait until equipment has cooled completely.
MOVING PARTS HAZARD
Moving parts can pinch or amputate fingers and other body parts.
•
Keep clear of moving parts.
•
Do not operate equipment with protective guards or covers removed.
•
Pressurized equipment can start without warning. Before checking, moving, or servicing equipment,
follow the
Pressure Relief Procedure
in this manual. Disconnect power or air supply.
TOXIC FLUID OR FUMES HAZARD
Toxic fluids or fumes can cause serious injury or death if splashed in the eyes or on skin, inhaled, or
swallowed.
•
Read MSDS’s to know the specific hazards of the fluids you are using.
•
Store hazardous fluid in approved containers, and dispose of it according to applicable guidelines.
PERSONAL PROTECTIVE EQUIPMENT
You must wear appropriate protective equipment when operating, servicing, or when in the operating
area of the equipment to help protect you from serious injury, including eye injury, inhalation of toxic
fumes, burns, and hearing loss. This equipment includes but is not limited to:
•
Protective eye wear
•
Clothing and respirator as recommended by the fluid and solvent manufacturer
•
Gloves
•
Hearing protection
Summary of Contents for 390 253958
Page 30: ...Notes 30 311737B Notes...